E-mail: [email protected]
How Jaw Crusher Design Enhances Operational Efficiency in Mining and Construction
The efficiency of a jaw crusher depends on its design. These design principles maximize production while minimizing energy consumption and downtime. Below, we analyze which key design features contribute to its efficiency, combined with global case studies and technical insights.
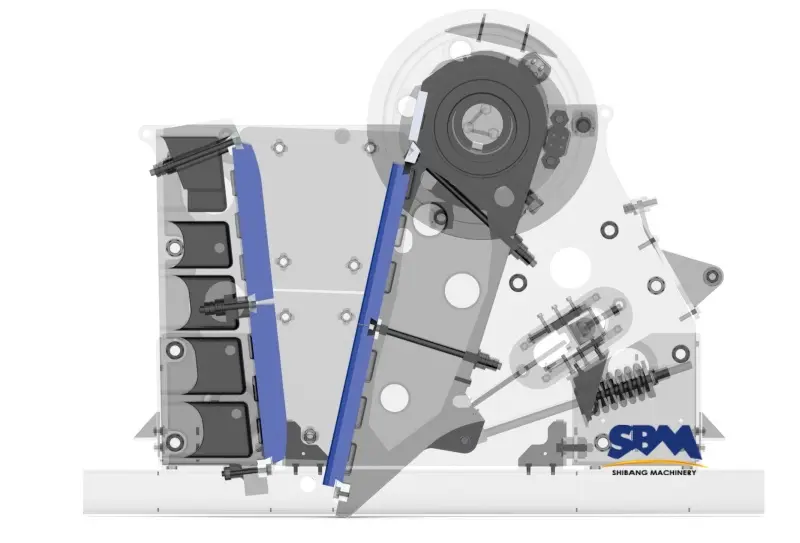
1. Structural Innovations: The Backbone of Crushing Performance
New jaw crusher, such as the C6X jaw crusher, features advanced structural designs to optimize force distribution and durability. Key elements include:
- V-Shaped Crushing Chambers: This design widens the feed inlet, allowing larger raw materials (Por exemplo, up to 1,200mm in models like the C6X200 series) to enter without pre-screening. The geometry ensures progressive compression, reducing wear on jaw plates and boosting throughput by 15–20% compared to traditional chambers.
- Reinforced Components: High-quality cast steel for moving jaws and forged eccentric shafts (as seen in European jaw crushers) enhance load-bearing capacity, critical for processing hard materials like scheelite or gold ore ingold mine crusher operations.
Estudo de caso: A Swedish iron ore mine reported a 25% increase in productivity after upgrading to a crusher with a V-shaped chamber and hydraulic discharge adjustments.
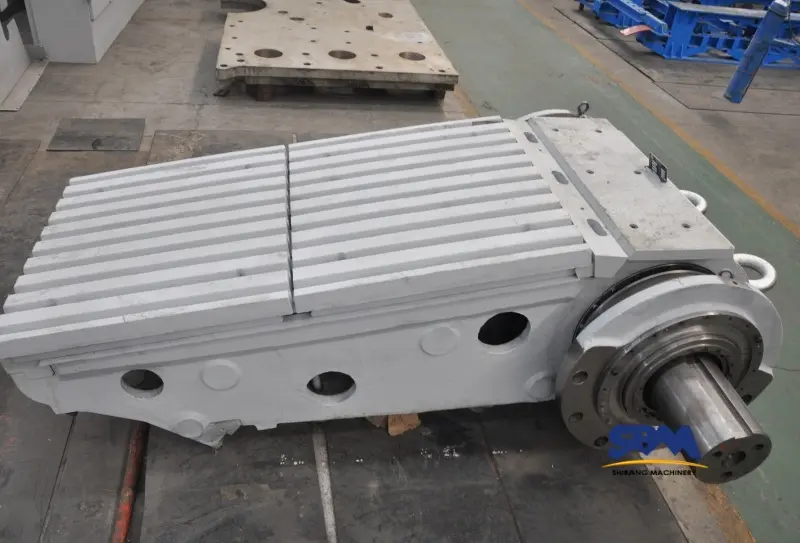
2. Adjustability and Automation: Precision in Output Control
Efficiency isn’t just about power—it’s about adaptability. Jaw crushers now integrate:
- Hydraulic Wedge Systems: Replacing manual shim adjustments, these systems enable real-time modifications to the discharge opening. This flexibility ensures consistent product sizing, vital for meetingfixed jaw crusher capacity requirements in aggregate production.
