E-mail: [email protected]
Stratégies de réduction du bruit pour les concasseurs à mâchoire fixes: Amélioration de l'efficacité et de la sécurité
Les concasseurs à mâchoires fixes sont essentiels dans les industries minières et agrégées, (Raisons de réduction du bruit) Mais leur bruit opérationnel peut dépasser les niveaux sûrs, Impact sur la santé des travailleurs et la conformité réglementaire. This article explores actionable strategies to reduce noise in fixed jaw crushers, supported by global case studies and technical insights.
Understanding Noise Sources in Fixed Jaw Crushers
Jaw crushers generate noise through multiple mechanisms:
- Mechanical Impact: Crushing hard materials like granite or basalt creates high-frequency vibrations and impact noise.
- Friction and Wear: Moving parts, such as toggle plates and eccentric shafts, produce grinding sounds as components degrade.
- Resonance: Structural vibrations from unbalanced flywheels or poorly aligned components amplify noise.
Par exemple, a Canadian mining company reported noise levels exceeding 110 dB(UN) during limestone processing, primarily due to worn toggle plates and insufficient damping systems.
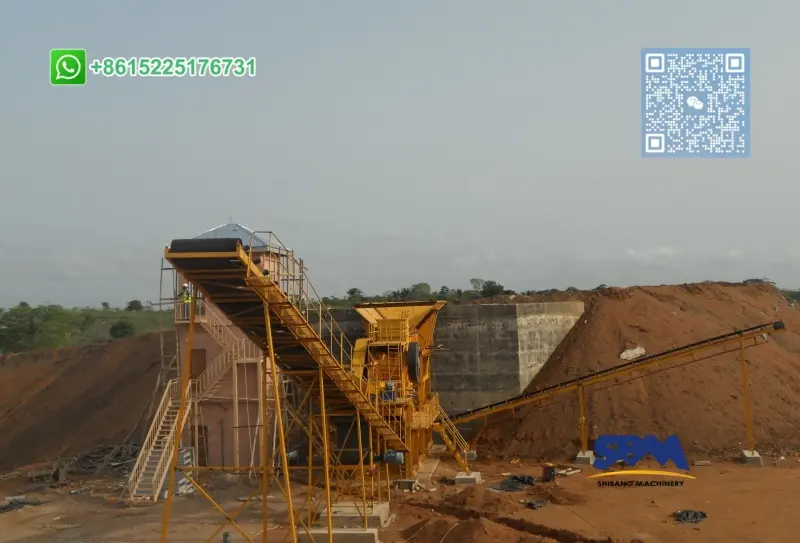
Proven Noise Reduction Techniques
1. Acoustic Enclosures and Damping Materials
Installingsoundproof enclosures around crushers can reduce noise by up to 20 dB(UN). In Sweden, a quarry operator combined steel-framed enclosures with mineral wool insulation to achieve a 15% reduction in ambient noise.
- Embedded Acoustic Black Holes (ABHs): Research from Australia highlights ABHs—flexible plates with tapered thickness—as effective vibration dampers, cutting high-frequency noise by 30% in lab tests.
2. Design and Component Optimization
- Replace Flat Plates with Corrugated Jaws: Corrugated jaw surfaces (common in Blake crushers) minimize material slippage, reducing repetitive impact noise.
- Anti-Vibration Mounts: A German engineering firm reduced resonance noise by 25% using rubber-isolated mounts for eccentric shafts.
3. Maintenance-Driven Noise Control
- Lubrification régulière: Proper greasing of toggle plates and bearings reduces friction-related noise.
- Wear Part Replacement: Timely replacement of worn jaw plates (Par exemple, switching from manganese steel to composite alloys) prevents uneven crushing and noise spikes.
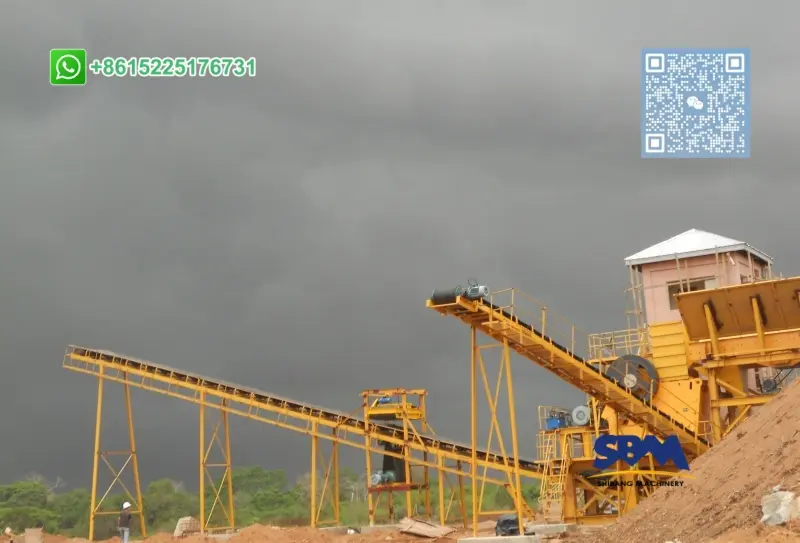
Étude de cas: Noise Mitigation in a U.S. Granite Processing Plant
A Texas-based facility reduced crusher noise from 105 dB(UN) pour 88 dB(UN) by:
- Installingpolyurethane-lined chutes to dampen material impact.
