پست الکترونیک: [email protected]
درک نقش مهم سنگ شکن های فک در تولید کل
In the mining and construction industries, jaw crushers are indispensable workhorse machines and are the backbone of aggregate production. When a highway expansion project required 2.3 million tons of high-quality aggregate, engineers turned to their C6X series jaw crushers – not just as machines, but as strategic partners in sustainable construction. This story is repeated around the world, revealing why jaw crushers remain the first step in transforming raw stone into the building blocks of civilization.
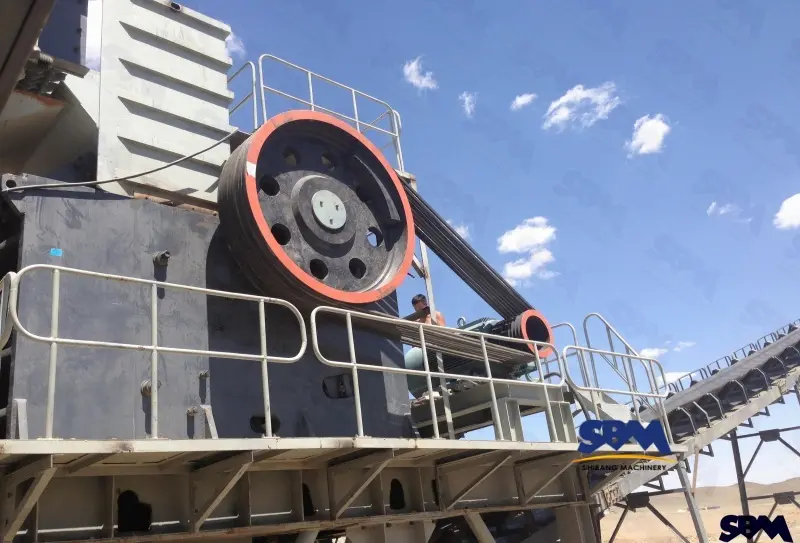
Comprehensive equipment configuration for aggregate processing
Modern aggregate handling systems are a highly coordinated industrial chain that typically includes the following core modules:
- Vibrating feeder: Controls the feed rate of raw materials by adjusting amplitude and frequency to avoid overloading the jaw crusher.
- Primary jaw crusher (such as C6X): With a hydraulically adjusted discharge design, the crushing size can be optimized in real time during operation (in the case of Heidelberg Materials, Germany, the C6X processes 800mm granite raw materials to 150-200mm with a capacity of 600 tons/hour).
- Secondary impact crusher (such as PF1210): fine crushing is achieved through high-speed impact and adjustable angle of plate hammer (the case of Yukon mine in Canada shows that PF1210 processes 200mm raw materials to less than 50mm, reducing energy consumption by 22%).
- Multi-layer vibrating screen: can separate 4-6 different particle sizes of aggregates at the same time.
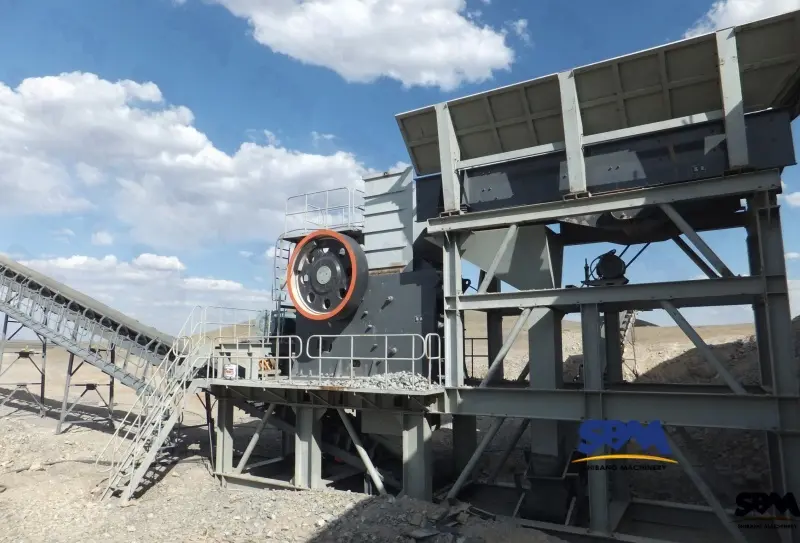
Key role in aggregate production
a) Primary crushing of raw materials
In aggregate production lines, jaw crushers are usually the first process. They crush large stones (maximum size 1.5 meters) and prepare materials for subsequent crushing stages. مثلا, limestone crushing lines in Brazil rely on jaw crushers to process raw materials into 0-5 میلی متر, 5-10 mm and 20-40 mm aggregates.
