Email: [email protected]
New Method of Crushing and Grinding Granite
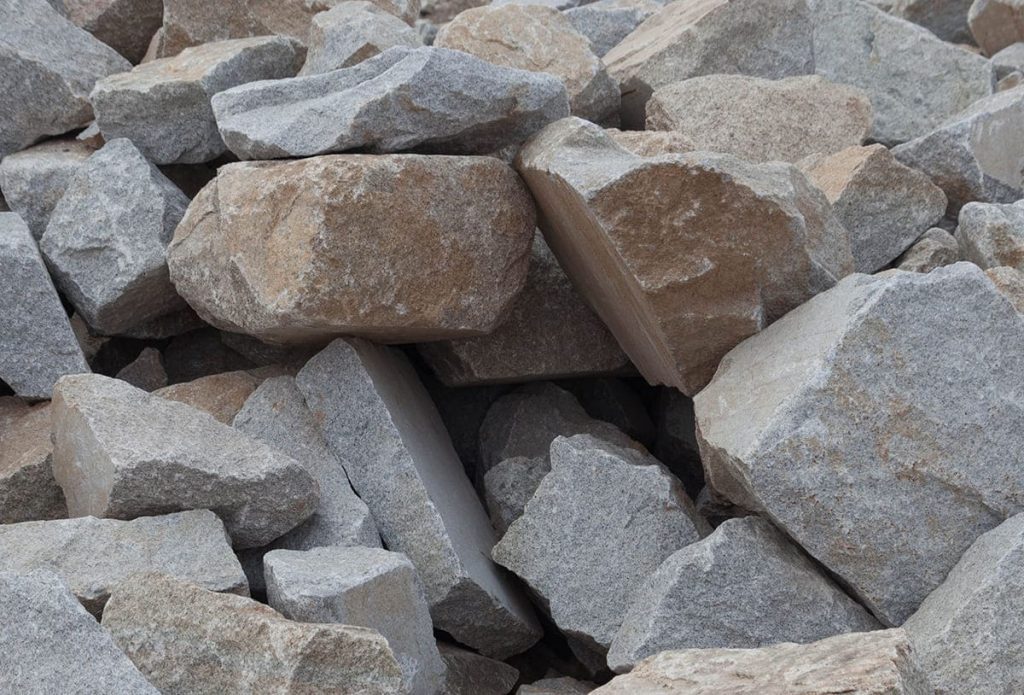
Introduction
New method of crushing and grinding granite has emerged, with the potential to fundamentally alter the industry. The innovative approach for crushing and grinding granite involves reducing the hard stone to small fragments using specific equipment and procedures. This method is more effective and efficient than traditional procedures, resulting in faster and more accurate results. Using cutting-edge technology and innovative concepts, this breakthrough procedure is altering how granite is processed and used in a variety of applications.
The granite quarry production line is the primary crusher and screening equipment for reducing massive granite stones to small fragments.
The granite crusher is the primary crushing device in the granite crushing and screening plant. As a prominent, recognized granite crusher manufacturer in China, SBM provides clients with jaw crushers, impact crushers, cone crushers, VSI crushers, and other granite crushers. SBM also offers completely automated granite production systems, which comprise crushing, sorting, and grinding. A granite stone production factory is frequently used to create crushed granite, granite, sand, and granite powder.
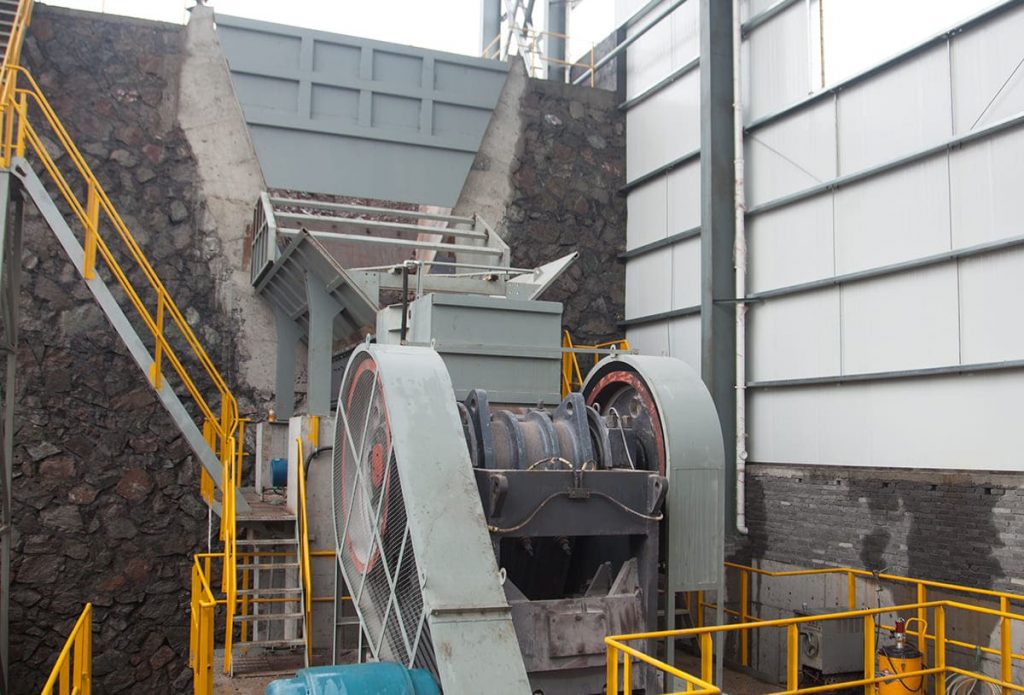
Granite Crushing Equipment
A granite quarry is the principal source of crushed granite in the worldwide construction materials business. There are various granite quarry crushing plants across Asia, Europe, and Africa.
