Surel: [email protected]
Cara melumasi bantalan crusher rahang: Panduan ahli untuk mencegah kegagalan
Proper bearing lubrication prevents 68% daripenghancur rahang breakdowns in quarry operations. This guide details professional techniques to lubricate jaw crusher bearings effectively, ensuring 10,000+ hours of reliable service. We’ll cover grease selection, injection methods, and criticalpreventive maintenance strategies used by industry leaders.

Why Bearing Lubrication Matters
Jaw crusher bearings operate under extreme loads (hingga 200 tons force) and temperatures exceeding 80°C. Inadequate lubrication causes:
- Premature wear (reducing lifespan by 75%)
- Overheating failures (15% of unplanned downtime)
- Increased energy consumption (18-25% higher)
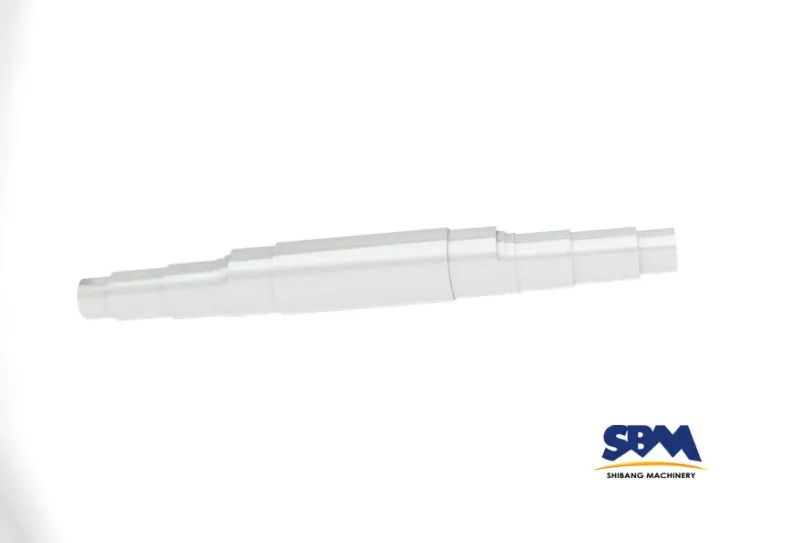
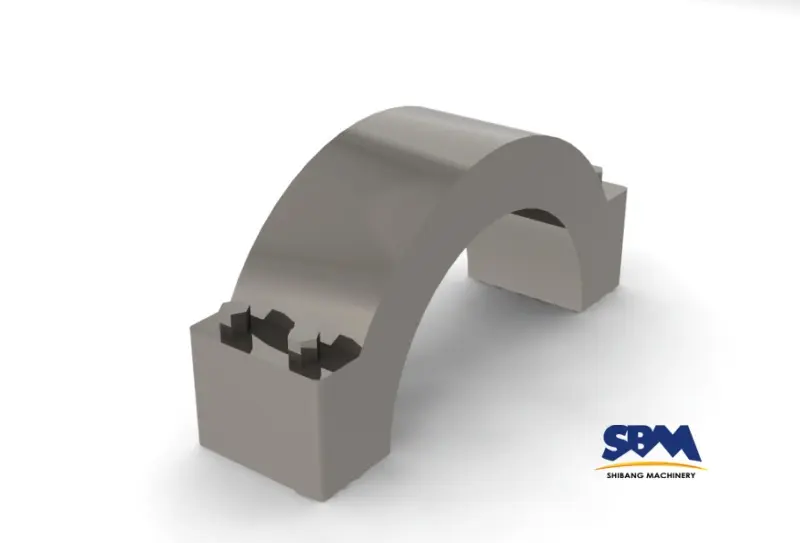
Step-by-Step Lubrication Process
1. Select the Right Lubricant
Condition | Grease Type | Viscosity |
---|---|---|
Normal | Lithium Complex | NLGI #2 |
High Temp | Polyurea | NLGI #1.5 |
Wet Environment | Calcium Sulfonate | NLGI #3 |
2. Clean Bearing Surfaces
Use solvent flushing to remove old grease (part of routine maintenance):
- Disengage crusher power
- Remove grease fittings
- Flush with kerosene until runoff clears
3. Calculate Grease Quantity
G = 0.114 × D × B Where: G = Grams of grease D = Bearing bore (mm) B = Bearing width (mm)
Contoh: 150mm bore × 75mm width = 1,282g
4. Apply Grease Correctly
Proper Injection Method:
- Use high-pressure grease gun (5,000-7,500 psi)
- Pump grease slowly until purge port showsfresh grease
- Rotate eccentric shaft during application for even distribution
Critical Tip: Avoid overgreasing – excess grease increases internal pressure by 30-40%, damaging seals.
