Email: [email protected]
Jaw Crusher Capacity and Output Size Guide for Quarrying Operations
Jaw crushers are indispensable in quarrying operations for primary crushing, transforming large rocks into manageable aggregates. Understanding how to optimize their capacity and control output size is critical for maximizing productivity and meeting project specifications. Below, we break down the key factors influencing performance and provide actionable insights for operators.
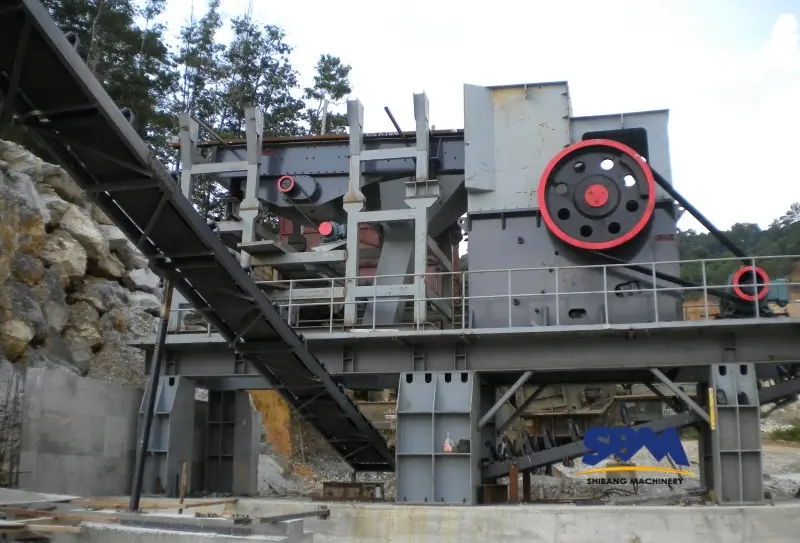
Key Factors Determining Jaw Crusher Capacity
1. Feed Opening Dimensions
The width and depth of the feed opening directly impact crushing capacity. For example, a 860×1,100 mm jaw crusher can typically process 200-500 tph of limestone, while granite, which is a rock with higher hardness, can reduce this ratio by 30%. So we can choose a hard rock crusher to process granite so that we can get a satisfactory production capacity.
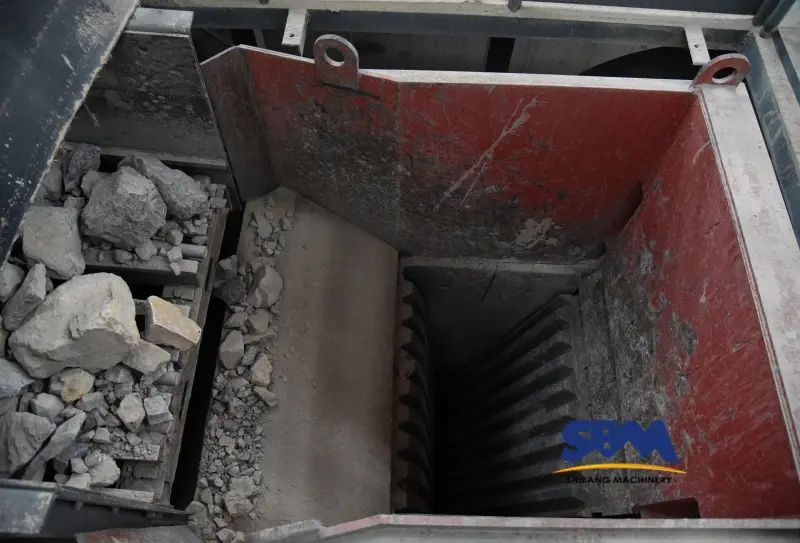
2. Material Characteristics
Rock hardness (measured by Mohs scale), abrasiveness, and moisture content significantly affect quarry crusher output:
- Soft sedimentary rocks (e.g., sandstone): 15-25% higher throughput
- Igneous rocks (e.g., basalt): Requires 20-40% more power
3. CSS (Closed Side Setting) Adjustments
The minimum distance between jaw plates determines your final output size:
CSS Setting | Typical Output Size | Capacity Impact |
---|---|---|
100 mm | 150-200 mm | Maximizes throughput |
50 mm | 75-100 mm | Reduces capacity by 25% |
