E-pos: [email protected]
What are the causes of damage to the jaw crusher plate?
Because it is under tremendous pressure during material processing, there are many causes for the damage of the jaw crusher plate. Understanding why they degrade prematurely can save costs and downtime. Let’s explore real-world causes of damage to the jaw crusher plate and solutions.
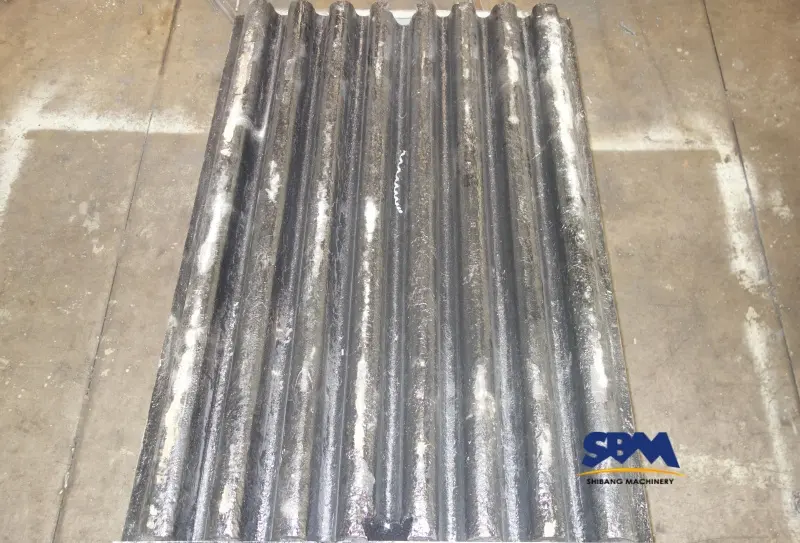
1. Material Hardness Mismatch: A Silent Plate Killer
A quarry in Texas reported rapid jaw plate wear while crushing granite. Analysis revealed the plates were designed for softer limestone. Harder materials like granite create excessive abrasion, accelerating cracks and fractures.
Oplossing: Match plate material hardness to the processed rocks. For mixed feeds (e.g., concrete crusher operations), manganese steel plates often outperform standard options.
2. Improper Feeding Practices: More Than Just a Loading Error
A Swedish mining site faced uneven plate wear due to irregular feeding. Operators frequently overloaded one side of the C6X jaw crusher, causing asymmetrical stress distribution.
Key Fixes:
- Follow jaw crusher feeding tips like using vibratory feeders for consistency.
- Avoid oversized materials exceeding the crusher’s intake capacity.
3. Incorrect Plate Design: Geometry Matters
An Australian contractor using a recycled concrete crusher noticed premature plate failure. The issue? Flat-profile plates struggled with angular demolition waste, increasing friction.
Optimization Strategy:
- Opt for curved or corrugated jaw plate selection to reduce sliding friction.
- Consult manufacturers for site-specific profiles.
4. Moisture & Corrosion: The Hidden Aggressor
Coastal operations in Japan saw plates rusting within months. Saltwater exposure combined with wet aggregates caused corrosion pits, weakening structural integrity.
Prevention Methods:
- Apply anti-corrosion coatings for humid environments.
- Store spare plates in dry conditions.
5. Overlooking Maintenance Intervals
A German recycling plant ignored jaw crusher output size changes caused by worn plates. Continued operation led to secondary damage in the crushing chamber.
Proactive Steps:
- Monitor particle size regularly to detect plate wear early.
- Schedule plate rotation/replacement based on tonnage logs.
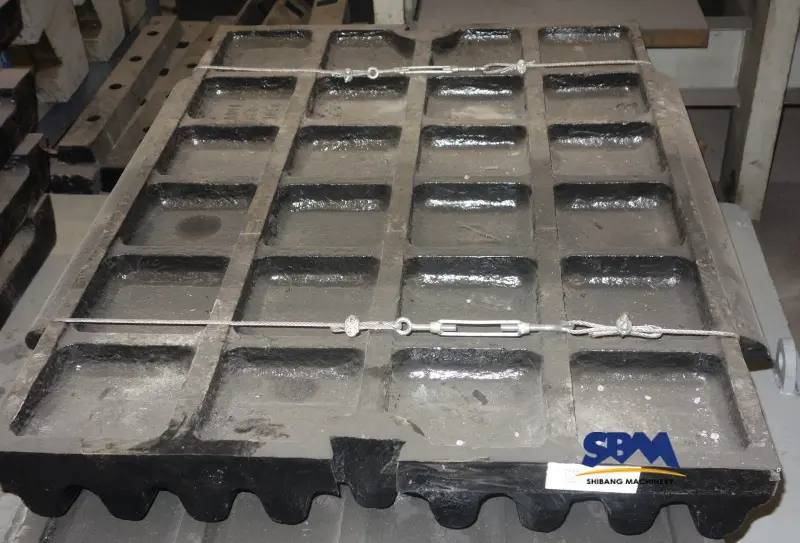
Global Case Study: Extending Plate Life in Canadian Iron Ore Mining
Challenge: A C6X jaw crusher processing iron ore required plate replacements every 6 weeks.
Diagnose: Abrasive ore + frequent tramp metal incidents caused gouging.
Outcome: Switching to tungsten-carbide-enhanced plates and installing metal detectors increased lifespan to 14 weeks.
How to Minimize Jaw Crusher Plate Damage: Action Checklist
- Material Testing: Analyze feedstock hardness before plate selection.
- Feed Control: Use pre-screening to remove uncrushables.
- Smeer: Ensure timely greasing of pivot points.
- Alignment Checks: Verify plate positioning during jaw crusher maintenance.
Hoofkwartierkantoor
Whatsapp:+8615225176731
E-pos: [email protected]
Adres: Geen. 1688, Gaoke East Road, Pudong nuwe distrik, Sjanghai, Sjina.
Webwerf: https://www.mill-sbm.com/
Artikelinhoud
Onlangse plasings
- What are the causes of damage to the jaw crusher plate?Because it is under tremendous pressure during material processing, there are many causes for the damage of the jaw crusher plate. Understanding why they degrade prematurely can save costs and…
- What is the ideal jaw crusher for granite crushing?Granite’s relentless toughness demands jaw crusher built to endure—think armored jaws and unyielding frames. Prioritize crushers that combine brute force with precision engineering, like heat-treated alloys and adaptive crushing chambers.…
- Jaw Crusher for Limestone Processing: A Guide to EfficiencyAs limestone is widely used in construction and industry, its processing requires strong and durable jaw crusher to meet the needs of the industry. Among the many crushers, the jaw…