پست الکترونیک: [email protected]
محدودیت های یک سنگ شکن فک چیست؟? – یک راهنمای جامع
غلبه بر محدودیت های یک سنگ شکن فک برای به حداکثر رساندن کارآیی و جلوگیری از خطاهای عملیاتی ضروری است. The following will walk you through the key limitations of a jaw crusher and how to solve them.
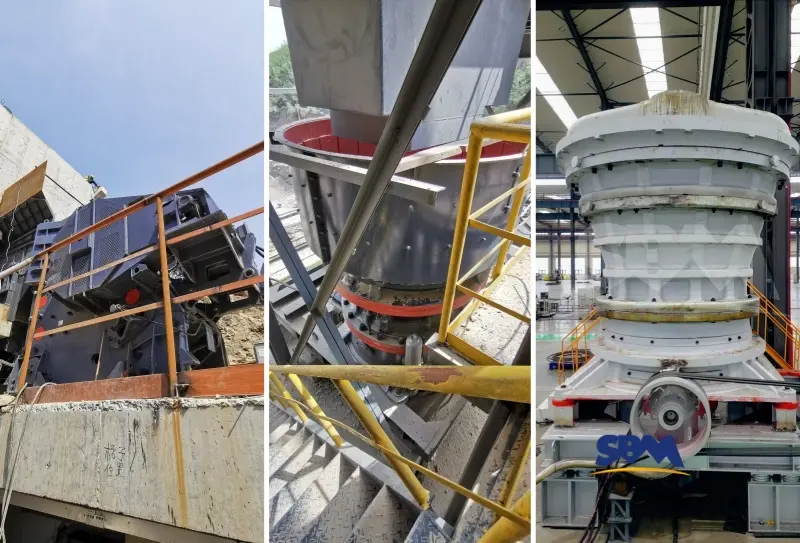
1. Material hardness and abrasiveness limitations
While adept at processing hard rocks such as quartzite, basalt and granite, jaw crushers are also subject to great challenges, such as extremely abrasive materials or materials with a compressive strength exceeding 320 MPA.
مطالعه موردی: Quartzite Processing in Sweden
At LKAB’s Kiruna iron ore, standard jaw crushers were initially unable to process quartzite containing 40% abrasive feldspar. Wear plates were wearing 3 times faster than standard iron ore, resulting in replacement costs of up to 92,000 euros per month.
راه حل:
- Use high manganese steel jaw plates for better wear resistance.
- Pair with secondary crushing equipment such as cone crushers for more delicate processing of hard materials.
2. Feed size and capacity limitations
If the size of the material fed into the jaw crusher exceeds the maximum range allowed by the equipment design during operation, it is easy to cause the crushing chamber to be blocked, and in serious cases, the production line will be forced to stop. Taking the PE 900×1200 model as an example, its maximum allowable feed size is 750 میلی متر; while the C6X200 series has a stronger processing capacity and can accept block materials up to 1200 میلی متر.
راه حل:
- Install a vibrating screen to filter oversized material before feeding it into the crusher.
- Choose a larger model, such as the C6X200 series, for higher capacity (تا 1,510 t/h).
نکات: you can learn more about نکات مربوط به تغذیه شکن فک.
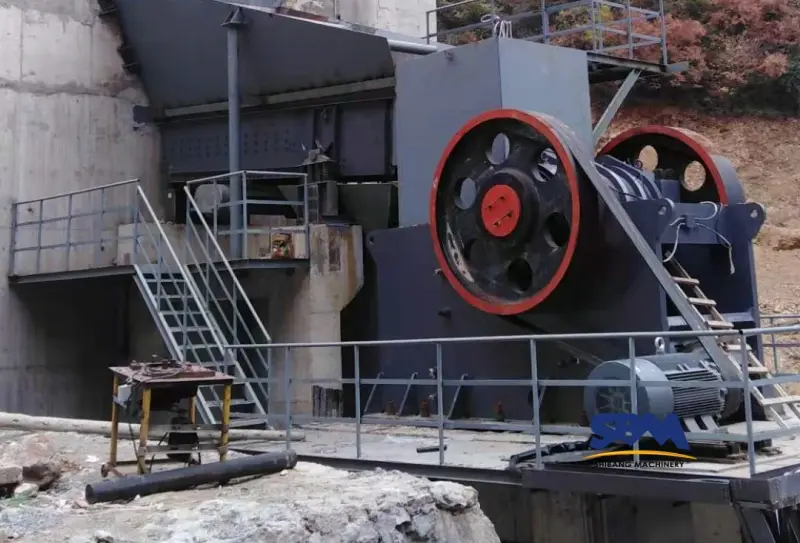
3. High maintenance and wear costs
Frequent wear of components such as toggle plates, jaw liners and bearings is a very common problem. A case study of a Brazilian limestone quarry showed that the jaw crusher required replacement of jaw crusher spare parts every 6-8 weeks due to abrasive limestone.
