E-mail: [email protected]
Comprendre les composantes clés des concasseurs d'impact pour une efficacité de concassage optimale
Ce guide explore les éléments clés des concasseurs d'impact, leurs fonctions, et applications réelles dans les industries mondiales.
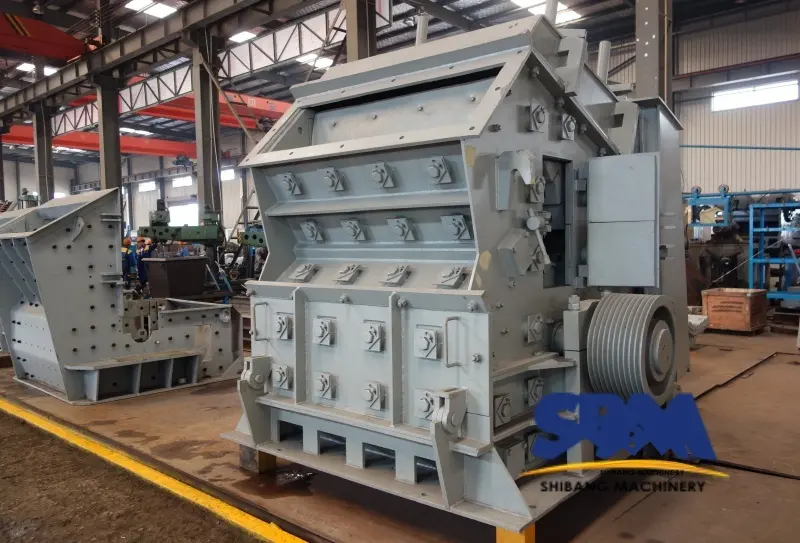
Composants clés des concasseurs d'impact
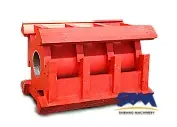
1. Assemblage du rotor: The Heart of Crushing Efficiency
The rotor is the central rotating element that generates the force needed to crush materials. Equipped with hammers or blow bars, it spins at high speeds to strike incoming feed. Par exemple, le Machine de fabrication de sable VSI6X (producing 100–583 tons/hour) uses a heavy-duty rotor with wear-resistant alloys, ideal for processing granite in UK quarries.
Key Features:
- Blow Bars: Replaceable metal bars attached to the rotor.
- Rotor Discs: Secure blow bars and balance rotation.
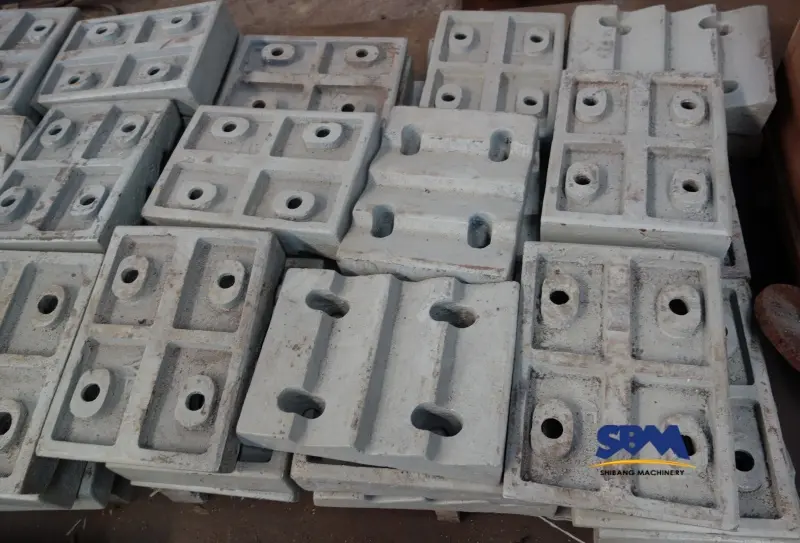
2. Impact Aprons and Grates: Shaping the Final Product
Impact aprons (or breaker plates) line the crushing chamber, redirecting materials for secondary collisions. Adjustable grates control output size, ensuring uniformity. A German recycling plant using a Concasseur VSI (60–520 tons/hour) reported a 30% improvement in slag recycling efficiency by optimizing apron gaps.