5. Verify Lubrication Effectiveness
Tes | Acceptable Range | Tool |
---|---|---|
Temperature | 65-75°C | Infrared thermometer |
Vibration | <4 mm/s RMS | Vibration analyzer |
Grease Color | No dark streaks | Clean cloth test |
6. Document Maintenance Records
Track key parameters using digital maintenance logs:
Date: 2024-03-15 | Bearing: Eccentric Grease Type: Mobilith SHC 220 Quantity: 1200g Post-lube Temp: 68°C | Vibration: 3.2 mm/s
7. Implement Condition Monitoring
- Weekly: Check grease consistency withstiffness test
- Monthly: Send grease samples for lab analysis
- Annually: Perform full bearing inspection during shutdowns
Common Lubrication Mistakes
- Overgreasing: Causes seal damage (30% of failures)
- Mixing Greases: Creates incompatible chemical reactions
- Ignoring Temperature: Standard grease fails above 90°C
Advanced Monitoring Techniques
Infrared Thermography
Detect under-lubrication through temperature anomalies duringcrusher operation:
- Normal range: 65-75°C
- Warning threshold: >85°C
Real-Time IoT Sensors
Install smart sensors to monitor:
- Grease film thickness (>25μm required)
- Bearing load distribution (±15% variance limit)
- Lubricant oxidation levels (TAN <2 mg KOH/g)
Vibration Analysis
Use wireless sensors to monitor bearing condition:
Vibration Level | Action Required |
---|---|
<4 mm/s | Normal operation |
4-7 mm/s | Inspect lubrication |
>7 mm/s | Immediate shutdown |
Lubrication Schedule Template
Component | Frequency | Grease Type |
---|---|---|
Eccentric Bearings | Every 8 jam | EP-2 Lithium |
Toggle Bearings | Every 40 jam | Moly-based |
Flywheel Bearings | Monthly | Polyurea |
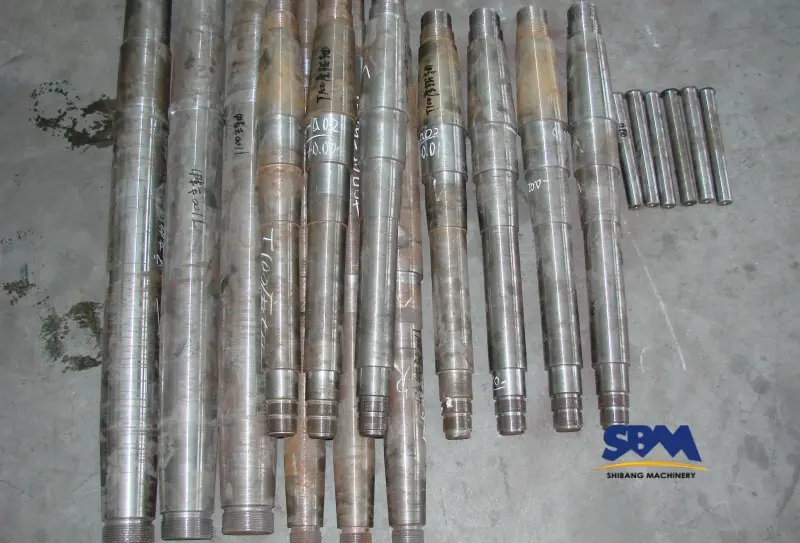
Studi kasus: Solving Premature Bearing Failure
A granite quarry extended bearing life from 6 ke 18 months by:
- Installing automatic grease metering systems
- Implementing our 7-step protocol
- Training staff on proper crusher startup procedures
Essential Tools for Proper Lubrication
- Grease compatibility chart (prevent chemical reactions)
- Digital torque wrench for fitting installation (35-50 N·m)
- Ultrasonic grease thickness gauge
Lubrication as Performance Strategy
Masteringhow to lubricate jaw crusher bearings reduces maintenance costs by 40% and extends component life. Remember: Effective lubrication combines proper crusher operation, quality greases, and data-driven monitoring. Implement these protocols with yourpreventive maintenance program for maximum equipment availability.
Kantor Pusat
ada apa:+8615225176731
Surel: [email protected]
Alamat: TIDAK. 1688, Jalan Timur Gaoke, Kabupaten baru Pudong, Shanghai, Cina.
Situs web: https://www.mill-sbm.com/
Isi Artikel
Tulisan Terbaru
- Cara Memilih Ukuran Crusher Jaw yang Tepat untuk Industri Anda?Selecting the right jaw crusher size isn’t a guessing game—it’s a science rooted in material dynamics and operational calculus. For industries from hard-rock mining to urban concrete recycling, even a…
- Apa penyebab kerusakan pada piring crusher rahang?Because it is under tremendous pressure during material processing, there are many causes for the damage of the jaw crusher plate. Understanding why they degrade prematurely can save costs and…
- Apa jambu rahang yang ideal untuk crushing granit?Granite’s relentless toughness demands jaw crusher built to endure—think armored jaws and unyielding frames. Prioritize crushers that combine brute force with precision engineering, like heat-treated alloys and adaptive crushing chambers.…