E-mail: [email protected]
Qual é o papel do britador de mandíbula no britador de rocha?
In the context of a rock crusher, a jaw crusher plays a fundamental role as the primary crushing equipment. Jaw crushers have wide application in mining, construção, and demolition industries to crush materials like limestone, granito, basalto, quartz, and ore. They also participate in recycling operations, breaking down waste materials such as concrete and asphalt. Here’s an overview of its role:
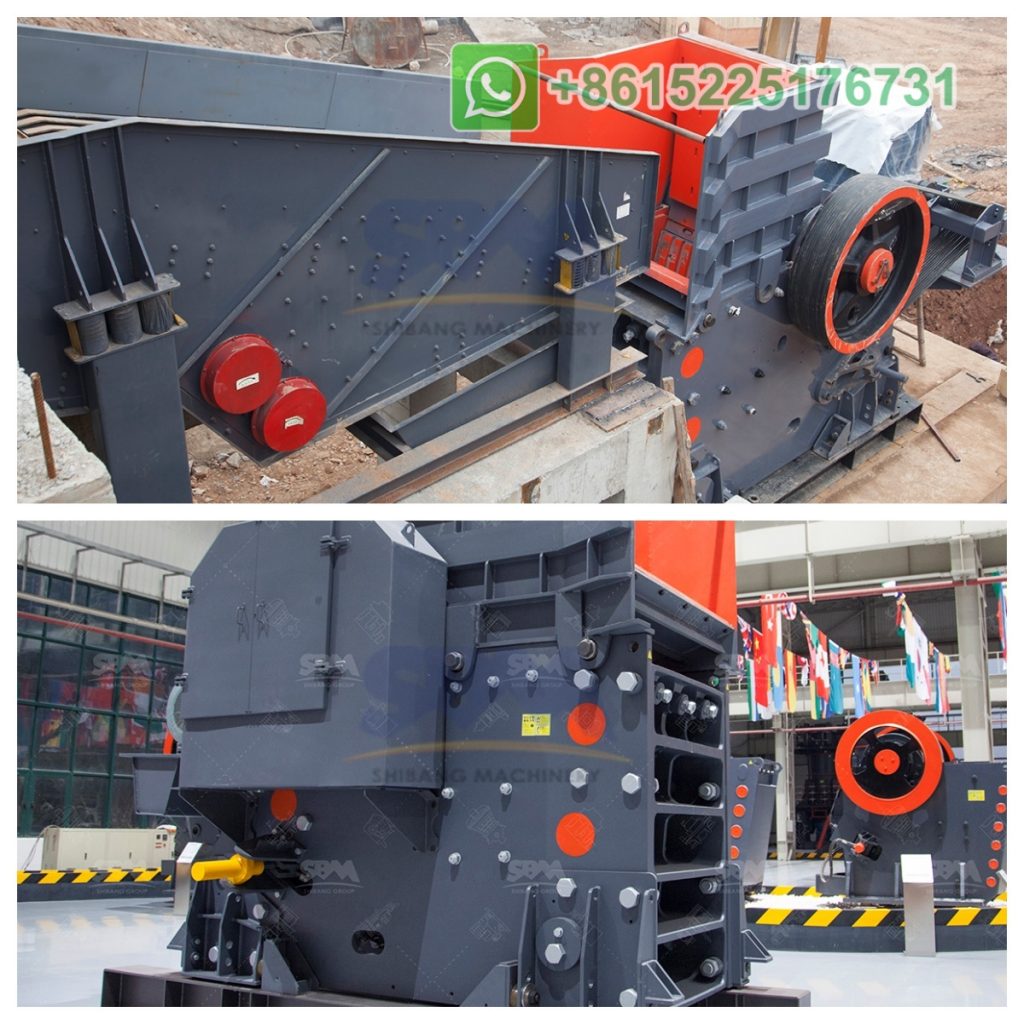
Primary crusher in stone crushing line
O britador de mandíbula is the first stage in the rock crushing process. It handles large and hard rocks, breaking them into smaller pieces that are more manageable for secondary crushers or further processing.
By using a compressive force, it crushes rocks between two hard surfaces (the fixed and the movable jaw).