A case study in the Turkish construction industry showed that 40% of jaw crusher downtime was due to liner wear, and maintenance costs accounted for 15% of the operating budget. Regular lubrication and calibration checks are critical but time-consuming.
In addition, an Australian gold mine cost analysis showed that Newmont’s Boddington operation tracked a worn toggle plate, resulting in:
- 11% excess energy consumption
- 0.3 mm oversize product deviation
- Downstream screening losses of $7,200 per month
راه حل:
- Implement a predictive maintenance program.
- Use an automatic lubrication system to extend bearing life
4. Energy consumption and operating costs
Traditional jaw crusher, especially early models, generally has the limitations of high energy consumption. Taking the PE 1200×1500 model as an example, its rated power is as high as 200 kilowatts, and it shows significant energy consumption characteristics during the material crushing process. Actual application cases show that in the production line transformation of a German aggregate processing plant, by replacing the traditional jaw crusher with an energy-saving impact equipment, the energy consumption in the secondary crushing link was successfully reduced by 15%, verifying the key role of equipment selection in energy efficiency optimization.
Compared with gyratory crushers, سنگ شکن های فکی consume more energy in material handling. مثلا, the crushing energy consumption of each ton of limestone in a jaw crusher is about 25%-30% higher than that of a gyratory device. This energy efficiency gap is particularly prominent in a limestone mining project in India. When the crushing equipments run continuously for more than 12 ساعت, its electricity consumption accounts for up to 32%-35% of the total production cost. It has become an important factor restricting operational efficiency. It is worth noting that the high energy consumption characteristics of the jaw crusher in this case are mainly due to its mechanical structure characteristics – including large friction losses and relatively low crushing chamber volume utilization.
راه حل:
- Retrofit variable frequency drives (VFDS) to optimize motor efficiency.
- Compare energy usage to alternatives such as gyratory crushers for large operations.
5. Inefficient handling of wet or sticky materials
Jaw crushers do not perform well with wet or clay-rich materials, as seen in Malaysian quarries, where moisture causes frequent clogging of jaw crusher feed points. In South African coal mines, clay-rich coal seams often reduce efficiency by 20-30%, requiring the use of secondary crushers such as cone crushers to compensate.
راه حل:
- Pre-dry materials or use additives to reduce moisture content. مثلا, install infrared pre-dryers at feed points.
- Consider using gyratory or impact crushers to handle sticky materials.
- Implement staggered crushing cycles during the monsoon season.
6. Limited control over product shape
Jaw crushers produce aggregates with uneven shapes compared to cone crushers that provide better cubicity. In a US highway project, jaw crushed aggregates required additional screening, which increased costs by 20%.
A comparative study of I-35 expansion material from a Texas highway project showed:
- Metric jaw crusher only Jaw crusher + cone crusher combination
- Cubic particles 58% 89%
- Rescreening required 3 times/day 1 time/3 days
- Total cost/cubic meter $4.20 $3.65
راه حل:
- Use a jaw crusher for primary crushing and pair it with a cone crusher for secondary shaping.
