Email: [email protected]
Jaw Plate Selection Guide: Optimize Performance for Your Crushing Operation
Choosing the right jaw plates can increase your crushing efficiency by 25-40% while reducing replacement costs. This comprehensive jaw plate selection guide explains how material composition, tooth profile design, and operating conditions determine plate longevity. Whether you’re operating a C6X Jaw Crusher or older models, these insights will help you make informed decisions.
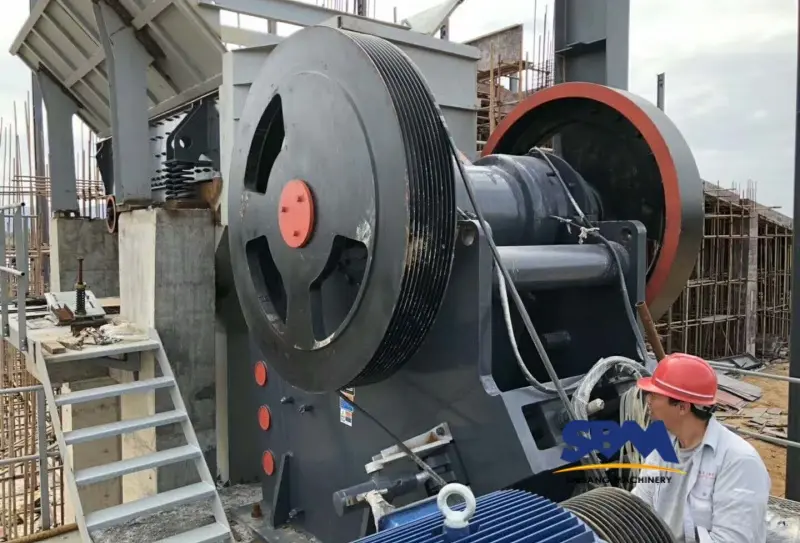
Key Factors in Jaw Plate Selection
Material Composition Choices
Modern jaw plates use three primary materials:
- Manganese Steel (14-18%): Ideal for general-purpose quarry applications, withstands 50-70k tons before replacement
- Chrome Iron Alloy: 30% longer lifespan in abrasive materials like granite
- Ceramic-Enhanced: Reduces wear by 45% in high-silica content operations
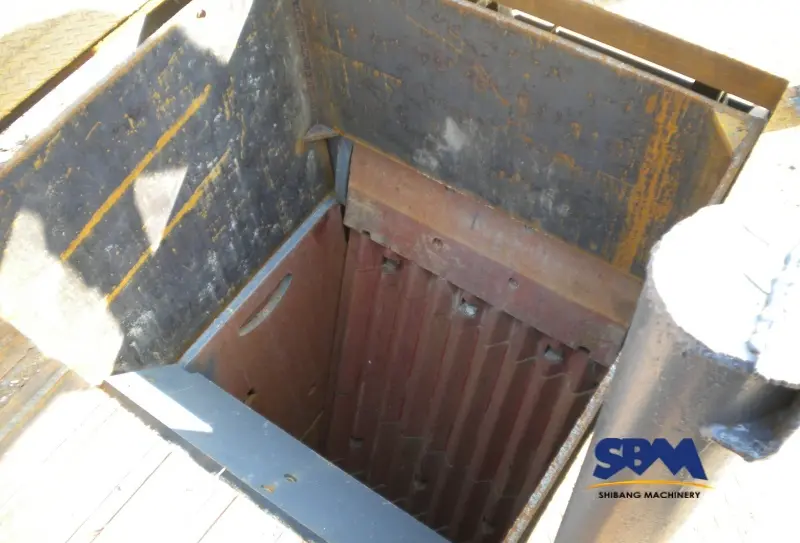
Tooth Profile Design Considerations
The plate’s tooth configuration directly impacts your crusher’s working mechanism:
Profile Type | Best For | Output Size Range |
---|---|---|
Straight | Primary crushing | 150-300 mm |
Waved | Secondary reduction | 50-120 mm |
Hybrid | Mixed material feeds | 30-150 mm |
4-Step Selection Process
- Analyze Feed Material: Test hardness (Mohs scale) and abrasiveness
- Determine Crusher Type: C6X series jaw crusher requires specific plate locking systems
- Calculate Economic Lifespan: Balance initial cost vs tons crushed/$
- Verify Compatibility: Check mounting system dimensions (±2mm tolerance)
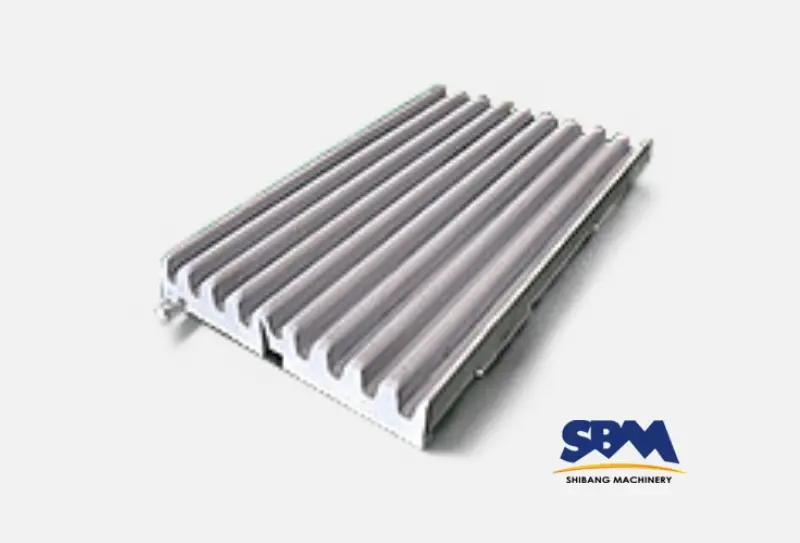
Maintenance Synergy: Plates and Crusher Health
Proper jaw crusher maintenance extends plate lifespan by 60%:
- Rotate plates every 200-300 operating hours
- Maintain correct CSS settings (affects wear patterns)
- Use laser alignment tools for precise installation
Case Study: Granite Quarry Optimization
A Brazilian operation achieved 32% cost reduction by:
- Switching from standard Mn14 to Mn18Cr2 plates
- Implementing bi-weekly wear measurements
- Syncing replacements with scheduled maintenance downtime
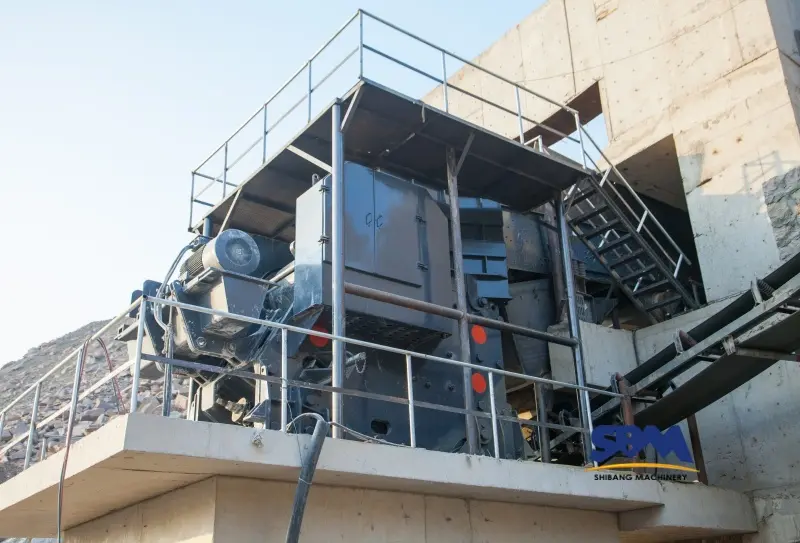
Advanced Monitoring Techniques
- 3D wear scanning for precise remaining thickness analysis
- AI-powered wear rate prediction models
- Ultrasonic hardness testing for material verification
Common Selection Mistakes
- Choosing cheap plates needing 3x more frequent replacement
- Ignoring material compatibility (e.g., zinc contamination)
- Overlooking plate weight impacts on crusher kinematics
Strategic Selection Pays Dividends
Mastering jaw plate selection requires understanding your material, machine type (like C6X models), and operational goals. Pair this guide with regular preventive maintenance to achieve 18-24 month plate lifespans even in demanding conditions. Remember: The optimal plate today may differ tomorrow – re-evaluate selections with major material changes.
Headquaters Office
Whatsapp:+8615225176731
Email: [email protected]
Address: No. 1688, Gaoke East Road, Pudong new district, Shanghai, China.
Website: https://www.mill-sbm.com/
Article Contents
Recent Posts
- Jaw Crusher for Limestone Processing: A Guide to EfficiencyAs limestone is widely used in construction and industry, its processing requires strong and durable jaw crusher to meet the needs of the industry. Among the many crushers, the jaw…
- Impact crusher with 300 TPH for large projectsWhen mining giants face mountains of iron ore or urban demolitions generate concrete avalanches, 300 TPH impact crusher emerges as material-processing titans. Beyond basic specs, we dissect how these industrial…
- Affordable Impact Crusher: A Game-Changer for Small Construction BusinessesSmall construction companies often face budget constraints, yet need reliable equipment – an affordable impact crusher. This crusher can bridge the gap, providing efficient material processing without a huge capital…