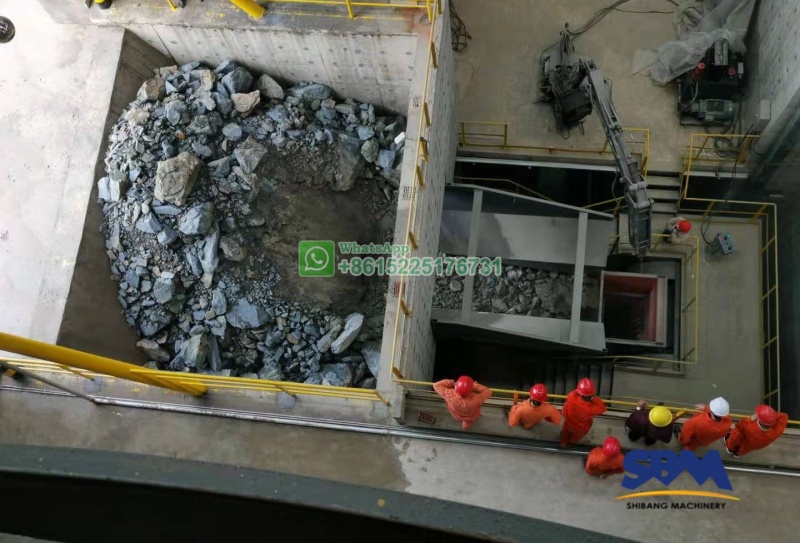
What are the advantages of jaw crusher as primary crusher?
- Raw stones from quarries or mines are usually large and irregular in size.
- High capacity and ability to handle large feed sizes.
- Simple structure, Manutenção fácil, and reliability.
- Suitable for crushing hard and abrasive materials like granite and basalt.
Efficient size reduction of materials
Jaw crushers reduce the size of rocks and stones, making them suitable for secondary or tertiary crushers, such as cone crushers or impact crushers.
This initial size reduction ensures that the material is efficiently processed downstream.
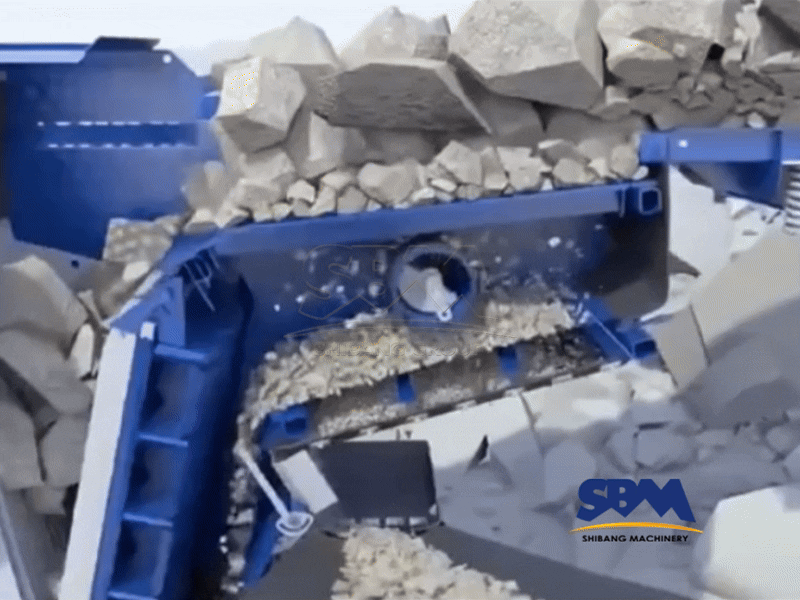
What is the working principle of jaw crusher?
The basis of the working principle of the jaw crusher is compression, which works to reduce the size of large rocks and materials.
1. Crushing Mechanism
The jaw crusher consists of two main parts: a fixed jaw and a movable jaw. These two jaws form a V-shaped crushing chamber. Movable jaws mounted on pivots that can move forward and backward. The fixed jaw remains stationary.
2. Feed Material
A feeder delivers rock or other material (through a hopper) into the top of the crushing chamber. The material enters between the two jaws.
3. Compression Action
When the movable jaw moves toward the fixed jaw during the downstroke, the two jaws squeeze the material in between and crush it. This compressive force causes the material to break into smaller pieces.
4. Descarga de Material Triturado
When the movable jaw moves away from the fixed jaw (during the upstroke), the crushed material falls from the bottom of the rock crusher through the discharge opening.
5. Crushing Cycle
The cycle of the movable jaw moving towards and away from the fixed jaw happens repeatedly, allowing the material to be progressively crushed into smaller and smaller pieces.
Versatilidade
It can crush various types of rock, including:
Hard materials (granito, basalto, quartz).
Medium hard materials (calcário, sandstone).
So its adaptability allows it to be used in a variety of applications, incluindo mineração, construction and demolition recycling.