The quarry granite production line is the primary crusher and screening facility used to reduce large granite stones to small bits. Conveyors, sorting equipment, primary, secondary, and feed equipment comprise the entirety of the granite quarry production line. Our granite quarry crusher system is of excellent quality, requires less maintenance, is ecologically friendly, is simple to use, and has an extremely high crushing performance.
In the mining of granite, the SBM-developed granite crusher machine is crucial. Granite cone crushers are used for secondary crushing after first crushing using granite jaw crushers. SBM will also provide vibrating feeders to feed granite crushers, vibrating screens to divide goods into different sizes, and a belt conveyor to move granite from one location to another.
The granite impact crusher can crush and shape granite, resulting in end products used primarily in the construction of motorways, water reservoirs, airports, and other infrastructure. Because of the high hardness of the stone, the cost of an impact crusher is likewise high, with prices for stones generated by an impact crusher being more expensive than those produced by a jaw crusher, cone crusher, or wear parts.
Cone crushers of the S and HP series are ideal for turning crushed stone into fine particles on a wide scale.
Maximizing Efficiency and Output: Implementing the Latest Techniques in Granite Crushing and Grinding
Granite is a popular construction, architectural, and interior design material. It is a lovely stone that is sturdy and long-lasting, capable of withstanding harsh use. Crushing and grinding granite, on the other hand, may be a tough procedure when working with large volumes of the material. Traditional granite crushing and grinding procedures can be labor-intensive and inefficient, increasing costs and decreasing production. Fortunately, new strategies for increasing production and efficiency while decreasing costs have been identified.
High-pressure Grinding Rollers for Granite
High-pressure grinding rollers (HPGRs) are a relatively new breakthrough in granite crushing and grinding. HPGRs, a type of grinding machinery, employ a pair of counter-rotating rolls to crush the material. The rollers are made of a wear-resistant material, such as tungsten carbide, and are designed to impart a lot of pressure on the substance. The material breaking apart under this pressure produces a more uniform and consistent output.
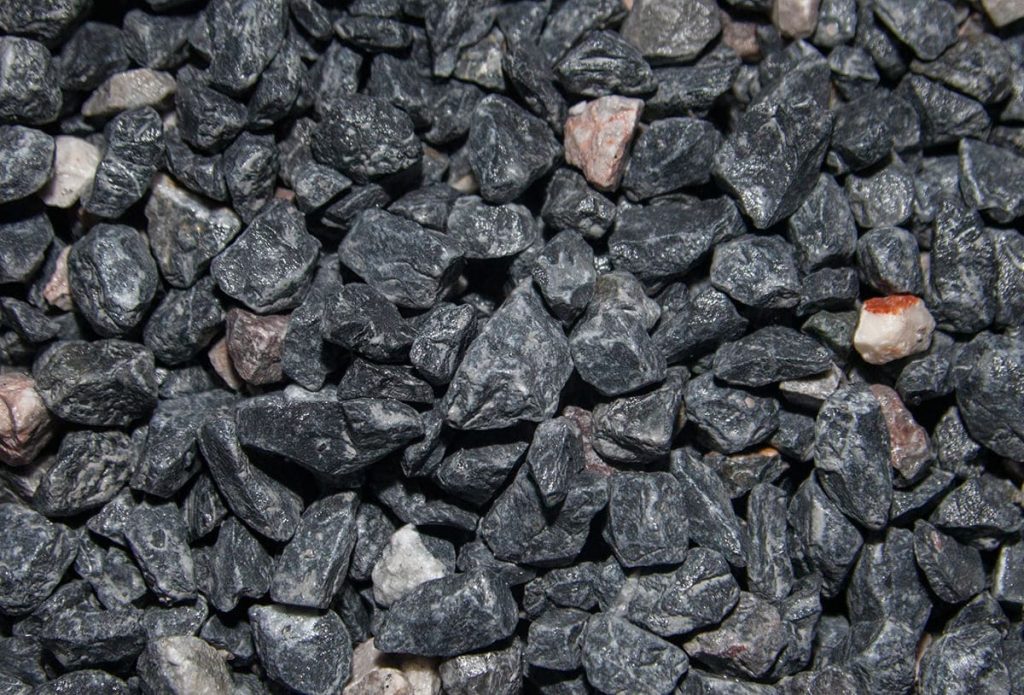
In some aspects, HPGRs outperform traditional crushing and grinding procedures. The primary advantage is that they consume less energy to operate than traditional crushers and mills. This might save you a lot of money in the long run. Second, HPGRs create less fines and a more homogenous particle size distribution, resulting in more uniform output. This can save waste while improving the completed product’s quality. Finally, when compared to traditional crushing and grinding procedures, HPGRs are more environmentally friendly since they produce less dust and noise.
