อีเมล: [email protected]
เครื่องบด VSI
ทุกคน (แรงกระแทกของเพลาแนวตั้ง) เครื่องบด, หรือที่เรียกว่าเครื่องทำทราย, เป็นอุปกรณ์บดที่นิยมใช้ในด้านการผลิตทรายเทียม. มีการใช้กันอย่างแพร่หลายในด้านความสามารถในการผลิตมวลรวมคุณภาพสูงเพื่อการก่อสร้าง. VSI crushers มีให้เลือกหลายประเภท, แต่ละตัวออกแบบสำหรับแอปพลิเคชันเฉพาะ. ประเภททั่วไปรวมถึงใบพัดเปิด, ใบพัด, ร็อคร็อค, และเครื่องบดหินบนเหล็กกล้า. ทางเลือกของประเภทเครื่องบดขึ้นอยู่กับปัจจัยต่าง ๆ เช่นรูปร่างผลิตภัณฑ์ที่ต้องการ, ขนาด, และการขัดของวัสดุอาหารสัตว์.
ประเภทของเครื่องบด VSI
SBM VSI crushers มีสามประเภทหลักสามประเภท: ทุกคน, VSI5X, VSI6X. เครื่องทำทรายแนวตั้ง VSI เป็นที่รู้จักกันทั่วไปว่าเป็นเครื่องบดกระแทกหรือ shaper รวม. VSI Sand Maker เป็นเครื่องทำทรายที่มีประสิทธิภาพสูงรุ่นที่สี่ที่พัฒนาโดย SBM บนพื้นฐานของการแนะนำเทคโนโลยีขั้นสูงของเยอรมันเกี่ยวกับผู้ผลิตทรายและการวิเคราะห์สถานการณ์ในประเทศของอุตสาหกรรมเหมืองแร่.

SBM พัฒนาและตรวจสอบเครื่องทำทรายรุ่นใหม่-VSI5X Maker-บนพื้นฐานของการแนะนำเทคโนโลยีเยอรมันเกี่ยวกับอุปกรณ์ทำทรายและปรับปรุงผู้ผลิตทราย VSI. เครื่องผลิตทราย VSI5X รวมโหมดการบดที่แตกต่างกันสามโหมดและมีสิทธิ์ในทรัพย์สินต่าง ๆ แยกต่างหาก. ณ ตอนนี้, VSI5X Sand Maker เป็นเครื่องจักรมาตรฐานอุตสาหกรรม.

SBM เพิ่มประสิทธิภาพโครงสร้างและฟังก์ชั่นของเครื่องบดกระแทกแบบเพลาแนวตั้งแบบดั้งเดิมเพื่อตอบสนองต่อความต้องการของตลาดที่กำลังเติบโตสำหรับขนาด, ทวีความรุนแรงมากขึ้น, การอนุรักษ์พลังงาน, การคุ้มครองสิ่งแวดล้อม, และทรายที่ทำด้วยเครื่องจักรคุณภาพสูง. ผลที่ตามมา, SBM แนะนำไฟล์ เครื่องทำทราย VSI6X, อุปกรณ์ทำทรายและการปรับเปลี่ยนรุ่นใหม่ที่มีประสิทธิภาพสูงและต้นทุนต่ำ.

