Email: [email protected]
Jaw Crusher Feeding Tips: 5 Strategies to Eliminate Blockages
Blocked crushing chambers are a universal headache in aggregate processing. From quarries in Sweden to recycling plants in Texas, improper feeding tips and methods can cripple jaw crusher efficiency. Let’s explore field-tested techniques keeping operations blockage-free.
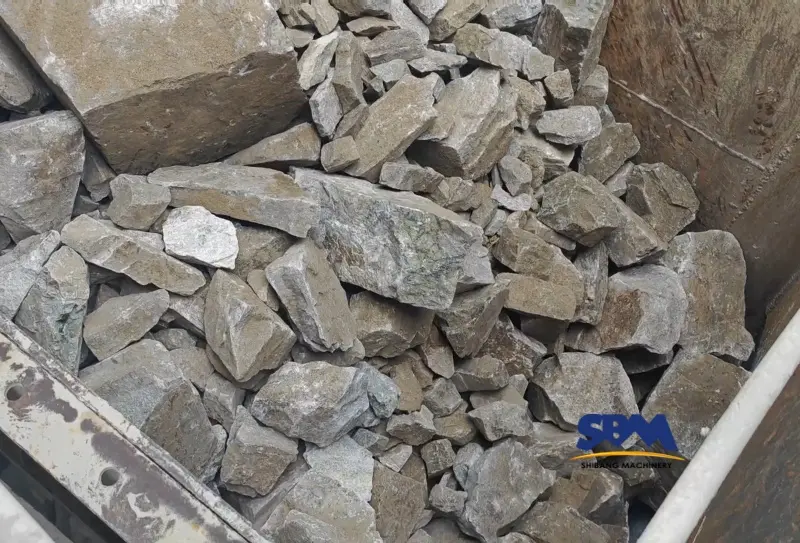
1. Optimizing Feed Material Dimensions
A Canadian mining operation reduced jaw crusher jams by 68% after implementing strict size control. Their secret? Matching feed dimensions to the crusher’s gape width:
- Rule: Maximum feed size ≤ 80-90% of crusher opening
- Tool: Pre-screening with vibrating feeders
- Benefit: Eliminates “bridging” where oversize materials lock the chamber
2. Material Entry Angle Optimization
Australian operators found a 15-20° feed angle reduces impact shock:
Vertical Dump → 43% blockage rate Angled Feed → 9% blockage rate
Pro Tip: Pair with mobile jaw crushers for dynamic angle adjustments.
3. Controlling Material Moisture Content
Brazil’s iron ore processors combat sticky materials using:
- Pre-drying: Reducing moisture below 5%
- Baffle Walls: Redirecting material flow (ideal for vibrating feeder systems)
- Anti-stick Liners: Teflon-coated surfaces in feed chutes
4. Crusher Capacity Matching Strategies
German engineers developed this formula for optimal throughput:
Ideal Feed Rate (TPH) = (Crusher Width (in) × RPM) ÷ 250
Case Study: A Norwegian plant using AI-powered feeders achieved 92% utilization rate.
5. Maintenance as Prevention: Wear Pattern Analysis
Key indicators from U.S. aggregate producers:
- Uneven jaw plate wear → misaligned material flow
- Worn toggle seats → inconsistent stroke patterns
- Dampered vibration → inefficient material discharge
Solution: Implement IoT-enabled new jaw crusher models with real-time wear monitoring.
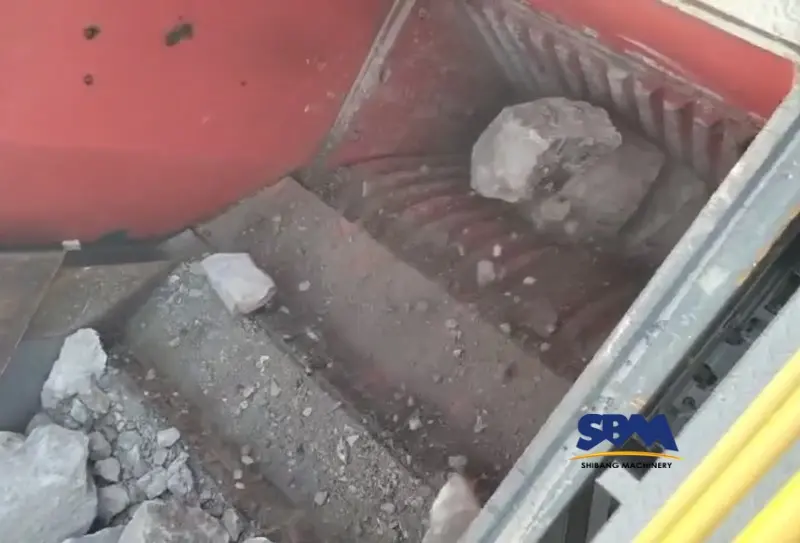
Global Success Blueprint: Lessons from 3 Continents
Sweden’s Granite Solution:
- Installed heated feed chutes
- Reduced winter blockages by 81%
Chile’s Copper Miracle:
- Implemented staggered feeding cycles
- Increased crusher uptime to 94%
South Africa’s Diamond Approach:
- Combined grizzly screens with mobile jaw crushers
- Achieved 12-month blockage-free operation
Final Thought: Blockage prevention isn’t about brute force – it’s about intelligent material orchestration. From selecting proper vibrating feeder systems to adopting smart noise control of jaw crusher technologies, every adjustment contributes to seamless operations.
Need expert guidance? Contact us for information and solutions on our anti-clogging crushers designed for your specific material challenges.
Headquaters Office
Whatsapp:+8615225176731
Email: [email protected]
Address: No. 1688, Gaoke East Road, Pudong new district, Shanghai, China.
Website: https://www.mill-sbm.com/
Article Contents
Recent Posts
- Top 6 Advantages of Mobile Jaw Crushers (And Why They Outperform Fixed Units)Mobile jaw crushers are reshaping the global resource development landscape with multiple advantages such as “plug and play” integrated design and autonomous mobility. From Indonesian volcanic rock quarries to the…
- Single Toggle VS Double Toggle Jaw Crushers: A Quick ComparisonIn basic industrial fields such as aggregate production and mineral mining, the structural differences between single toggle vs double toggle jaw crushers directly determine the equipment selection strategy. The comparative…
- What is the Life of a Jaw Crusher? Key Factors & Maintenance TipsThe service life of a jaw crusher is usually 5-15 years, and its life is subject to the combined effects of the intensity of equipment use, maintenance system and working…