Email: [email protected]
Rock Crusher
A rock crusher is a device that breaks up solid objects like boulders into smaller bits. It is frequently used to make gravel or for building projects. Rocks are sized down and made more manageable for a variety of uses using mechanical force, such as compression or impact. In the mining, quarrying, recycling, and building sectors, rock crushers are often employed.
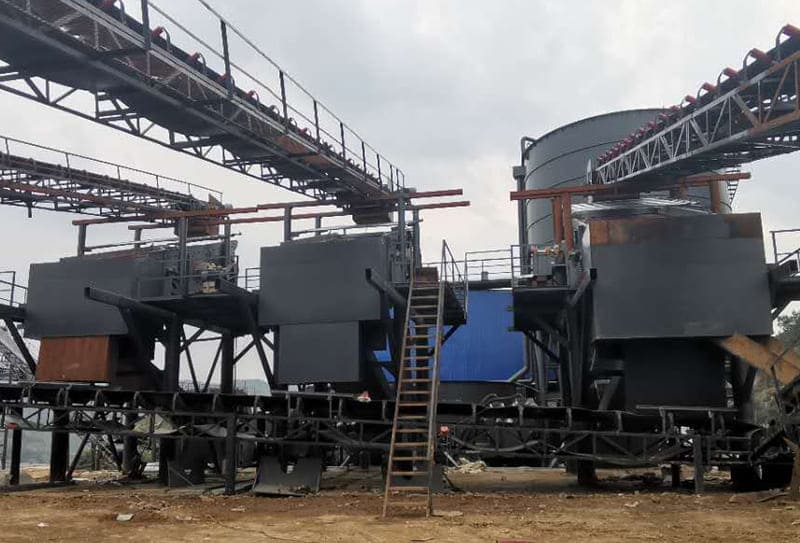
The manufacturing of aggregate, mining operations, construction projects, and demolition are just a few of the sectors and applications where rock crushers are crucial. They make it possible to reduce bigger boulders to manageable sizes, preparing them for transit, storage, or additional processing.
The hardness and abrasiveness of the material, the necessary product size, the intended capacity, and operational issues should all be taken into account when choosing a rock crusher. Different rock crushers are ideal for particular purposes and have varying capacities.
What are the different types of rock crushers?
There are several different types of rock crushers commonly used in mining, quarrying, and recycling applications. Each type has its own unique characteristics and uses. Here are some of the most common types of rock crushers:
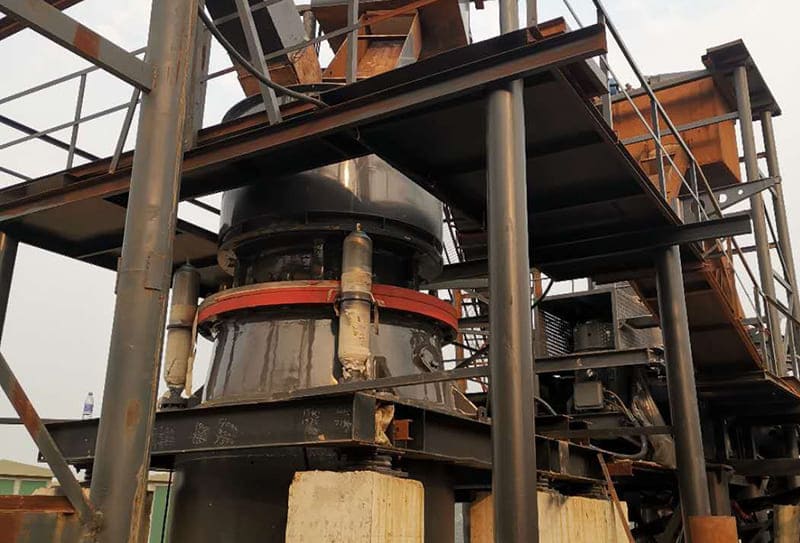
- Jaw Crusher: Using a stationary jaw and a moving jaw to form a V-shaped cavity, a jaw crusher is a primary crusher that breaks rock. In the mining and aggregate sectors, it is the most used kind of crusher.
- Cone Crusher: A cone crusher uses the compression principle to break up rocks by pressing them against a concave surface and mantle. For secondary, tertiary, or quaternary crushing phases, it is frequently employed.
- Impact Crusher: An impact crusher breaks rocks using the impact principle. A swift rotor is used, which collides with the rock and shattering it into smaller bits. Impact crushers may be used for both primary and secondary crushing because of their adaptability.
- Gyratory Crusher: A gyratory crusher is like a jaw crusher, except instead of a fixed jaw, it features a round cone. The cone’s gyrating motion inside the concave crushing chamber produces the crushing action. For large-scale operations, gyratory crushers are frequently utilized as primary crushers.
- Vertical Shaft Impactor (VSI): Rocks are thrown against a solid surface using a vertical shaft impactor (VSI) crusher, which employs a high-speed rotor with wear-resistant tips to smash the rocks. It is frequently used to make manufactured sand and to shape crushed rock particle shapes.