- Operational Challenges in Global Case Studies
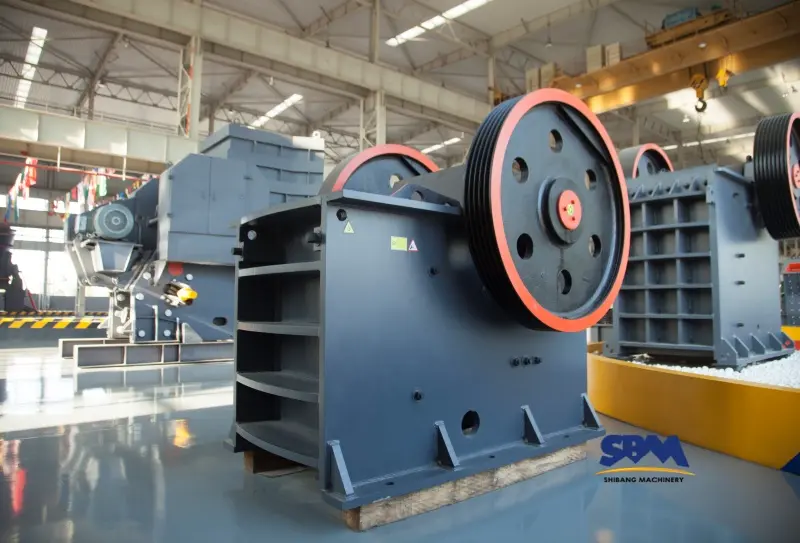
Special Cases
مورد 1: South African Iron Ore
A medium-sized mine faced frequent blockages due to the abrasive nature of high-iron laterite ore. Switching to a فک PP PE with a reinforced liner improved durability but increased maintenance frequency. The solution was a hybrid system that paired a jaw crusher with a cone crusher for primary crushing, followed by secondary processing.
مورد 2: Australian quarry
In New South Wales, a quarry struggled with fluctuating feed sizes from open-pit mining. Installing a vibrating feeder with adjustable settings optimized material flow and reduced jaw crusher overload incidents by 25%.
مورد 3: European recycling facility
A German plant encountered metal contamination when processing construction waste. Integrating an eddy current separator upstream of the jaw crusher reduced equipment damage by 60%, highlighting the importance of pre-treatment.
Comparing Jaw Crushers to Alternatives
عوامل | سنگ شکن فک | Gyratory Crushers |
---|---|---|
Feed Size | Limited (تا 1200 میلی متر) | Large (تا 1525 میلی متر) |
ظرفیت | عالی (تا 1,510 t/hr) | عالی (تا 1,525 t/hr) |
Maintenance | Frequent liner replacement | Reduced wear due to larger crushing area |
Energy Consumption | Higher | Lower |
For operations where scalability is a priority, a gyratory crusher may be preferable, but a jaw crusher is still cost-effective for smaller or mobile setups.
Optimizing Jaw Crushers Performance
Prescreening: Use vibrating screens to remove oversized material before crushing.
Liner Selection: Choose cone liners in high-wear environments.
Regular Maintenance: Schedule alignment checks and lubrication to minimize downtime.
Hybrid Systems: Pair with a cone crusher for secondary processing to increase efficiency.
In summary, سنگ شکن فکی, as the core equipment of primary crushing, is irreplaceable in the field of mineral processing. Although jaw crusher has limitations such as limited material adaptability, high operation and maintenance costs, and energy consumption pressure, it can effectively break through the application boundaries through systematic technical optimization. If you need customized spare parts selection guidance or feeding system optimization solutions, we can provide overall solutions covering equipment selection, process layout and energy efficiency optimization based on material characteristics (such as hardness ≤320MPa, maximum block size ≤1200mm) and production capacity requirements (30-1000t/h).
دفتر مرکزی
واتساپ:+8615225176731
پست الکترونیک: [email protected]
نشانی: خیر. 1688, جاده شرقی گائوک, ناحیه جدید پودونگ, شانگهای, چین.
سایت اینترنتی: https://www.mill-sbm.com/
محتویات مقاله
پستهای اخیر
- سنگ معدن طلا: کارآیی خرد کننده فکپردازش سنگ معدن طلای موثر به عملیات خرد کردن دقیق وابسته است, جایی که سنگ شکن های فک رسوبات ناهموار را به مواد اولیه بهینه تبدیل می کنند. کشف کنید که چگونه این دستگاه ها را برای بهره وری اوج بدون به خطر انداختن محل کار تنظیم کنید ...
- شن و ماسه رودخانه با سنگ شکن های فکسنگ بنای ساخت و سازهای مدرن, River Gravel سختی و سازگاری بی نظیر را برای جاده ها ارائه می دهد, بتونی, و کنترل فرسایش. با این حال ناهموار, طبیعت نامنظم نیاز به ماشین آلات ساخته شده برای تحمل شکن های فک وارد می کند.…
- چگونه می توان اندازه خرد خرد فک را برای صنعت خود انتخاب کرد?انتخاب اندازه خرد کننده فک درست یک بازی حدس نیست - این یک علم ریشه در پویایی مواد و حساب عملیاتی است. برای صنایع از معدن سخت سنگ گرفته تا بازیافت بتن شهری, حتی…