Email: [email protected]
Gold Ore Processing: Jaw Crusher Efficiency
Effective gold ore processing hinges on precise crushing operations, where jaw crushers convert rugged deposits into optimized feedstock. Discover how to fine-tune these machines for peak productivity without compromising worksite safety or operational budgets.
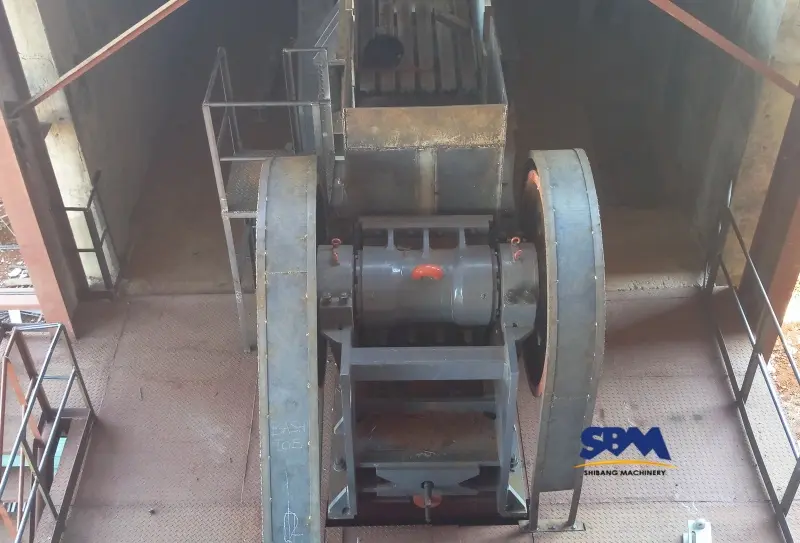
Why Jaw Crushers Dominate Gold Ore Processing?
In hard rock mining operations, jaw crushers serve as frontline warriors, pulverizing gold-laden quartz and other abrasive ores into fist-sized fragments. Their reinforced alloy frames withstand pressures exceeding 120 MPa, outperforming cone crushers in initial size reduction – a critical advantage when preparing 6-8″ material for heap leaching systems, as demonstrated at Idaho’s Silver Valley mine.
Key advantages include:
- High reduction ratios (6:1 on average)
- Minimal maintenance requirements
- Adaptability to varying ore hardness
Optimizing Jaw Crusher Setup for Gold Ore
1. Selecting the Right Crushing Equipment
Precision-engineered jaw crusher configurations directly correlate with ore geomechanics – take Canada’s Detour Lake Mine, where 30×42″ units with 180 HP motors process 800 TPH of auriferous shear zones (UCS 150 MPa), versus Western Australia’s Sunrise Dam operations utilizing 36×48″ heavy-duty crushers (300 HP) to tackle 220 MPa banded iron formations.
Pro Tip: Prioritize crushers with adjustable settings to accommodate fluctuating ore densities.
2. Feed Size Management
Avoid overloading by adhering to the “80% rule”: keep feed material no larger than 80% of the crusher’s gape width. For a 24-inch gape, limit rocks to 19 inches. Use a F5X vibrating feeder upstream to filter oversized material.
3. Crushing Chamber Maintenance
Regularly inspect jaw plates for wear. Rotate or replace them when thickness decreases by 20% to prevent efficiency losses. Australian mining company Blackridge Resources reported a 15% throughput increase after implementing biweekly plate inspections.
Case Study: Boosting Recovery Rates in Nevada’s Carlin Trend
A Nevada-based gold mine faced challenges with uneven particle sizes from their aging jaw crusher. By upgrading to a hydraulic adjustment system and installing wear-resistant manganese liners, they achieved:
- 22% higher throughput
- 18% reduction in energy consumption
- Consistent ¾-inch output for cyanide leaching
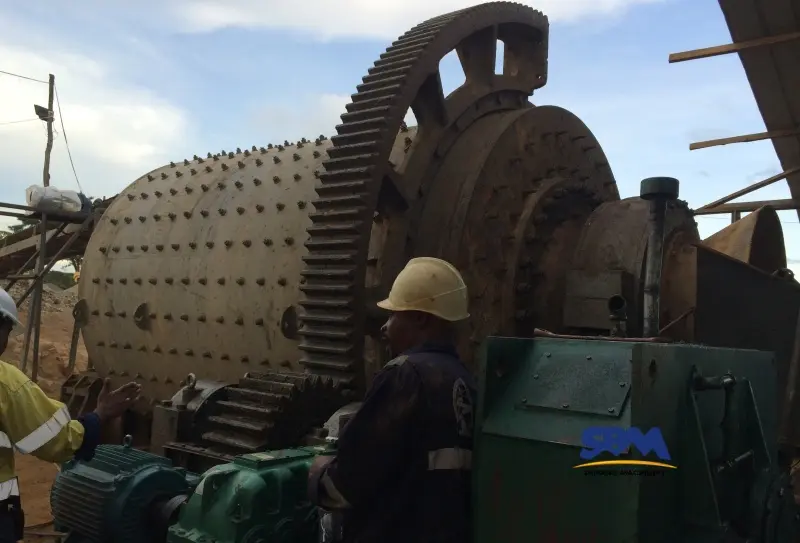
Avoiding Common Jaw Crusher Mistakes
- Ignoring Moisture Content: Wet, sticky gold ore can cause blockages. Canadian operator Yukon Gold Solutions mitigated this by pre-drying high-moisture ore batches.
- Overlooking Lubrication: Schedule greasing every 8–10 hours for bearings.
- Neglecting Safety Protocols: Always lock out power before clearing jams.
Troubleshooting Guide: Quick Fixes for Crusher Issues
Symptom | Likely Cause | Solution |
---|---|---|
Unusual vibrations | Worn bearings | Replace bearings ASAP |
Reduced output size | Loose toggle plate | Tighten or replace plate |
Frequent blockages | Incorrect feed angle | Adjust hopper to 30–45° |
FAQs: Jaw Crushers in Gold Ore Processing
Q: Can jaw crushers process oxidized gold ore?
A: Yes, but opt for corrosion-resistant materials like stainless steel components in humid environments.
Q: How often should I replace jaw plates?
A: Every 500–700 operational hours, depending on ore abrasiveness.
Mastering Gold Ore Crushing
Optimizing your gold ore jaw crusher involves equal parts technical knowledge and proactive maintenance. By aligning equipment specs with ore properties, adhering to feed guidelines, and learning from global case studies like Nevada’s success, you can streamline processing and maximize ROI.
Headquaters Office
Whatsapp:+8615225176731
Email: [email protected]
Address: No. 1688, Gaoke East Road, Pudong new district, Shanghai, China.
Website: https://www.mill-sbm.com/
Article Contents
Recent Posts
- Gold Ore Processing: Jaw Crusher EfficiencyEffective gold ore processing hinges on precise crushing operations, where jaw crushers convert rugged deposits into optimized feedstock. Discover how to fine-tune these machines for peak productivity without compromising worksite…
- Crushing River Gravel with Jaw CrushersA cornerstone of modern construction, river gravel delivers unmatched toughness and adaptability for roads, concrete, and erosion control. Yet its rugged, irregular nature demands machinery built to endure—enter jaw crushers.…
- How to Choose the Right Jaw Crusher Size for Your Industry?Selecting the right jaw crusher size isn’t a guessing game—it’s a science rooted in material dynamics and operational calculus. For industries from hard-rock mining to urban concrete recycling, even a…