ईमेल: [email protected]
साइटवर जबडा क्रशर स्थापित करीत आहे: 2025 बांधकाम संघांसाठी फील्ड मार्गदर्शक
जेव्हा ओंटारियो स्टोन को. टीमने गेल्या महिन्यात त्यांचे नवीन पीई 1200 × 1500 जबडा क्रशर स्थापित केले, त्यांनी सेटअप वेळ कापला 3 दिवस 18 तास - सेव्हिंग $15,000 कामगार खर्चात. Here’s how modern construction site is revolutionizing crusher installation, blending old-school mechanical know-how with 2025’s smart tech.
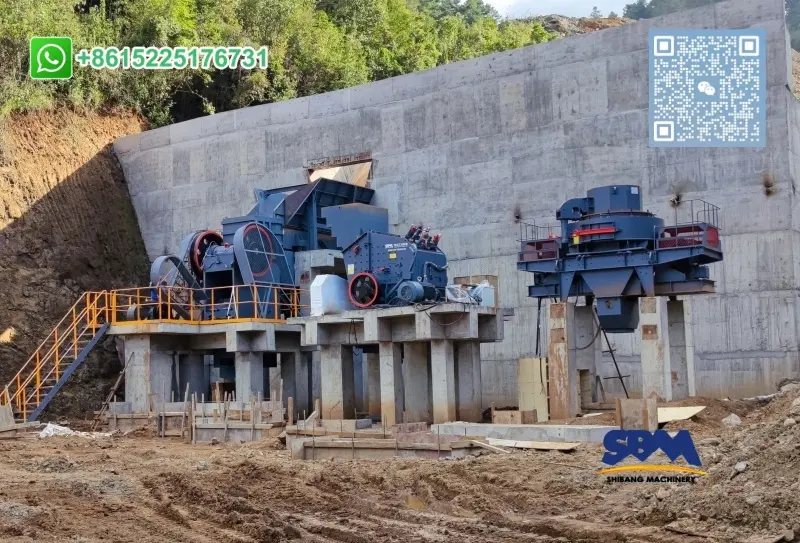
द 4 Golden Rules of Crusher Installation
Golden Rule 1: Precise foundation preparation – the foundation of installation success
Key operations:
- Concrete strength matching: The foundation concrete grade must be ≥C30, and the thickness must be 1.5 times the weight of the equipment (उदाहरणार्थ, a 300-ton crusher requires a 450-ton foundation)
- Drainage system design: Set a 5° outward slope to prevent water accumulation from causing metal corrosion (in the case of Sudbury Nickel Mine in Canada, this reduced the problem of bolt rust by 80%)
- Anchor bolt pre-tightening technology: Use M42 high-strength anchor bolts, and increase the torque to 850N·m in three steps (the Chilean copper mine project uses a laser torque meter to achieve ±2% accuracy control)
- Failure case: मध्ये 2023, a gold mine in South Africa had a foundation tilt of 0.5°, which caused the wear rate of the movable jaw assembly to accelerate by 300%, with an annual loss of $1.2 million.
Golden Rule 2: Modular assembly process – a balance between efficiency and safety
Five-step assembly method:
- Chassis positioning: laser total station calibrates horizontality (error ≤ 0.1mm/m)
- Eccentric shaft installation: hydraulically press in after heating to 80°C to avoid cold installation deformation (refer to the Finnish factory standard)
- Moving jaw lifting: double-point balance beam technology to prevent 1.8-ton components from swinging (Norway Arctic Iron Mine uses drones to assist in lifting, increasing efficiency by 40%)
- Drive belt tensioning: ultrasonic dynamometer ensures tension value of 85-90N (Australian lithium mine project reduces belt slippage by 60% through this method)
- Lubrication system pre-activation: Before injecting high-temperature lithium-based grease, flush the pipeline with diesel circulation (impurity removal rate increased by 92% in the Congolese cobalt mine case)
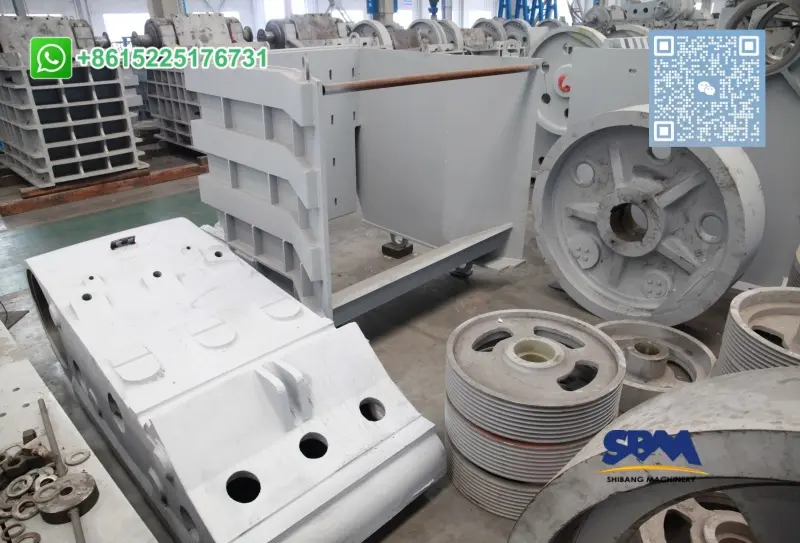
Golden Rule 3: Intelligent calibration – from empiricism to data-driven