VSI Crusher for Crushing Granite
Vertical shaft impact (VSI) crushers are yet another novel approach to crushing and grinding granite. In VSI crushers, a type of impact crusher, a high-speed rotor is used to throw the material against a hard surface, such as a rock or a metal plate. The impact breaks up the material, resulting in a more equal and constant production.
In a variety of ways, VSI crushers outperform traditional crushing and grinding procedures. The primary advantage is that they consume less energy to operate than traditional crushers and mills. This might save you a lot of money in the long run. Second, VSI crushers produce a more consistent output with less fines and a more regular distribution of particle sizes. This can save waste while improving the completed product’s quality. Finally, because they produce less dust and noise, VSI crushers are more environmentally friendly than traditional crushing and grinding procedures.
Other Advanced Technologies for Granite
In addition to HPGRs and VSI crushers, there are other advanced technologies for crushing and grinding granite that can improve efficiency and productivity. Utilizing cutting-edge control systems, for example, can aid in increasing productivity and optimizing the performance of crushing and grinding machines. Similarly, advanced sensors and monitoring systems can help in the early discovery of potential problems, allowing for proactive maintenance and repair.
Overall, new ways of crushing and grinding granite can boost production while decreasing costs. Whether using HPGRs, VSI crushers, or other cutting-edge technology, it’s vital to use the right tools for the job and adhere to industry best practices for maintenance and operation. Businesses may use this to ensure that they are getting the most out of their equipment and getting the best return on investment.
Revolutionizing Granite Processing: A Comprehensive Guide to the New Method of Crushing and Grinding
Granite is a popular building and home décor material due to its strength and beauty. However, processing granite may be tough, particularly when it comes to crushing and grinding. Granite is frequently crushed and pulverized by huge machinery, which may be expensive and time-consuming. Fortunately, a new method of crushing and grinding granite has emerged, with the potential to fundamentally alter the industry.
The contemporary method for crushing and grinding granite is to use a high-pressure roller mill. A pair of parallel rollers provide a lot of pressure to the granite block being crushed in this mill. The pressure crushes the granite into smaller pieces, which are then processed into a fine powder. This method of crushing and grinding granite is far more efficient than traditional methods since it requires less energy and produces more consistent results.
Faster
One of the primary benefits of the new granite crushing and grinding technology is that it is significantly faster than old ways. The high-pressure roller mill can process a big volume of granite quickly, allowing producers to make more goods in less time. This can result in higher profitability and a more efficient manufacturing process.
More Uniform Output
The new procedure for crushing and grinding granite also produces a more uniform output. When granite is crushed and milled using traditional methods, the particle sizes might vary, lowering the quality of the end product. The high-pressure roller mill produces particles with more consistent sizes, resulting in a higher-quality end product.
