Email: [email protected]
Common Jaw Crusher Problems and Solutions: Your Complete Maintenance Checklist
Over 65% of unplanned downtime in jaw crusher operations stems from preventable mechanical issues. This comprehensive guide identifies the 7 most common jaw crusher problems and provides actionable solutions, complete with a maintenance checklist to keep your C6X Jaw Crusher or other models running optimally.
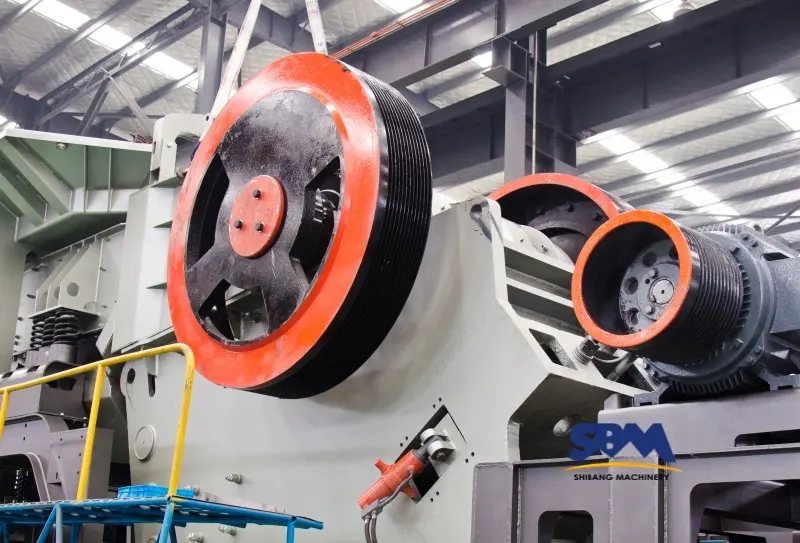
Top 7 Jaw Crusher Issues & Immediate Fixes
1. Uneven Jaw Plate Wear
Symptoms: 30-50% faster wear on one side
Solutions:
- Rotate plates every 200 operating hours
- Check feed distribution with laser alignment
- Upgrade to asymmetric tooth profiles for mixed materials
2. Excessive Vibration
Symptoms: Structural shaking >5mm/s RMS
Root Cause:
- Worn bearings (85% of cases)
- Unbalanced flywheel (12%)
- Loose foundation bolts (3%)
Fix:
- Torque all bolts to 350 N·m specification
- Replace tapered roller bearings using proper installation techniques
3. Low Production Output
Symptoms: Throughput drops >20%
Diagnosis:
Possible Causes | Verification Method | Solution |
---|---|---|
Worn jaw dies | Measure plate thickness | Replace at 60% wear limit |
Incorrect CSS setting | Laser measurement | Adjust to OEM specifications |
Material bridging | Visual inspection | Install grizzly feeder |
4. Hydraulic System Overheating
Symptoms: Oil temperature >80°C
Solutions:
- Clean clogged radiator fins weekly
- Replace hydraulic filters every 500 hours
- Upgrade to synthetic high-temp oil (ISO VG 68)
5. Abnormal Noise During Operation
Sound Types & Meanings:
- Metallic grinding: Worn toggle seats
- Loud banging: Broken toggle plate
- High-pitched squeal: Dry bearings
Action Plan:
- Immediately stop operation
- Inspect components using diagnostic checklist
- Replace damaged parts before restarting
6. Frequent Bearing Failures
Prevention Strategy:
- Use laser alignment for perfect shaft positioning (±0.05mm)
- Implement automatic lubrication systems
- Monitor temperature with wireless IoT sensors
7. Oil Contamination Issues
Contamination Sources:
Contaminant | Max Allowable | Removal Method |
---|---|---|
Dirt particles | ISO 16/13 | Centrifugal filters |
Water | 0.1% volume | Vacuum dehydration |
Metallic debris | >50μm | Magnetic plugs |
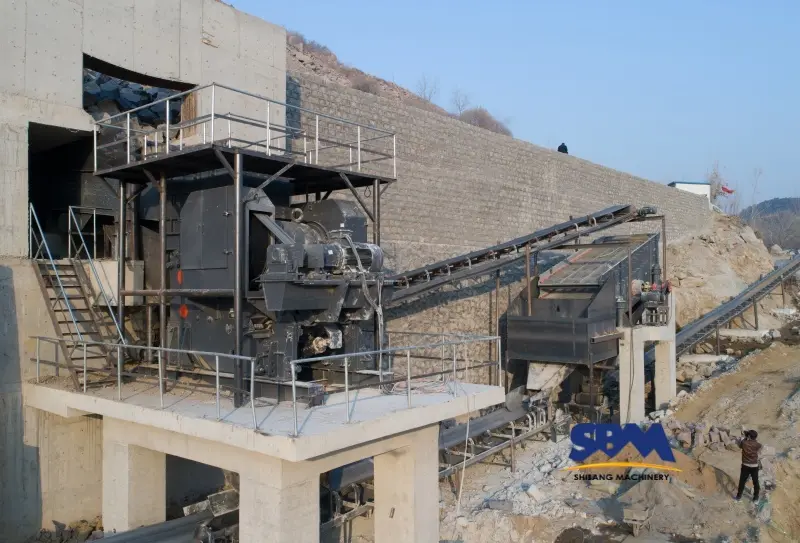
Proactive Maintenance Checklist
Daily Tasks
- Check oil levels and contamination (use patch test)
- Inspect belt tension (deflection <15mm)
Weekly Actions
- Measure CSS with laser gauge
