Email: [email protected]
Crushers in Aggregate Production: Key Equipment and Best Practices
Modern construction relies on efficiently processed aggregates, making crushers indispensable in mining and quarrying operations (aggregate production). This guide examines international applications of crushing technology, equipment selection strategies, and maintenance insights through real examples.
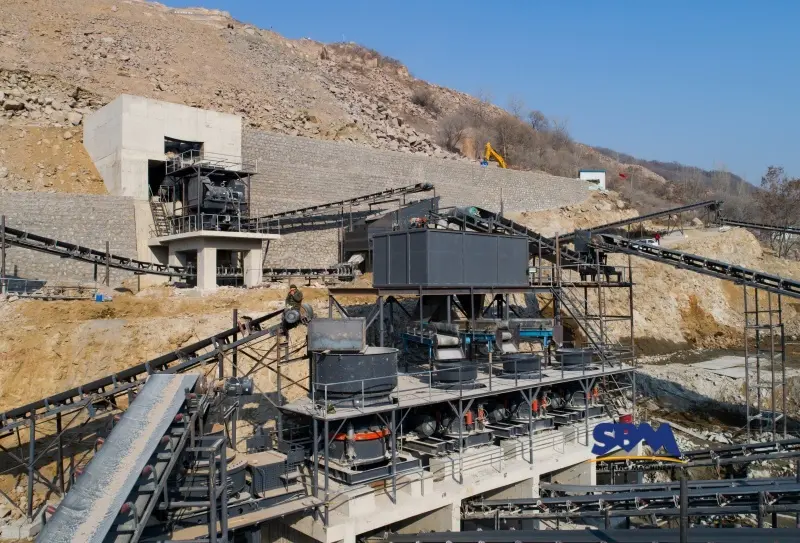
Global Case Studies: Crushing Solutions in Action
1. German Quarry Upgrades to Hybrid Jaw Crushers
The Bavarian Aggregate production Group reduced energy consumption by 22% after implementing jaw crushers with adaptive crushing chambers. Their limestone operation now achieves 650 TPH while maintaining <5% oversize material.
2. Australian Mobile Crushers Revolutionize Remote Sites
Rio Tinto’s Pilbara iron ore project utilizes mobile jaw crushers that process 800 tons/hour. The track-mounted units reduced transport costs by 40% compared to stationary plants.
3. Canadian Recycled Concrete Processing Breakthrough
Toronto’s GreenDemolition Inc. employs impact-jaw combi-crushers to achieve 98% purity in recycled aggregates. Their system recovers 12,000 tons/month of construction waste.
Core Equipment Selection Strategies
Balancing Power and Precision in Crusher Choice
When choosing jaw crushers in aggregate production, consider:
- Feed size vs. gape width ratio (ideal 0.8:1)
- CSS (Closed Side Setting) adjustment range
- Toggle plate safety mechanism types
SBM C6X200 units in Swedish granite quarries demonstrate how 1,200 mm feed openings handle 800-1,000 MPa materials effectively.
Maintenance Mastery: Extending Crusher Lifespan
Smart Liner Management Techniques
Proper jaw crusher liner replacement protocols can increase service life by 30%:
- Monitor wear patterns using 3D scanning (adopted by Chilean copper mines)
- Implement symmetrical rotation schedules
- Use manganese steel alloys (14-18% Mn content)
South African platinum mines report 6-month liner cycles instead of 4-month replacements through optimized maintenance.
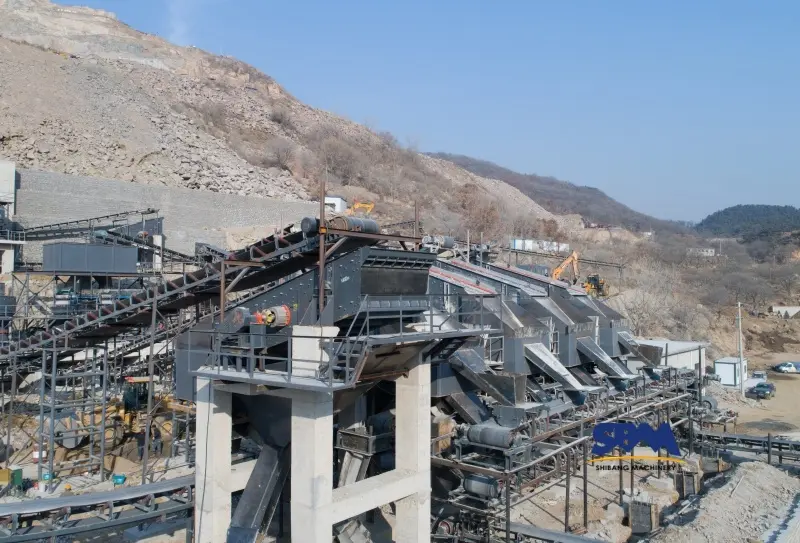
Emerging Technologies Shaping Aggregate Crushing
AI-Powered Crushing Optimization
’s crushing system in Nevada gold mines uses real-time ore analysis to automatically adjust crusher settings, boosting throughput by 18%.
Eco-Crushers: Noise and Dust Reduction
Eco-crushers features:
- 360° dust encapsulation
- 72 dB noise rating (vs standard 110 dB)
- Hybrid diesel-electric power options
Future Outlook:
The global aggregate crushers market in aggregate production (valued at $5.2B in 2023) is projected to grow at 5.8% CAGR through 2030 (Global Market Insights). Mobile and hybrid systems will dominate, particularly in infrastructure projects across Southeast Asia and Africa.
Practical Tip: Always cross-reference crusher capacity charts with actual material bulk density. Volcanic rock operators in Indonesia improved efficiency by 15% after adjusting for 1.8 t/m³ material density vs standard 1.6 t/m³ assumptions.
This comprehensive approach to crushing system design – combining appropriate equipment selection, proactive maintenance, and technology adoption – ensures optimal aggregate production outcomes across diverse operational contexts.
Headquaters Office
Whatsapp:+8615225176731
Email: [email protected]
Address: No. 1688, Gaoke East Road, Pudong new district, Shanghai, China.
Website: https://www.mill-sbm.com/
Article Contents
Recent Posts
- Top 6 Advantages of Mobile Jaw Crushers (And Why They Outperform Fixed Units)Mobile jaw crushers are reshaping the global resource development landscape with multiple advantages such as “plug and play” integrated design and autonomous mobility. From Indonesian volcanic rock quarries to the…
- Single Toggle VS Double Toggle Jaw Crushers: A Quick ComparisonIn basic industrial fields such as aggregate production and mineral mining, the structural differences between single toggle vs double toggle jaw crushers directly determine the equipment selection strategy. The comparative…
- What is the Life of a Jaw Crusher? Key Factors & Maintenance TipsThe service life of a jaw crusher is usually 5-15 years, and its life is subject to the combined effects of the intensity of equipment use, maintenance system and working…