- Hammer Crusher: A hammer crusher, often called a hammer mill, is a machine that crushes materials by impacting them with revolving hammers. Soft to medium-hard materials seem to be its main use.
- Roller Crusher: A roller crusher consists of one or more cylindrical rollers that rotate in opposite directions. The rocks are crushed between the rollers as they move.
- Cone Crusher with Inclined Screen: This type of crusher combines a cone crusher with an inclined screen deck. It is commonly used in closed-circuit crushing applications, where the oversized material from the screen is returned to the crusher for further crushing.
- Mobile Crusher: A mobile crusher is a type of rock crusher that is mounted on a wheeled or tracked platform. It provides flexibility and convenience in crushing operations, as it can be easily transported between job sites.
- Stationary Crusher: A rock crusher that is installed at a particular site is known as a stationary crusher. In larger-scale mining or quarrying operations where the crusher must be in a permanent and secure location, it is frequently employed.
What materials can be crushed by a rock crusher?
Rock crushers are adaptable equipment that can break down a variety of substances. The types of materials that may be treated may depend on the particular rock crusher and its capacity.
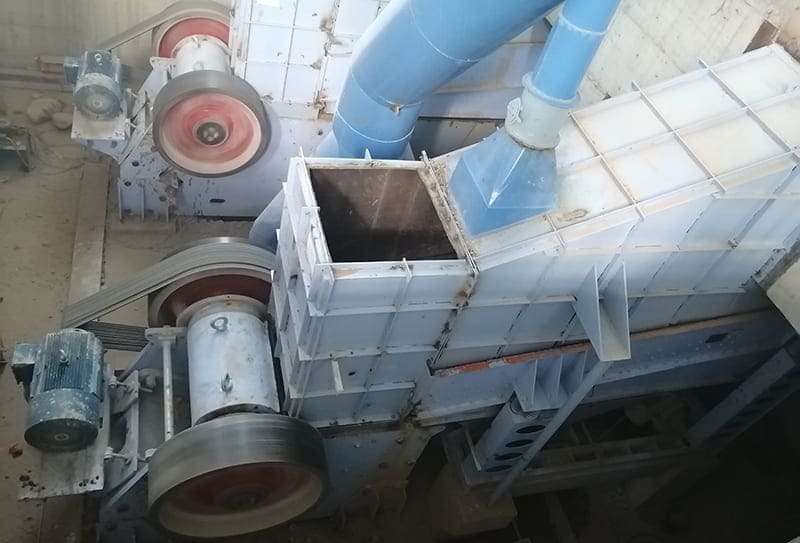
- Hard Rock: Granite, basalt, quartzite, and hard limestone are among the hard and abrasive materials that may be crushed using rock crushers. High crushing pressures and long-lasting wear components are frequently needed for these rocks.
- Soft Rock: Soft limestone, shale, gypsum, and phosphate are among the softer materials that rock crushers can handle. These substances are often softer and simpler to smash.
- Aggregates: The manufacture of aggregates for use in construction involves a lot of utilization of rock crushers. To produce various sizes of aggregate materials, they may crush a variety of rock types, including gravel, sand, and crushed stone.
- Ores: In mining operations, rock crushers are frequently used to crush ores, such as iron ore, copper ore, gold ore, and silver ore. Compared to conventional rocks, these materials are often bigger and harder to break.
- Construction and Demolition Waste: Construction and demolition debris, such as concrete, asphalt, bricks, and rubble, can be processed using rock crushers. These materials may be recycled and reused in building projects by being crushed.
- Recycled Materials: Rock crushers are also capable of crushing recycled materials like asphalt and concrete. In order to decrease the demand for fresh resources, these materials are frequently employed in applications such as building roads.
- Industrial Minerals: Industrial minerals including limestone, dolomite, gypsum, phosphate, and talc may be crushed using rock crushers. The manufacturing, agricultural, and chemical processing industries all require these minerals.
- Slag: Slag is a byproduct of the metal smelting process that may be crushed using rock crushers. Slag may be reduced in bulk while recovering important metals and minerals.
What are the key components of a rock crusher?
A rock crusher consists of several key components that work together to achieve the desired crushing outcome. While the specific design and configuration may vary depending on the type of rock crusher, here are some of the common key components:

- Feed Hopper: The feed hopper, which is a large chamber or container, houses the rock or other material that has to be crushed. The material enters the crusher in a regulated flow thanks to this device.
- Feeding Mechanism: The feeding mechanism, such as a vibrating feeder or a conveyor belt, transfers the material from the feed hopper to the crushing chamber.
- Crushing Chamber: The place where the actual crushing happens called the crushing chamber. To prevent the crusher from experiencing excessive wear and to make the crushing process easier, it is often coated with wear-resistant material.