Three major digital tool applications:
- 3D laser scanning: Generate a three-dimensional model of the crushing chamber to ensure that the parallelism between the movable jaw and the fixed jaw is ≤0.2mm (after Vale of Brazil adopted this method, the liner life was extended to 2,200 तास)
- IoT vibration monitoring: Real-time warning of abnormal frequency during the installation phase (LKAB Iron Mine in Sweden used this technology to reduce the commissioning time from 48 hours to 6 तास)
- Thermal imaging pre-inspection: The alarm is triggered when the temperature difference of the bearing seat exceeds 5℃ (Oyu Tolgoi Copper and Gold Mine in Mongolia successfully prevented 3 major failures)
- Cost-effectiveness: Data from Chile’s Codelco shows that intelligent calibration reduces installation labor costs by 35%, but requires an initial investment of $50,000 in equipment purchase costs.
Golden Rule 4: Full-cycle Verification System – From Static Installation to Dynamic Optimization
Four-stage Verification Method:
- No-load test: Measure vibration value <4.5मिमी/से (ISO 10816-3 standard)
- Load increment: Load in steps of 25%-50%-75%-100%, monitor current fluctuation ≤10%
- Particle size sampling: Sampling every 30 minutes to verify the output particle size distribution (Indonesian nickel mine uses AI image analysis system to adjust CSS in real time)
- Energy efficiency audit: Compare kWh/ton index with manufacturer’s commitment value (a project in the Democratic Republic of Congo found transmission system defects through audit and claimed $280,000)
- Typical case: Australian FMG Group found foundation settlement problems through full-cycle verification during the installation acceptance of Pilbara iron ore, avoiding potential losses of $4.5 million.
Extended points: Economic decision support
Selection of new and old equipment: Although the installation cost of second-hand equipment is 15% lower, the calibration time is increased by 50% (see [Cost comparison analysis of new and old jaw crushers] for details)
Maintenance pre-planning: Reserving sensor interfaces during the installation phase can increase [maintenance efficiency by 70%] in the later stage
The above rules integrate mechanical engineering, material science and digital technology. It is recommended to refer to [Jaw Crusher Selection Guide] आणि [Capacity Optimization Manual] to formulate implementation plans based on specific working conditions.