25 mm | 35-50 mm | Capacity drops 40-50% |
Calculating Output Size in Quarry Applications
Use this formula to estimate jaw crusher product size:
P80 = 0.8 x CSS + (Feed Size x 0.2)
Example: For 150 mm feed material with 75 mm CSS
P80 = 0.8*75 + (150*0.2) = 60 + 30 = 90 mm
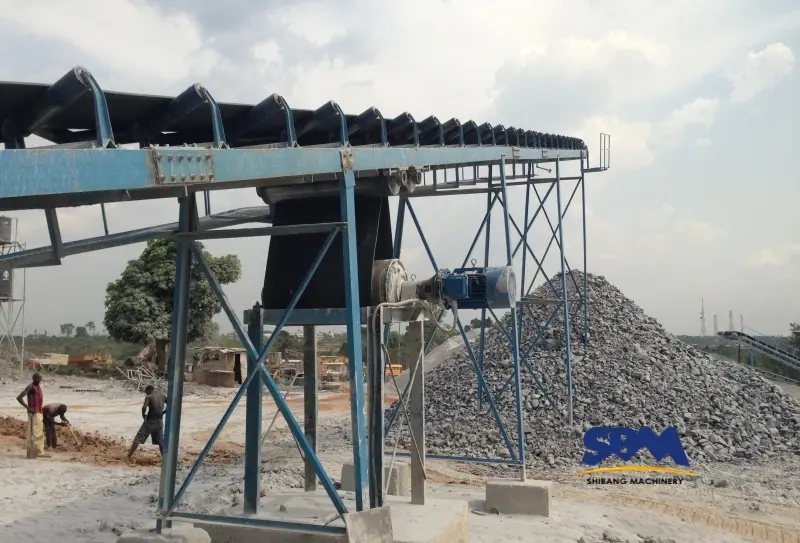
Optimizing Production: 3 Proven Strategies
1. Match Crusher Size to Quarry Requirements
Select jaw crushers with 20-30% higher rated capacity than your target production to account for material variability.
2. Implement Gradation Control
Use scalping screens before crushing to remove fines, increasing effective crushing chamber capacity by 15-20%.
3. Monitor Wear Patterns
Worn jaw plates increase the actual CSS by 10-25%, causing oversized output. Therefore, implement monthly measurements with crusher profile gauges.
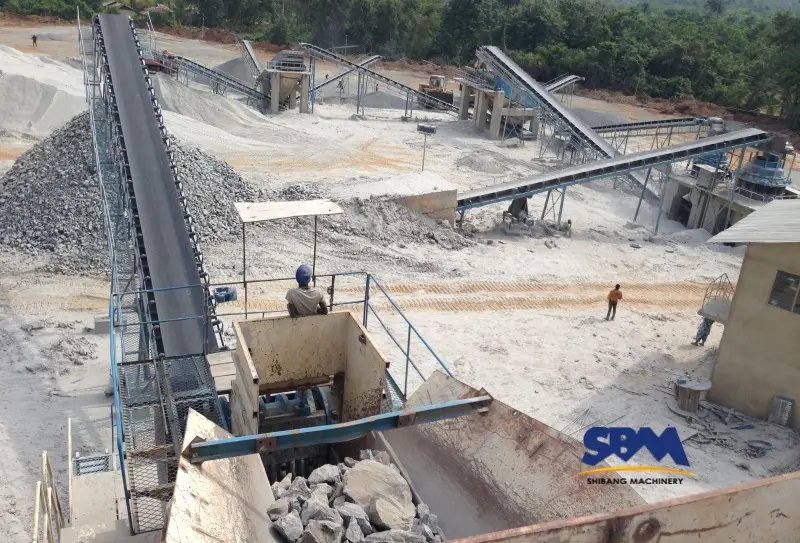
Case Study: Granite Quarry Output Optimization
A Texas quarry increased production by 18% after:
- First, adjusting CSS from 125 mm to 90 mm
- Installing pre-screening for >200 mm boulders
- Switching to corrugated jaw plates
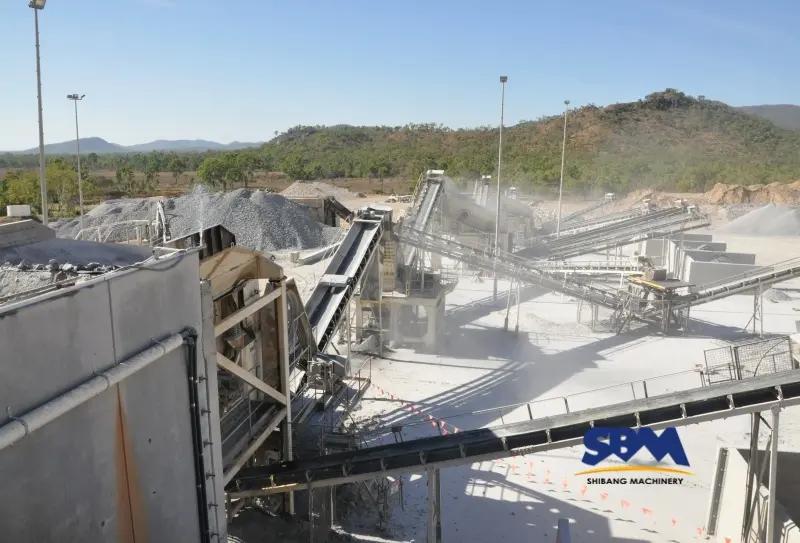
Common Mistakes in Capacity Planning
- Ignoring material bulk density variations (1.6 t/m³ vs 2.8 t/m³)
- Overlooking crusher discharge conveyor limits
- Failing to account for daily temperature-induced metal expansion
Advanced Tools for Precision Control
Modern solutions enhancing jaw crusher output management:
- Laser CSS measurement systems (±0.5 mm accuracy)