- Upgrading to aC6X series jaw crusher with optimized flywheel balance.
- Implementingpredictive maintenance using vibration analysis tools to detect misalignments early.
Linking Noise Reduction to Broader Operational Goals
- Efficacité énergétique: Modern crushers like thePE series prioritize low-noise designs while cutting energy use by 15–30%.
- Comparaison des coûts: Alors quenew C6X crushers may have higher upfront costs, their noise-reducing features lower long-term compliance penalties compared to older models.
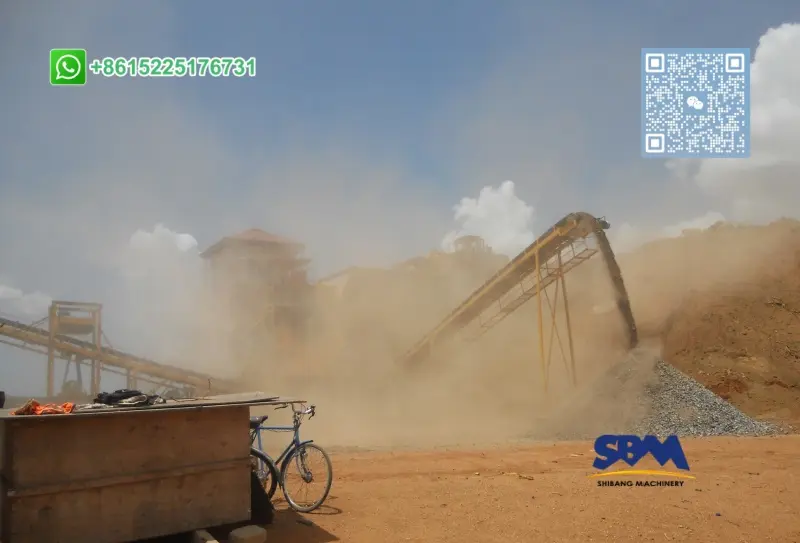
Internal Linking Opportunities
- Learn how proper installation affects noise levels: How to Install a Jaw Crusher for Optimal Performance.
- Explore vibration analysis tools: Jaw Crusher Vibration Analysis: A Step-by-Step Guide.
- Compare models: PE Series vs C6X Series Jaw Crusher: Price and Performance Breakdown.
Noise reduction in fixed jaw crushers is achievable through a mix of engineering upgrades, acoustic treatments, and proactive maintenance. By adopting strategies like ABH technology and optimized component designs, operators can enhance workplace safety, meet regulatory standards, and improve equipment longevity. For tailored solutions, consider consulting with acoustic engineers or exploring advanced crusher models like the C6X series.
Further Reading:
Bureau du siège social
WhatsApp:+8615225176731
E-mail: [email protected]
Adresse: Non. 1688, Gaoke East Road, Nouveau quartier de Pudong, Shangai, Chine.
Site Internet: https://www.mill-sbm.com/
Contenu des articles
Messages récents
- Crusher à mâchoire pour le traitement du calcaire: Un guide de l'efficacitéComme le calcaire est largement utilisé dans la construction et l'industrie, Son traitement nécessite un broyeur de mâchoire solide et durable pour répondre aux besoins de l'industrie. Parmi les nombreux concasseurs, La mâchoire…
- Impact Crusher avec 300 TPH pour les grands projetsLorsque les géants miniers font face à des montagnes de minerai de fer ou de démolitions urbaines, génèrent des avalanches en béton, 300 TPH Impact Crusher apparaît comme des titans de transformation des matériaux. Au-delà des spécifications de base, Nous disséquons comment ces industriels…
- Broyeur à impact abordable: Un changement de jeu pour les petites entreprises de constructionLes petites entreprises de construction sont souvent confrontées à des contraintes budgétaires, pourtant besoin d'équipement fiable – Un concasseur à impact abordable. Ce broyeur peut combler l'écart, fournir un traitement de matériaux efficace sans un énorme capital…