Email: [email protected]
Beyond Rocks: The Surprising Materials Jaw Crushers Can Process
While “rock crusher” might conjure images of granite mountains, new jaw crushers process materials that would surprise even seasoned engineers. Let’s examine their true capabilities through global operational data and unconventional use cases.
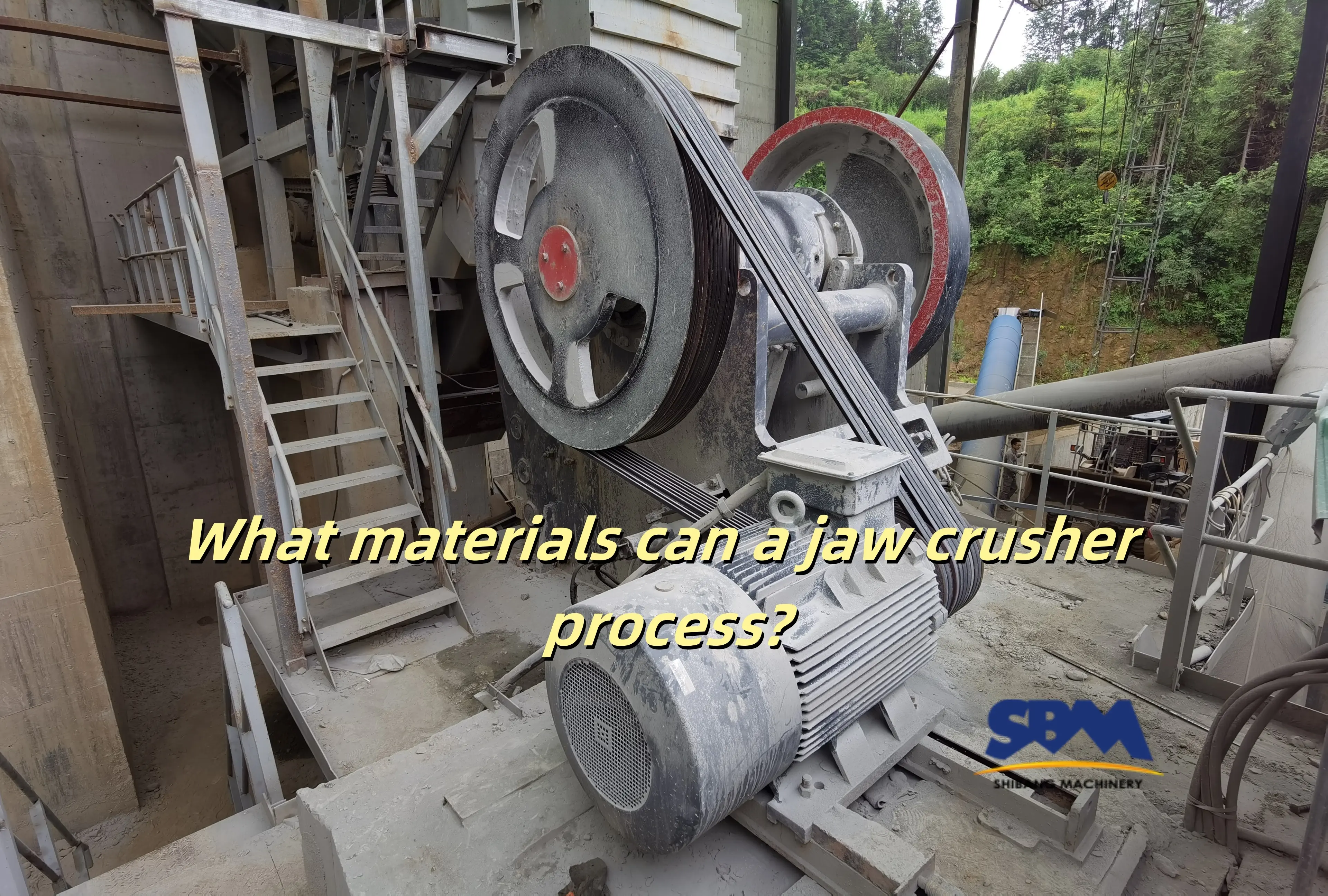
Material Mastery: From Quarries to Urban Mines
1. Geological Heavyweights
Jaw crushers demonstrate remarkable versatility across geological formations:
- Volcanic basalt (320-350 MPa strength): Essential for Dubai’s Burj Khalifa foundations
- Metamorphic quartzite: Primary material for solar silica production in Nevada’s Tesla Gigafactory
- Sedimentary limestone: Processes 1,200 TPH at Mexico’s Cancún coastal protection project
Case Study: Norway’s Larvikite quarries use C6X jaw crushers to achieve 0.5-2″ spec aggregates for Arctic road construction, withstanding -40°C operational temps.