- Automomatic wear compensation software
- Real-time throughput monitoring dashboards
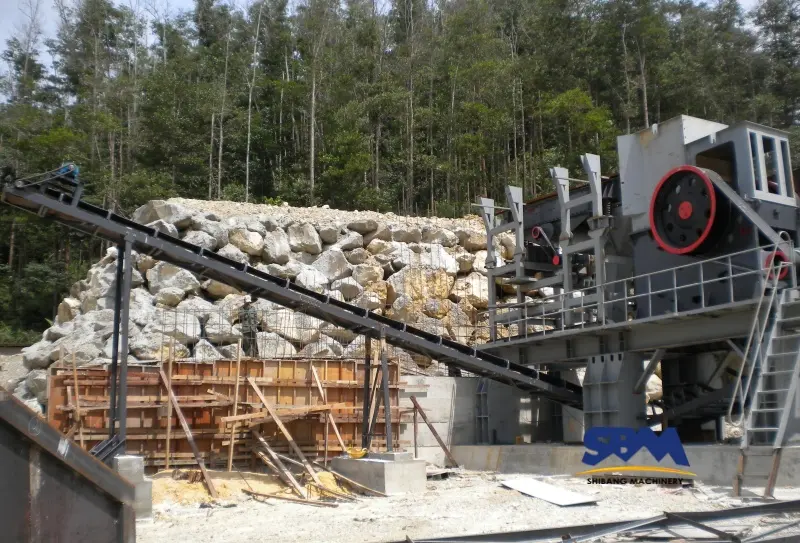
Maximize Your Quarry’s ROI
By mastering your jaw crusher’s capacity and output size relationships, quarries can achieve 15-30% higher yields. Therefore, keep in mind that the optimal settings will vary from day to day depending on material mix and wear rate. Also, combine these guidelines with regular equipment audits and operator training to achieve continued success in the competitive aggregates market.
Headquaters Office
Whatsapp:+8615225176731
Email: [email protected]
Address: No. 1688, Gaoke East Road, Pudong new district, Shanghai, China.
Website: https://www.mill-sbm.com/
Article Contents
Recent Posts
- What are the causes of damage to the jaw crusher plate?Because it is under tremendous pressure during material processing, there are many causes for the damage of the jaw crusher plate. Understanding why they degrade prematurely can save costs and…
- What is the ideal jaw crusher for granite crushing?Granite’s relentless toughness demands jaw crusher built to endure—think armored jaws and unyielding frames. Prioritize crushers that combine brute force with precision engineering, like heat-treated alloys and adaptive crushing chambers.…
- Jaw Crusher for Limestone Processing: A Guide to EfficiencyAs limestone is widely used in construction and industry, its processing requires strong and durable jaw crusher to meet the needs of the industry. Among the many crushers, the jaw…