3. Drive System: Powering Performance
The motor and belt/pulley system drive the rotor. High-torque motors, like the 315 kW unit in the tertiary crusher, enable consistent crushing of hard rocks in U.S. mining operations.
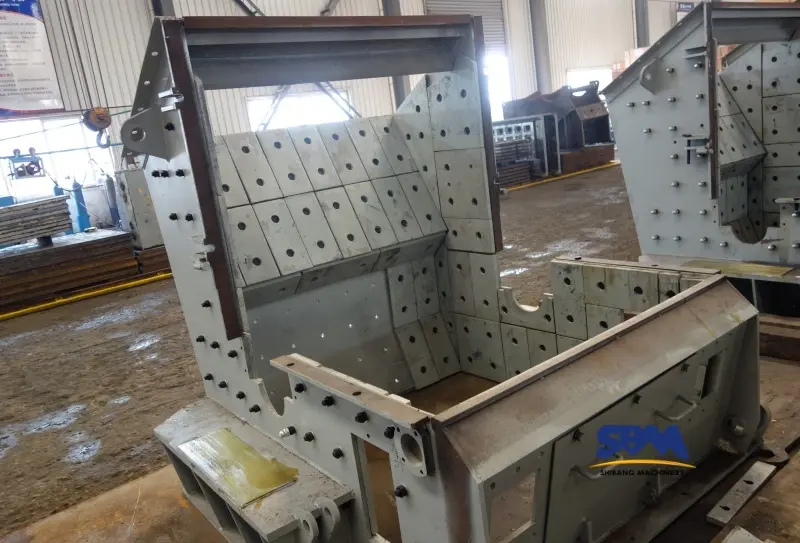
4. Housing and Frame: Durability Under Pressure
The crusher’s outer structure withstands extreme forces. Robust steel frames, such as those in primary impact crushers, ensure stability during high-volume operations6.
Global Applications of Impact Crushers
Étude de cas 1: Fixed Crusher for Slag Recycling in Germany
A steel plant in Dortmund uses a Concasseur à percussion PFW to process 400 tons of slag daily. Adjustable aprons and tungsten carbide blow bars reduce wear, achieving 95% material reuse.
Étude de cas 2: How to Crush Rocks Efficiently in Australia
A Queensland quarry employs an CI5X Impact crusher with a multi-functional rotor to produce road base aggregates. Its 585-ton/hour capacity cuts operational costs by 20%.
Maintenance Tips for Longevity
- Inspect Blow Bars Regularly: Replace worn bars to maintain crushing efficiency.
- Lubricate Bearings: Prevent overheating in the drive system.
- Adjust Apron Gaps: Optimize output size for specific materials like limestone or recycled concrete.
Conclusion: Optimizing Impact Crusher Performance
From the rotor to the housing, key components of impact crushers play a critical role in material processing. Whether for slag recycling or rock crushing, selecting the right impact crusher model—such as PF, PFW, CI5X, TOUT LE MONDE, VSI5X or VSI6X—ensures high efficiency and cost savings. For tailored solutions, explore our guides on efficacité de concassage et how to crush rocks effectively.
Bureau du siège social
WhatsApp:+8615225176731
E-mail: [email protected]
Adresse: Non. 1688, Gaoke East Road, Nouveau quartier de Pudong, Shangai, Chine.
Site Internet: https://www.mill-sbm.com/
Contenu des articles
Messages récents
- Crusher à mâchoire pour le traitement du calcaire: Un guide de l'efficacitéComme le calcaire est largement utilisé dans la construction et l'industrie, Son traitement nécessite un broyeur de mâchoire solide et durable pour répondre aux besoins de l'industrie. Parmi les nombreux concasseurs, La mâchoire…
- Impact Crusher avec 300 TPH pour les grands projetsLorsque les géants miniers font face à des montagnes de minerai de fer ou de démolitions urbaines, génèrent des avalanches en béton, 300 TPH Impact Crusher apparaît comme des titans de transformation des matériaux. Au-delà des spécifications de base, Nous disséquons comment ces industriels…
- Broyeur à impact abordable: Un changement de jeu pour les petites entreprises de constructionLes petites entreprises de construction sont souvent confrontées à des contraintes budgétaires, pourtant besoin d'équipement fiable – Un concasseur à impact abordable. Ce broyeur peut combler l'écart, fournir un traitement de matériaux efficace sans un énorme capital…