- Test safety interlocks
Monthly Priorities
- Perform vibration analysis (2-5mm/s limit)
- Inspect structural welds for cracks
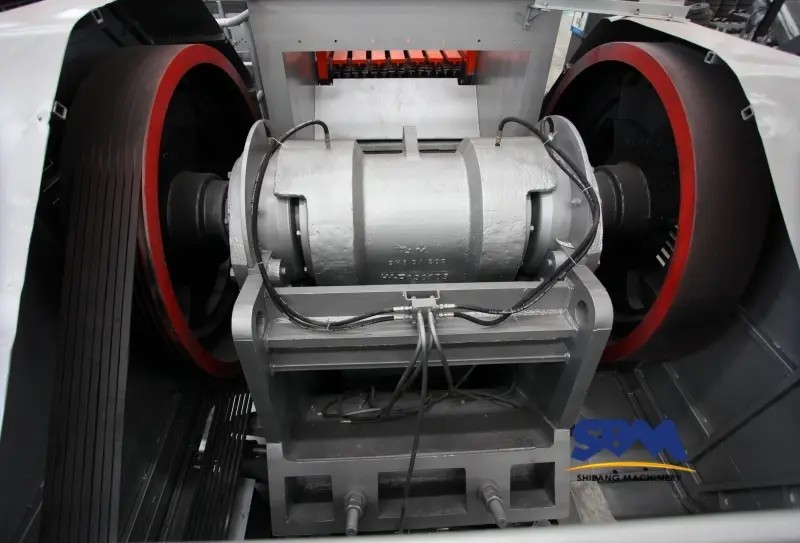
Critical Component Failure Prevention
Toggle Plate Breakage
Early Warning Signs:
- Output size variation >15%
- Unusual clicking during crushing cycles
Prevention: Replace after 800-1200 hours in abrasive conditions
Advanced Monitoring Techniques
- Infrared thermography for bearing health checks
- Vibration analysis (2-5 mm/s RMS threshold)
- Oil debris sensors detecting >50μm particles
When to Seek Professional Help
Contact OEM technicians if experiencing:
- Persistent capacity drops >25% after routine maintenance
- Frame cracks exceeding 2mm width
- Eccentric shaft runout >0.15mm
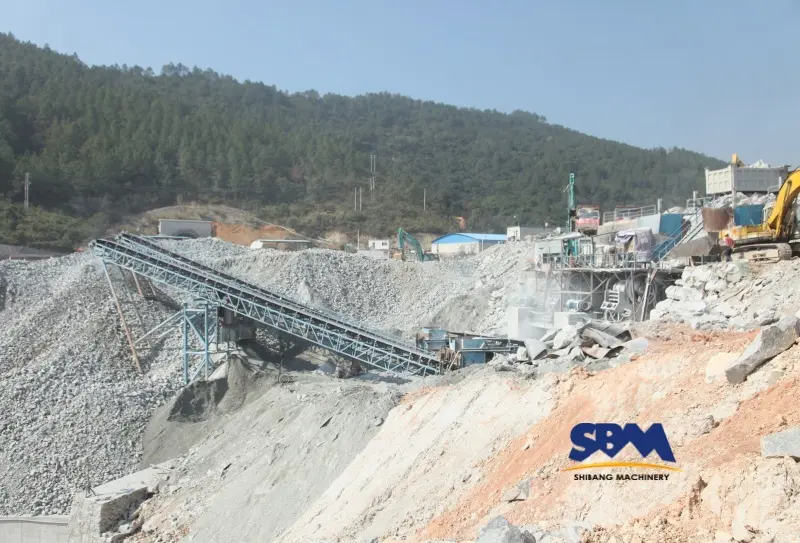
Case Study: Solving Chronic Overheating
A limestone quarry reduced bearing failures by 70% through:
- Upgrading to synthetic high-temp grease
- Installing automatic lubrication systems
- Implementing our monthly inspection protocol
Essential Tools for Effective Maintenance
- Laser alignment kit (±0.1mm accuracy)
- Digital torque wrench (50-500 N·m range)
- Wear measurement calipers
Systematic Prevention Wins
By addressing these common jaw crusher problems through our maintenance checklist, operators achieve >92% uptime. Also, remember: 80% of failures originate from just 20% of components – focus on bearings, jaw plates, and hydraulic systems. Finally, pair this guide with proper operation training for maximum equipment lifespan.
Headquaters Office
Whatsapp:+8615225176731
Email: [email protected]
Address: No. 1688, Gaoke East Road, Pudong new district, Shanghai, China.
Website: https://www.mill-sbm.com/
Article Contents
Recent Posts
- How to Choose the Right Jaw Crusher Size for Your Industry?Selecting the right jaw crusher size isn’t a guessing game—it’s a science rooted in material dynamics and operational calculus. For industries from hard-rock mining to urban concrete recycling, even a…
- What are the causes of damage to the jaw crusher plate?Because it is under tremendous pressure during material processing, there are many causes for the damage of the jaw crusher plate. Understanding why they degrade prematurely can save costs and…
- What is the ideal jaw crusher for granite crushing?Granite’s relentless toughness demands jaw crusher built to endure—think armored jaws and unyielding frames. Prioritize crushers that combine brute force with precision engineering, like heat-treated alloys and adaptive crushing chambers.…