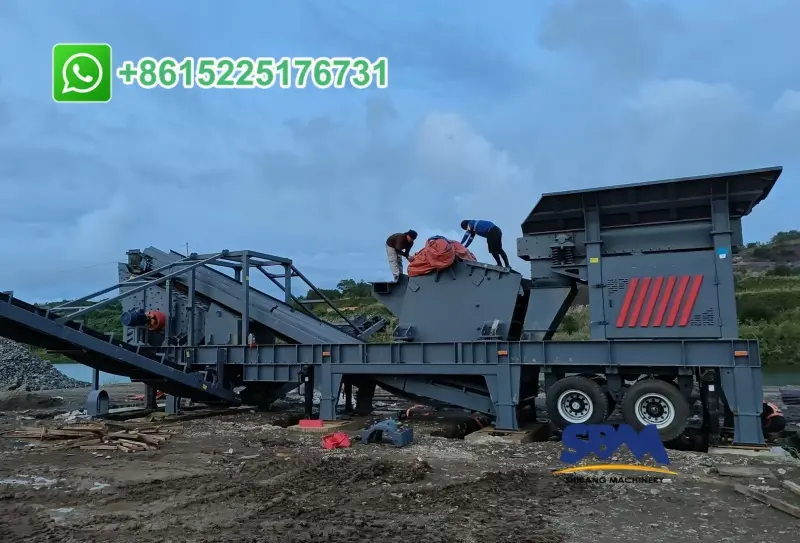
Smart Tools Changing the Game
Laser Alignment Kits
Reduces jaw plate gap errors by 92% compared to manual measurement
IoT Vibration Sensors
Detect foundation issues in real-time (used in Norway’s Arctic mines)
Cost-Saving Pro Tips
- Rent vs Buy: For projects under 6 months, used mobile units save 40% on transport
- Pre-Assembled Kits: नवीन 2025 models arrive 70% pre-built
- Hybrid Power: Solar-diesel combos cut energy costs by 35%
The Canadian Success Blueprint
Ontario 500T/H Quarry Installation
Step | Time | Tech Used |
---|---|---|
Foundation Pour | 2 days | Fast-cure concrete (+accelerator) |
Mechanical Assembly | 6 तास | Laser-guided crane systems |
Test Run | 1.5 तास | Vibration analysis software |
Result: Achieved target 450tph capacity within 2% tolerance
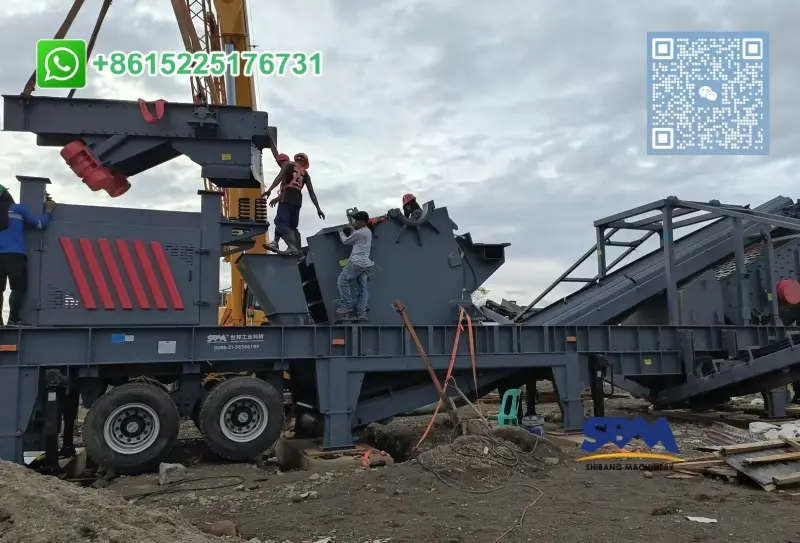
When Things Go South: Quick Fixes
Vibration Overload
Symptom: 5mm frame movement during first run
Fix: Re-torque anchor bolts + add rubber isolators
Belt Slip
Symptom: 15% power loss
Fix: Adjust tension to 85-90N using ultrasonic gauge
Future-Proofing Your Setup
- AI Optimization: नवीन2025 C6X models auto-adjust based on material hardness
- मॉड्यूलर डिझाइन: Swap from granite to recycling mode in 4 तास
- Drone Surveys: Pre-site analysis reduces foundation errors by 60%
Expert Verdict: Installation = 50% of Performance
As Toronto-based engineer Mark Wu notes: “A $2M crusher installed poorly performs like a $800k unit. But a mid-rangeजबडा क्रशर with precision setup can outperform premium models.”
मुख्यालय कार्यालय
Whatsapp:+8615225176731
ईमेल: [email protected]
पत्ता: नाही. 1688, गावके पूर्व रस्ता, पुडोंग नवीन जिल्हा, शांघाय, चीन.
संकेतस्थळ: https://www.mill-sbm.com/
लेखातील सामग्री
अलीकडील पोस्ट
- Gold Ore Processing: Jaw Crusher EfficiencyEffective gold ore processing hinges on precise crushing operations, where jaw crushers convert rugged deposits into optimized feedstock. Discover how to fine-tune these machines for peak productivity without compromising worksite…
- Crushing River Gravel with Jaw CrushersA cornerstone of modern construction, river gravel delivers unmatched toughness and adaptability for roads, ठोस, and erosion control. Yet its rugged, irregular nature demands machinery built to endure—enter jaw crushers.…
- How to Choose the Right Jaw Crusher Size for Your Industry?Selecting the right jaw crusher size isn’t a guessing game—it’s a science rooted in material dynamics and operational calculus. For industries from hard-rock mining to urban concrete recycling, even a…