- Centralized Lubrication: Automated lubrication reduces maintenance downtime by 30%, as observed in Australian copper mining operations using SBM crusher models.
3. Material Science and Wear Resistance
The longevity of components directly impacts operational costs. Innovations include:
- Reversible Jaw Plates: Made from BTMcr20 alloy, these plates extend service life by 40% in abrasive environments like scheelite processing plants.
- Toothed Guard Plates: These increase the effective length of jaw plates, improving crushing force distribution and reducing energy consumption per ton.
Estudo de caso: A Canadian limestone quarry reduced replacement costs by 50% after switching to crushers with reversible jaw plates and integrated wear monitoring.
4. Safety and Energy Efficiency: Balancing Power and Protection
Modern designs prioritize both operator safety and sustainability:
- Overload Protection: Sensors and hydraulic systems automatically halt operations during jams, preventing equipment damage. This feature is critical in high-capacitySBM crusher units used in South African platinum mines1.
- Eco-Friendly Motors: Energy-efficient motors reduce power consumption by up to 20%, aligning with global carbon reduction goals.
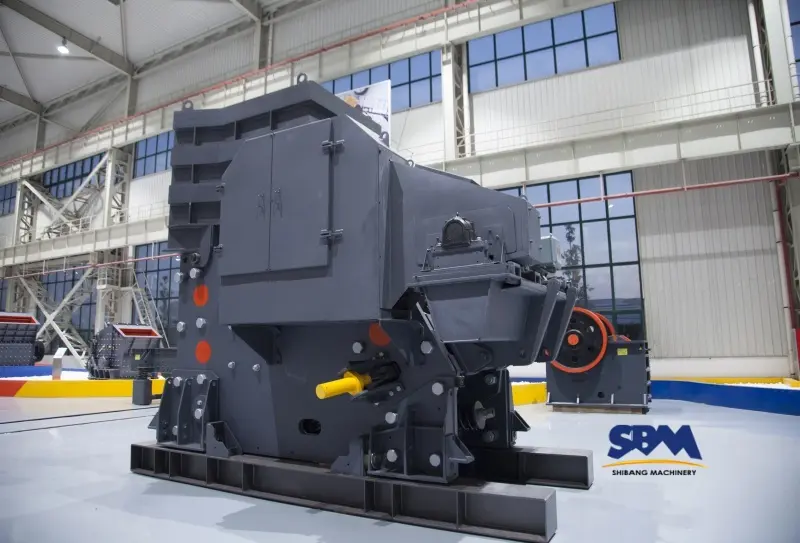
5. Global Applications: Design Tailored to Local Needs
Jaw crusher efficiency varies by application. Por exemplo:
- Gold Ore Processing: In Ghana, crushers with hermetic structures minimize dust contamination during primary crushing, ensuring sample accuracy.
- Scheelite Crusher Solutions: German tungsten processors favor crushers with adjustable discharge ranges (3–38mm) to accommodate varying mineral hardness.
From hydraulic adjustments to wear-resistant alloys, jaw crusher design is a symphony of engineering aimed at maximizing efficiency. Whether optimizingfixed jaw crusher capacity for urban construction projects or tailoringscheelite crusher configurations for mineral processing, these innovations ensure reliability across industries. For specialized needs, explore models like the C6X jaw crusher or consult global suppliers like SBM crusher to match design with demand.
Sede Escritório
Whatsapp:+8615225176731
E-mail: [email protected]
Endereço: Não. 1688, Gaoke East Road, Novo distrito de Pudong, Xangai, China.
Local na rede Internet: https://www.mill-sbm.com/
Conteúdo do Artigo
Postagens recentes
- What are the causes of damage to the jaw crusher plate?Because it is under tremendous pressure during material processing, there are many causes for the damage of the jaw crusher plate. Understanding why they degrade prematurely can save costs and…
- What is the ideal jaw crusher for granite crushing?Granite’s relentless toughness demands jaw crusher built to endure—think armored jaws and unyielding frames. Prioritize crushers that combine brute force with precision engineering, like heat-treated alloys and adaptive crushing chambers.…
- Jaw Crusher for Limestone Processing: A Guide to EfficiencyAs limestone is widely used in construction and industry, its processing requires strong and durable jaw crusher to meet the needs of the industry. Among the many crushers, the jaw…