2. Metallurgical Challenges
Beyond conventional ore materials, jaw crushers process:
- Lateritic nickel ore (Philippines) with 12% moisture content
- Platinum-bearing UG2 reef (South Africa) requiring special wear-resistant liners
- Bauxite processing in Jamaica’s humid conditions (85% RH tolerance)
Pro Tip: You can visit this to see more information about Some Kinds of Ore Raw Materials and Finished Stone Materials.
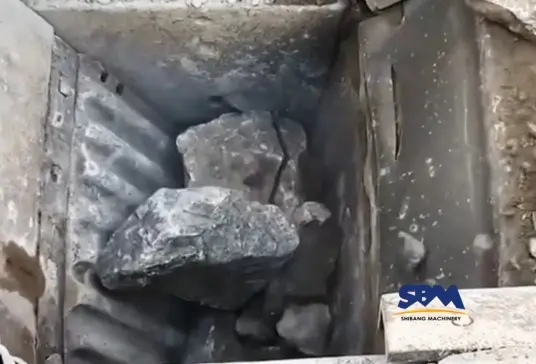
Recycling Revolution: Urban Material Rebirth
From Demolition to Reconstruction
- Concrete Recycling: Berlin’s circular economy project achieves 98% materials reuse:
- Input: 24″ thick demolition slabs
- Output: 3/4″ clean aggregate via hydraulic jaw adjustment
- Metal recovery: 2.3 tons/hour ferrous extraction
Unconventional Inputs
- Shipbreaking steel (Chittagong, Bangladesh)
- Railway sleeper concrete (UK’s HS2 project)
- Decommissioned runway asphalt (LAX Airport redevelopment)
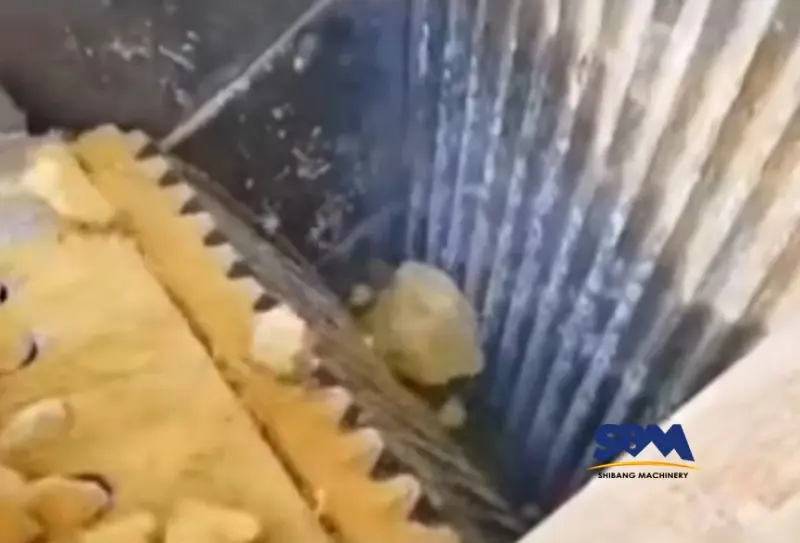
Size Matters: Precision Crushing Strategies
Optimal Output Ranges
Material Type | Feed Size | Discharge Range | Common Use |
---|---|---|---|
Granite | 24″-36″ | 2″-6″ | Bridge abutments |
Recycled concrete | 18″-24″ | 0.5″-3″ | Road base |
Copper ore | 30″-42″ | 4″-8″ | Heap leaching prep |
Pro Tip: Use wedge adjustment systems for 15% faster size changes compared to traditional shim plates. You can visit Crushed Stone Size Chart for more information.