- Crusher Jaws or Plates: The crushing chamber of jaw crusher has both a fixed and a moveable jaw. The fixed jaw serves as a stationary surface against which the rock is crushed and is normally positioned vertically. By swinging back and forth, the moveable jaw applies pressure to the rock, crushing it against the fixed jaw.
- Rotor or Hammers: Rotors with revolving hammers or blow bars are used in impact crushers to hit the material. The material is struck with kinetic energy from the rotating rotor, which causes it to shatter.
- Crushing Liners: Cone crushers and gyratory crushers’ crushing chambers are lined with replaceable wear-resistant crushing liners, sometimes referred to as concaves or mantles. They offer effective crushing action and aid in the crusher’s protection.
- Drive System: A rock crusher’s drive system consists of the motor, pulleys, and belts or gears that transfer power from the engine to the moving components of the crusher. It supplies the energy required for the crusher to run.
- Control panel: The control panel serves as the rock crusher’s interface for operation and management. It could have knobs, buttons, and screens for displays to track and modify the crusher’s settings.
- Conveyor or Discharge Chute: After the material has been crushed, it has to be removed from the crusher. The crushed material is moved away from the crusher and to the appropriate destination using a discharge chute or conveyor.
- Support Structure: The rock crusher’s support structure serves as its framework and foundation. To withstand the forces produced during the crushing process, it is often built of steel or reinforced concrete.
What safety precautions should be taken when operating a rock crusher?
Prioritizing safety is essential while using a rock crusher to avoid mishaps and guarantee the safety of the users and anybody nearby.
![icon name="arrow-right" prefix="fas"] What safety precautions should be taken when operating a rock crusher?](https://www.mill-sbm.com/wp-content/uploads/2023/06/32-rock-crusher-5.jpg)
- Read and Comply with the Manufacturer’s Guidelines: Learn the directions and specifications for the particular rock crusher you are using from the manufacturer. Observe the installation, use, maintenance, and safety recommendations.
- Wear Personal Protective Equipment (PPE): Always put on the proper PPE, such as steel-toed boots, safety goggles, hard helmets, and earplugs. Depending on the particular risks connected to the rock crusher and the workplace, additional PPE can be needed.
- Guarding: Ensure that the rock crusher’s working parts are all suitably protected. To avoid unintentional contact, place safety barriers or coverings over belts, pulleys, flywheels, and other potentially dangerous regions.
- Lockout/Tagout Procedures: Before beginning any maintenance or repair work, use lockout/tagout procedures to properly disconnect the rock crusher from its power supply. This avoids unintentional starting or energy release.
- Clearing Blockages: Make sure the power is turned off and the crusher is securely locked out before attempting to clear any blockages. Use the proper equipment and safe procedures to clear obstacles without endangering yourself.
- Training and Supervision: Make sure that the operators of the rock crusher are properly trained and able to operate it. Give operators who are less experienced the appropriate supervision. Make sure operators are informed of safety protocols and best practices and regularly update training.
- Housekeeping: Keep the area surrounding the rock crusher tidy and orderly. To lessen the chance of mishaps or injuries, clear the area of debris, loose objects, and trip hazards.
- Fire Prevention: Take steps to avoid fires, such as routinely inspecting and maintaining electrical components, storing combustible products properly, and adhering to fire safety regulations.
- Communication: Establish open lines of communication between operators and other staff members working nearby the rock crusher. To make sure that everyone is aware of possible threats and can cooperate efficiently, use the proper signals, hand signs, or radios.
- Regular Maintenance and Inspections: Check the rock crusher often for any mechanical or safety concerns. Follow the manufacturer’s recommendations for routine maintenance to keep the machinery in excellent operating order.
Always keep in mind that safety should come first while using a rock crusher. You can lower the risk of accidents and make the workplace safer for everyone by implementing these safety measures and encouraging a safety-conscious culture.
Headquaters Office
Whatsapp:+8615225176731
Email: [email protected]
Address: No. 1688, Gaoke East Road, Pudong new district, Shanghai, China.
Website: https://www.mill-sbm.com/
Headquaters Office
Whatsapp:+8615225176731
Email: [email protected]
Address: No. 1688, Gaoke East Road, Pudong new district, Shanghai, China.
Website: https://www.mill-sbm.com/
Article Contents
Recent Posts
- Why Jaw Crushers Are the Unshakable Foundation of Mining?In the rugged world of mining, where efficiency determines profitability, jaw crushers stand as the first line of defense against raw, unprocessed ore. From Australia’s iron-rich Pilbara region to Argentina’s…
- What Industries Primarily Use Jaw Crushers? A Global PerspectiveThe applications of jaw crushers are very wide and numerous industries mainly use them. While jaw crushers might seem like simple mechanical workhorses, their impact on modern industry is anything…
- Understanding the Key Components of Impact Crushers for Optimal Crushing EfficiencyThis guide explores the key components of impact crushers, their functions, and real-world applications in global industries. Key Components of Impact Crushers 1. Rotor Assembly: The Heart of Crushing Efficiency…