b) Handling a variety of material types
Jaw crushers excel in processing hard materials such as river pebbles, سنگ گرانیت, marble and construction/demolition waste. This powerful performance makes them a cornerstone equipment for sustainable construction practices. They effectively convert concrete سنگ خرد شده and masonry fragments into standardized reusable aggregates through a controlled crushing cycle. Their adaptability extends to circular economy initiatives, especially in repurposing mixed construction waste as secondary raw materials for road base construction and concrete manufacturing. مثلا, an optimized jaw crusher configuration has achieved more than 95% material recovery in a concrete recycling project, producing aggregate that meets ASTM C33 specifications for structural applications.
c) Increase operational efficiency
By controlling the feed size and discharge settings, the jaw crusher can meet the particle size requirements of the finished product. This performance is crucial for the feed of subsequent equipment. Standardized particle size of the finished aggregate can be guaranteed.
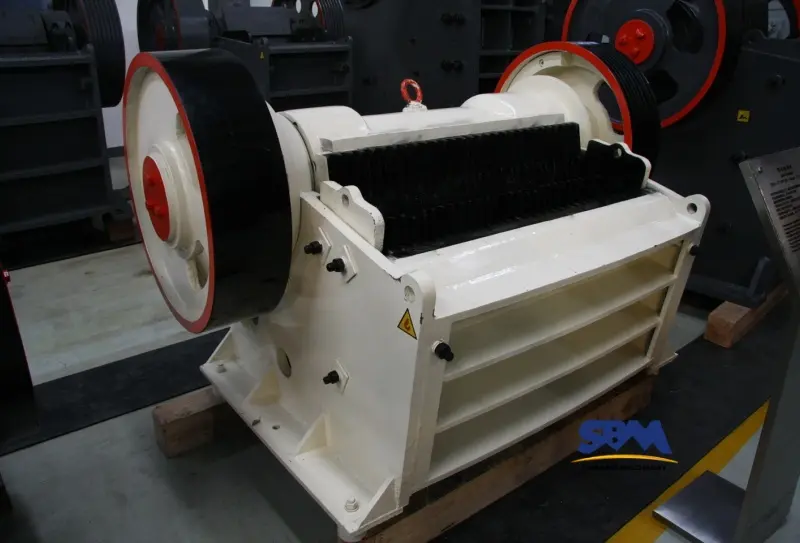
Increasing mining efficiency: synergy between jaw crusher and impact crusher
In the operation practice of an aggregate processing plant in Canada, the combination of C6X series jaw crusher (with high output and low energy consumption characteristics) and PF1210 impact crusher (with heavy rotor and deep cavity crushing design) has achieved a significant effect of increasing aggregate production by 30%. In this solution, the jaw crusher completes the primary crushing of ore through its optimized crushing chamber structure, and then the material enters the PF1210 impact crusher for secondary crushing. The precision alloy material of its plate hammer and the V-shaped impact plate layout not only ensure the uniform particle size of the output (80% of the finished product particle size is controlled in the range of 0-15mm), but also realizes the flexible switching of different graded aggregates through the hydraulic adjustment system. The unit energy consumption of the entire system is reduced by 18% compared with the traditional solution.
In the field of highway construction, a project in Colorado, USA, uses a similar technical combination: the PE series jaw crusher crushes the limestone raw materials into coarse aggregates below 150mm, and then further processes them through the impact-rebound crushing mechanism of the PF1210 impact crusher. The equipment optimizes the rotor speed (650-800دور در دقیقه) and the impact plate angle to secondary crush the material into 0-5mm graded machine-made sand, with cubic particles accounting for 92%, perfectly meeting the requirements of asphalt mixture for fine aggregate. This collaborative process increases the comprehensive utilization rate of stone to 98%, and at the same time controls the on-site dust concentration below 5mg/m³ through the closed structure design.