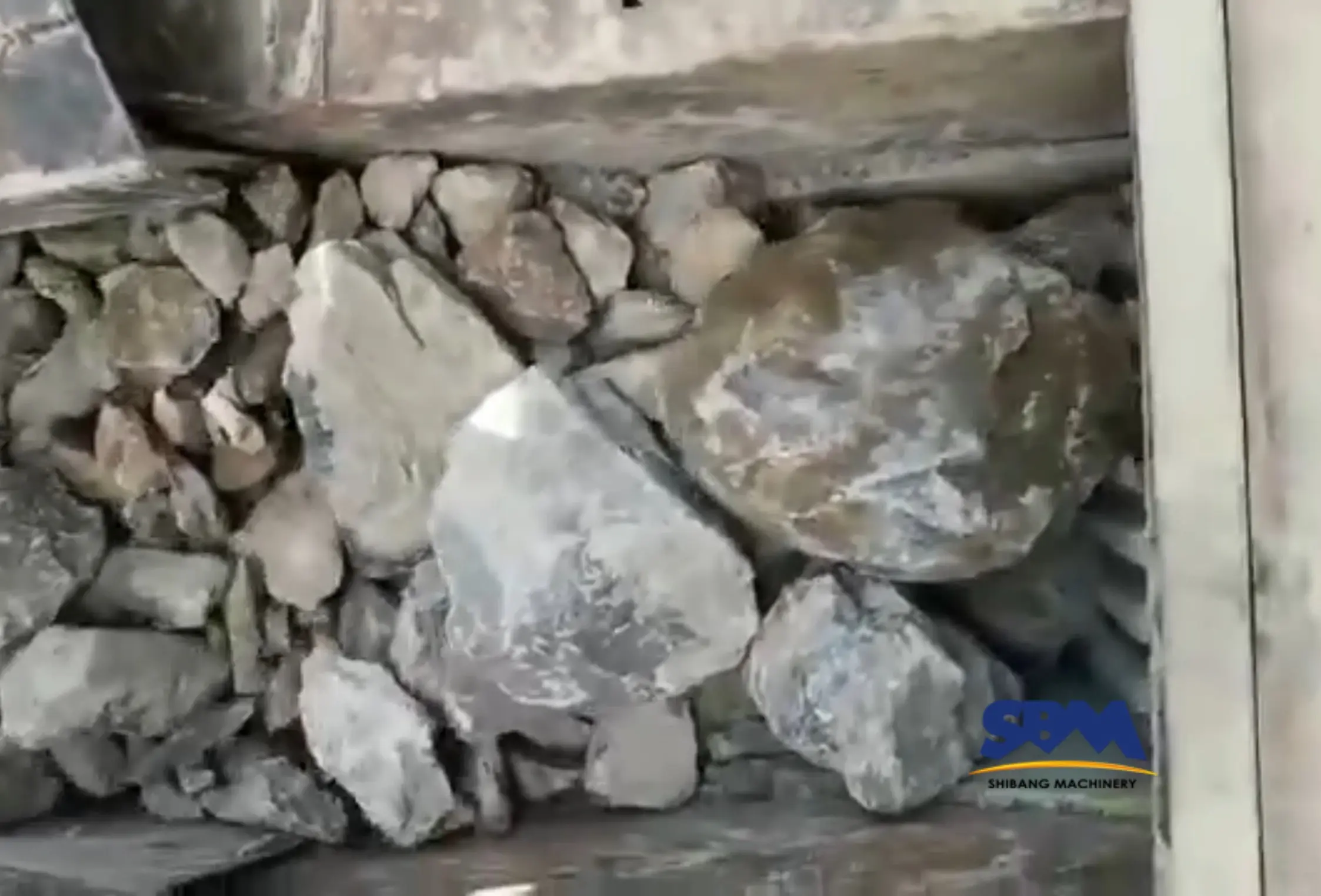
Maintenance Myths vs. Operational Reality
Field-Proven Upkeep Strategies
- Arctic conditions: Synthetic ISO VG 680 oil (-50°C pour point)
- Tropical mines: Water-resistant grease with 8% MoS2 additive
- Wear Part Innovations
- Manganese steel alternatives:
- Ceramic-impregnated plates (40% longer life in abrasive ores)
- Hybrid designs with tungsten inserts for slag processing
- Failure Prevention
- Vibration analysis thresholds:
- 7 mm/s RMS: Immediate shutdown
- 4-6 mm/s: Schedule bearing inspection
The C6X Advantage: Next-Gen Crushing
Latest field data from 12 countries shows:
- 23% energy reduction vs. traditional models
- Auto-tensioning system maintains 0.8-1.2 mm jaw plate gap
- Integrated IoT sensors predict liner wear within ±5% accuracy
From granite quarries to urban recycling centers, jaw crushers process an impressive range of materials. By understanding their capabilities—and adhering to maintenance best practices—operators can maximize efficiency and adapt to evolving industry demands.
Headquaters Office
Whatsapp:+8615225176731
Email: [email protected]
Address: No. 1688, Gaoke East Road, Pudong new district, Shanghai, China.
Website: https://www.mill-sbm.com/
Article Contents
Recent Posts
- How to Choose the Right Jaw Crusher Size for Your Industry?Selecting the right jaw crusher size isn’t a guessing game—it’s a science rooted in material dynamics and operational calculus. For industries from hard-rock mining to urban concrete recycling, even a…
- What are the causes of damage to the jaw crusher plate?Because it is under tremendous pressure during material processing, there are many causes for the damage of the jaw crusher plate. Understanding why they degrade prematurely can save costs and…
- What is the ideal jaw crusher for granite crushing?Granite’s relentless toughness demands jaw crusher built to endure—think armored jaws and unyielding frames. Prioritize crushers that combine brute force with precision engineering, like heat-treated alloys and adaptive crushing chambers.…