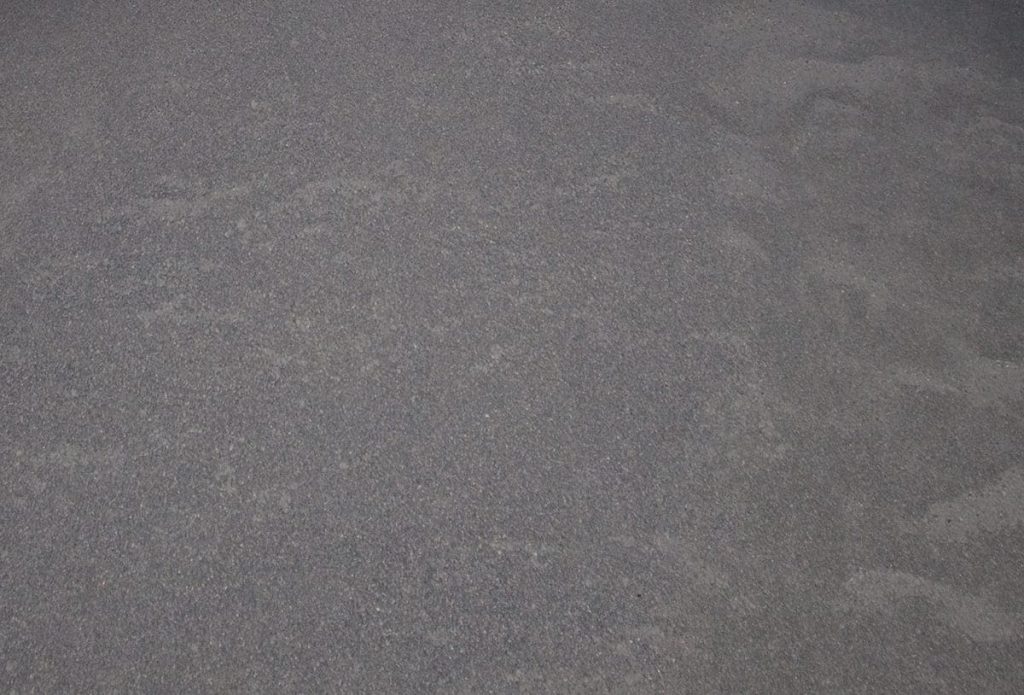
More Environmentally Friendly
The new method of crushing and grinding granite is also more environmentally friendly. Traditional granite processing procedures can consume a substantial amount of energy, resulting in significant carbon emissions. Because the high-pressure roller mill requires less energy to operate, it produces less greenhouse emissions. This can help businesses reduce their carbon footprint and promote a more sustainable future.
Challenge One: High-pressure Roller Mill’s Expense
Despite the numerous advantages of the new granite crushing and grinding technology, several concerns must be addressed. One of the primary impediments is the high-pressure roller mill’s expense. The expense of acquiring and maintaining this equipment may be too expensive for smaller manufacturers. As the technology becomes more widely utilized, the price is likely to fall.
Challenge Two: Specialized Personnel Training
Another challenge is that running a high-pressure roller mill necessitates specialized training. A certain level of ability is necessary for this technology to perform securely and successfully. Manufacturers will need to invest in training programs to ensure that their employees are properly trained to operate the machinery.
Finally, the revolutionary stone crushing and grinding process has the potential to radically alter the industry. It is faster, more efficient, and produces more uniform outcomes as compared to traditional techniques. It is also beneficial for the environment since it requires less energy and creates fewer carbon emissions. The benefits of the new strategy are evident, notwithstanding a few difficulties that must be addressed. As the technology becomes more widely utilized, it is expected to supplant traditional granite processing procedures.
Conclusion
Finally, the new approach for crushing and grinding granite involves shattering the stone into small fragments with high-pressure water jets. This strategy is more successful and environmentally friendly than more traditional procedures that use explosives and heavy equipment. It is a safer option for employees and local residents since it produces less dust and noise pollution. Overall, this unique strategy has the potential to transform the granite industry.
If you’d like to learn more about the granite crushing and screening line or granite crusher cost, please contact us online.
Headquaters Office
Whatsapp:+8615225176731
Email: [email protected]
Address: No. 1688, Gaoke East Road, Pudong new district, Shanghai, China.
Website: https://www.mill-sbm.com/
Article Contents
Recent Posts
- Jaw Crusher for Limestone Processing: A Guide to EfficiencyAs limestone is widely used in construction and industry, its processing requires strong and durable jaw crusher to meet the needs of the industry. Among the many crushers, the jaw…
- Impact crusher with 300 TPH for large projectsWhen mining giants face mountains of iron ore or urban demolitions generate concrete avalanches, 300 TPH impact crusher emerges as material-processing titans. Beyond basic specs, we dissect how these industrial…
- Affordable Impact Crusher: A Game-Changer for Small Construction BusinessesSmall construction companies often face budget constraints, yet need reliable equipment – an affordable impact crusher. This crusher can bridge the gap, providing efficient material processing without a huge capital…