مطالعه موردی: Rebuilding Ukraine’s Infrastructure
When reconstructing the Kharkiv-Dnipro highway:
- Challenge: Process 1.5M tons of concrete rubble and granite
- راه حل: Mobile C6X jaw crusher units with magnetic separators
- Results:
- 84% recycled material usage
- 600 tons/hour production rate
- 24/7 operation with remote diagnostics
“This isn’t just crushing – it’s urban mining,” says Oleksandr Volkov, site manager. “The jaw crushers allow us to turn war debris into hope.”
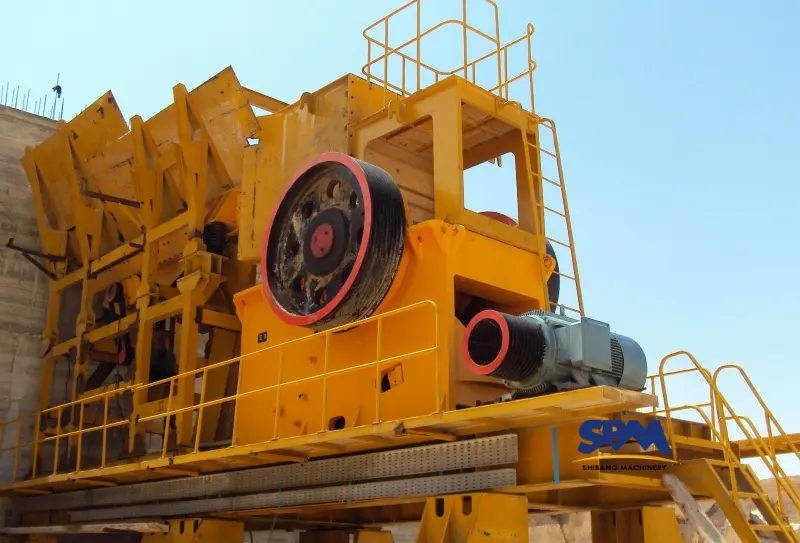
Maintenance Masterclass: Extending Crusher Life
Problem: A Chilean copper mine faced monthly liner replacements
راه حل: Implemented SBM’s 3D Wear Mapping System
- Step 1: Laser scan jaw plates hourly
- Step 2: AI predicts optimal flip/rotate timing
- Step 3: Automated hydraulic adjustments
Outcome:
- Liner lifespan increased from 18 به 61 days
- Annual savings: $640,000 USD
Best Practices for Maintaining Jaw Crushers in Aggregate Production
- Regular Lubrication: Prevent wear on plate hammers and toggle plates.
- Monitor Feed Size: Oversized materials can strain the crusher; use pre-screening if necessary.
- Inspect Wear Parts: Replace jaw plates and liners promptly to maintain crushing efficiency.
مثلا, a mine in Australia implemented regular maintenance and an automated monitoring system for its SBM crushers. در نتیجه, the service life of the jaw crushers was extended by 40%.
دفتر مرکزی
واتساپ:+8615225176731
پست الکترونیک: [email protected]
نشانی: خیر. 1688, جاده شرقی گائوک, ناحیه جدید پودونگ, شانگهای, چین.
سایت اینترنتی: https://www.mill-sbm.com/
محتویات مقاله
پستهای اخیر
- شستشوی فک دو ضلعی در مقابل دو ضامن: یک مقایسه سریعدر زمینه های اساسی صنعتی مانند تولید کل و استخراج مواد معدنی, تفاوت های ساختاری بین شکن های تک در مقابل شکن فک دو ضامن به طور مستقیم استراتژی انتخاب تجهیزات را تعیین می کند. تطبیقی ...
- زندگی یک سنگ شکن فک چیست؟? عوامل اصلی & نکات مربوط به نگهداریعمر خدمات یک شکن فک معمولاً است 5-15 سال, و عمر آن در معرض اثرات ترکیبی از شدت استفاده از تجهیزات است, سیستم نگهداری و کار ...
- فراتر از خرد شدن: تأثیرات و راه حل های زیست محیطی برای سنگ شکن های فکاز معادن سنگ آهن استرالیا گرفته تا معادن گرانیتی نروژی, تأثیرات زیست محیطی سنگ شکن های فک – سر و صدا, گرد و خاک, نیازهای انرژی و زباله – بحث جهانی را برانگیخته است. به عنوان معدن ...