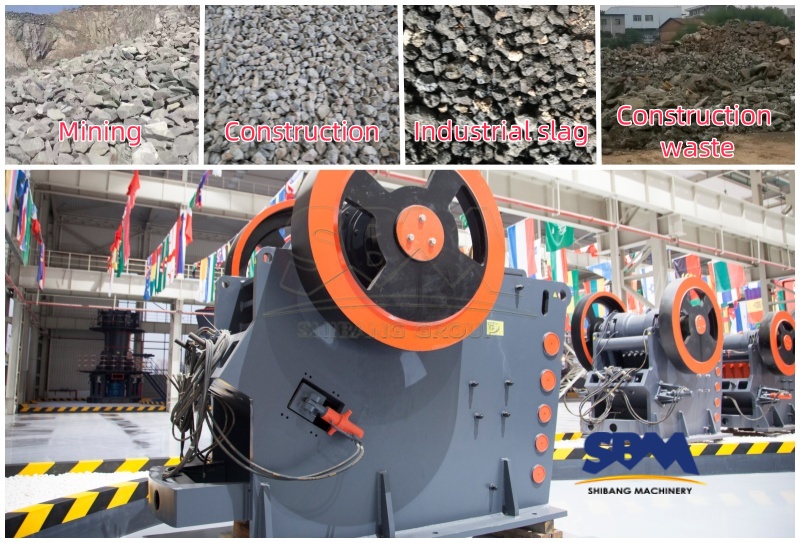
Why is jaw crusher universal?
The versatility of the jaw crusher comes in the form of:
1. Configurações ajustáveis
- Universal jaw crushers often feature adjustable settings for the size of the output product, making them suitable for a wide range of materials and industries.
- The rock crusher’s settings can be adjusted to handle different sizes of feed material, allowing for greater flexibility in application.
2. Effective crushing method: Dual-Action Crushing
Jaw crushers typically use a combination of compression and shear forces. Rock crushers move in both circular and linear motions, allowing them to effectively crush different types of materials, from harder, denser materials to softer, more brittle materials.
3. Wide Range of Material Types
- The versatility of the jaw crusher is also reflected in its ability to effectively handle a wide range of materials, including hard minerals, minérios, aggregates, and even some recycled materials.
- This versatility makes it widely used in various industries such as mining, construção, e reciclagem.
4. Simple Design in Structure
Jaw crushers are generally known for their simple and sturdy design. This simple structure is not only easier to maintain and operate, but also suitable for both primary and secondary crushing of different types of materials.
5. Reliability and stability in performance
The combination of its design features (such as toggle plates, heavy-duty bearings and strong and wear-resistant jaw plates) ensures that the jaw crusher can work stably and reliably for a long time. Therefore, it has been favored by many investors in the crushing industry.
6. Flexibility in crushing processes
Depending on the model and settings, the versatility of the jaw crusher can also be reflected in the processing of different feed sizes, equipped with different types of jaws (smooth or with teeth), and meet various capacities. Therefore, it can meet both fixed and portable needs, which further increases its versatility and flexibility in different crushing environments.
Provides consistent feed size to secondary crusher
The jaw crusher ensures uniform feed size and prepares the material for subsequent crushing stages.
This prevents clogging and improves the performance of other equipment in the rock crusher system.
Durable and low maintenance
The jaw crusher is durable and reliable, and can withstand the rigors of crushing hard materials.
The simple design requires almost no maintenance, which reduces downtime in the rock crushing process.
In summary of jaw cruher rock cusher
The jaw crusher is indispensable in the rock crushing system as it initiates the crushing process. It breaks large pieces of rock into smaller, more manageable sizes, ensuring the overall efficiency and effectiveness of the entire crushing operation.
Sede Escritório
Whatsapp:+8615225176731
E-mail: [email protected]
Endereço: Não. 1688, Gaoke East Road, Novo distrito de Pudong, Xangai, China.
Local na rede Internet: https://www.mill-sbm.com/
Conteúdo do Artigo
Postagens recentes
- What Are the Top Efficient Stone Crusher Models?Matching your stone crusher models to the job isn’t just about efficient—it’s about solving operational bottlenecks. SBM China equipment, like the HP Series for hard rock mining or the K3…
- Jaw Crusher Applications in Agricultural Limestone ProcessingFrom Midwest prairies to Southeast Asian paddies, crushed limestone breathes life into acidic farmland—but unlocking its full potential demands jaw crushers engineered to tackle regional rock formations, balancing power with…
- Gold Ore Processing: Jaw Crusher EfficiencyEffective gold ore processing hinges on precise crushing operations, where jaw crushers convert rugged deposits into optimized feedstock. Discover how to fine-tune these machines for peak productivity without compromising worksite…