เอาต์พุตและขนาด
VSI crushers มีกำลังการผลิตสูงและสามารถสร้างมวลรวมที่ดีและหยาบจำนวนมาก. โดยทั่วไปแล้วเอาต์พุตของเครื่องบด VSI จะวัดเป็นตันต่อชั่วโมง (ทีพีเอช) และอาจแตกต่างกันไปขึ้นอยู่กับวัสดุฟีดและการกำหนดค่าเครื่องบด. ขนาดของผลิตภัณฑ์ขั้นสุดท้ายสามารถปรับได้โดยการเปลี่ยนการตั้งค่าของเครื่องบด.
หลักการทำงาน
หลักการทำงานของเครื่องบด VSI นั้นเกี่ยวข้องกับการใช้แรงแบบแรงเหวี่ยงเพื่อเร่งวัสดุป้อนและโยนมันลงกับทั่งที่อยู่กับที่หรือห้องบดที่มีหินเรียงราย. ผลกระทบนี้ทำให้วัสดุแตกและรูปร่างเป็นขนาดที่ต้องการ. ประสิทธิภาพการใช้พลังงานของ VSI crushers นั้นมาจากใบพัดความเร็วสูง, ซึ่งทำให้มั่นใจได้ว่าการดำเนินการบดขยี้อย่างมีประสิทธิภาพ.
ชิ้นส่วนที่เปราะบาง
เช่นเดียวกับอุปกรณ์เครื่องกลใด ๆ, VSI crushers มีชิ้นส่วนที่มีช่องโหว่ที่ต้องมีการตรวจสอบและบำรุงรักษาเป็นประจำ. ส่วนที่มีช่องโหว่ที่พบมากที่สุด ได้แก่ เคล็ดลับโรเตอร์, จานผู้จัดจำหน่าย, และสวมจาน. ชิ้นส่วนเหล่านี้อาจเสื่อมสภาพเมื่อเวลาผ่านไปเนื่องจากผลกระทบความเร็วสูงและการเสียดสีในระหว่างกระบวนการบดขยี้.
ค่าซื้อ
ต้นทุนการซื้อของเครื่องบด VSI อาจแตกต่างกันไปขึ้นอยู่กับปัจจัยต่าง ๆ เช่นแบรนด์, แบบอย่าง, และคุณสมบัติเพิ่มเติม. โดยทั่วไป, VSI crushers มีให้บริการในราคาที่แตกต่างกันเพื่อรองรับงบประมาณที่หลากหลาย. ขอแนะนำให้เปรียบเทียบราคาและข้อกำหนดจากซัพพลายเออร์ที่แตกต่างกันเพื่อทำการตัดสินใจซื้อที่มีข้อมูล.
ค่าบำรุงรักษา
นอกเหนือจากต้นทุนการซื้อครั้งแรก, จำเป็นต้องพิจารณาค่าบำรุงรักษาระยะยาวของเครื่องบด VSI. ค่าบำรุงรักษารวมถึงค่าใช้จ่ายที่เกี่ยวข้องกับการตรวจสอบปกติ, การเปลี่ยนชิ้นส่วนที่มีช่องโหว่, การหล่อลื่น, และการบำรุงรักษาทั่วไป. การบำรุงรักษาที่เหมาะสมสามารถช่วยยืดอายุการใช้งานของเครื่องบดและเพิ่มประสิทธิภาพประสิทธิภาพ.
วิธีการบำรุงรักษา
เพื่อให้แน่ใจว่าการทำงานที่ราบรื่นและอายุยืนของ VSI เครื่องทำทราย, การบำรุงรักษาอย่างสม่ำเสมอเป็นสิ่งสำคัญ.
- ตรวจสอบชิ้นส่วนที่มีช่องโหว่เป็นประจำสำหรับการสึกหรอและแทนที่เมื่อจำเป็น.
- ทำให้เครื่องบดหล่อลื่นได้รับการหล่อลื่นอย่างดีเพื่อลดแรงเสียดทานและป้องกันการสะสมความร้อนที่มากเกินไป.
- การทำความสะอาดเครื่องบดเป็นประจำเพื่อกำจัดการสะสมของฝุ่นและเศษซาก.
- การตรวจสอบประสิทธิภาพของ Crusher และปรับการตั้งค่าตามที่จำเป็นเพื่อเพิ่มประสิทธิภาพการผลิตและลดการสึกหรอ.
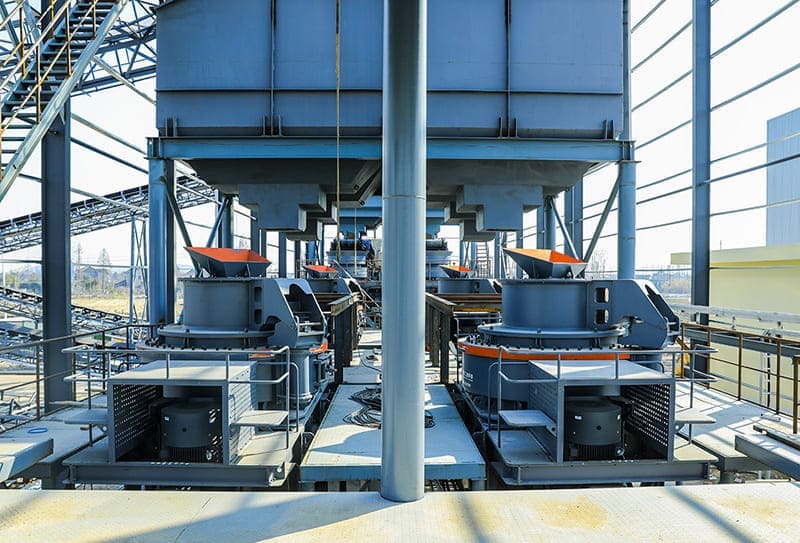
แอปพลิเคชันของ VSI crushers
- การผลิตทรายประดิษฐ์คุณภาพสูงสำหรับการผลิตคอนกรีตและแอสฟัลต์.
- การผลิตหินบดสำหรับการก่อสร้างถนนและโครงการโครงสร้างพื้นฐาน.
- การสร้างมวลรวมที่ดีสำหรับการฉาบปูนและการแสดงผลในอุตสาหกรรมการก่อสร้าง.
- การสร้างและกลั่นมวลรวมเพื่อใช้ในการผลิตองค์ประกอบคอนกรีตสำเร็จรูป.
- การรีไซเคิลและนำวัสดุก่อสร้างกลับมาใช้ใหม่และรื้อถอน.
สำนักงานใหญ่
วอทส์แอพ:+8615225176731
อีเมล: [email protected]
ที่อยู่: เลขที่. 1688, ถนน Gaoke ตะวันออก, เขตผู่ตงใหม่, เซี่ยงไฮ้, จีน.
เว็บไซต์: https://www.mill-sbm.com/
เนื้อหาบทความ
โพสต์ล่าสุด
- What are the causes of damage to the jaw crusher plate?Because it is under tremendous pressure during material processing, there are many causes for the damage of the jaw crusher plate. Understanding why they degrade prematurely can save costs and…
- What is the ideal jaw crusher for granite crushing?Granite’s relentless toughness demands jaw crusher built to endure—think armored jaws and unyielding frames. Prioritize crushers that combine brute force with precision engineering, like heat-treated alloys and adaptive crushing chambers.…
- Jaw Crusher for Limestone Processing: A Guide to EfficiencyAs limestone is widely used in construction and industry, its processing requires strong and durable jaw crusher to meet the needs of the industry. Among the many crushers, the jaw…