E-posta: satış@mill-sbm.com
Çene kırıcı vs nasıl olur. Diğer birincil kırma ekipmanı?
Avustralya’nın demir cevheri kemerlerinden Kanada’nın Petrol Kumlarına, çene kırıcı ve (veya Vs.) Diğer birincil kırma ekipmanı operasyonel başarıyı belirler. Dönme ve darbe kırıcıların niş rolleri vardır, jaw crushers remain the unshakable foundation of mining for hard materials. Let’s analyze their real-world advantages through operational data and unexpected case studies.
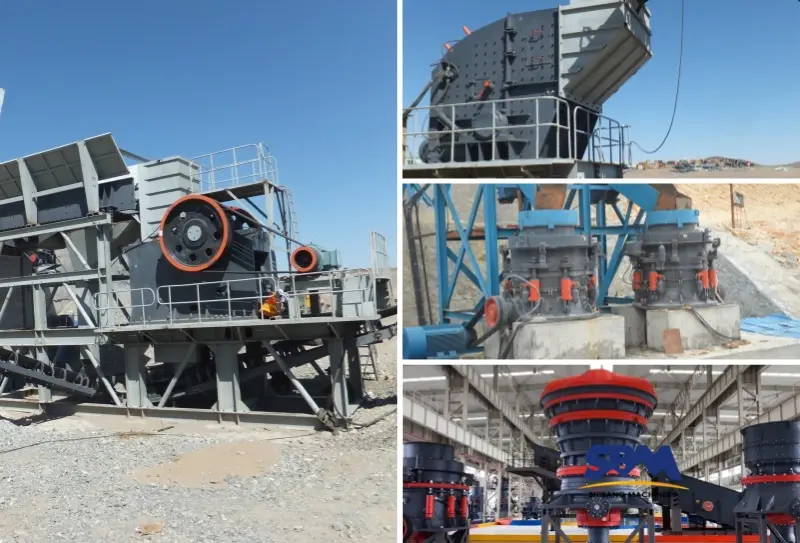
Understanding Primary Crushing Equipment
Primary crushing equipment reduce large raw materials into manageable sizes for downstream processing. Common types include:
- Çene kırıcılar: Use compressive force via fixed and movable jaw plates.
- Gyratory crushers: use cones to break materials in a circular motion.
- Impact crushers: use hammers or hammer bars to break materials by rotating at high speeds.
Each type excels in specific situations. Örneğin, çeneli kırıcılar (applications) excel at hard rock mining. Impact crushers are better for softer materials such as limestone.
The Hidden Cost of Primary Crusher Selection
1. Upfront vs. Lifetime Costs
A 2023 study by MiningTech Analytics compared jaw and gyratory crushers across 12 Canadian copper mines:
- Çeneli kırıcılar: 1.2Minitialcost, 180k/year maintenance
- Gyratory crushers: 2.8Minitialcost, 420k/year maintenance
Key insight: Jaw units saved $1.3M per 5-year lifecycle despite lower hourly capacity (600 vs 1,200 tph).
2. The Mobility Requirements
Norway’s LNS Gruppen revolutionized temporary mining sites using mobile jaw crusher:
- 48-hour setup vs 3 weeks for fixed gyratory systems
- Fuel efficiency: 22L/h vs 55L/h for equivalent impact crushers
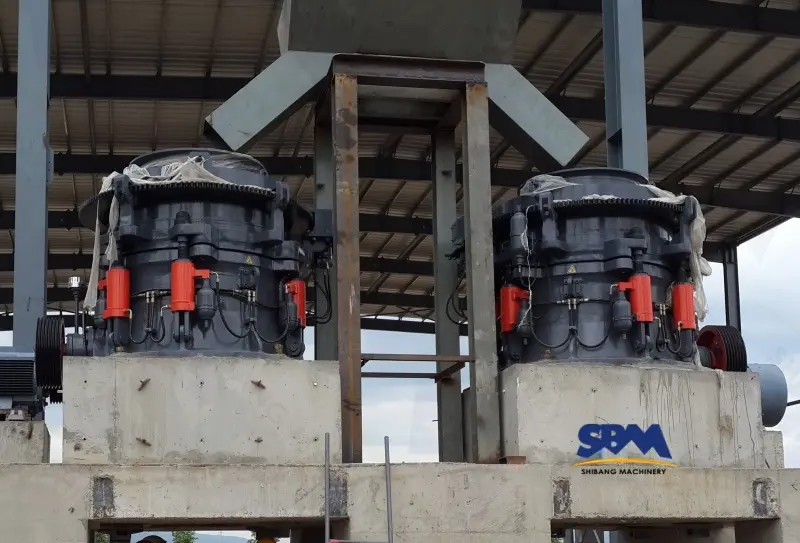
Jaw Crushers vs. Cone Crushers: A Clash of Titans
1. Çalışma prensibi
- Jaw Crushers: Rely on compression to break materials.
- Cone Crushers: Use rotating mantle and concave liners to apply pressure and shear force.
2. Material Handling
- Çeneli kırıcılar excel with hard, brittle materials (Örn., kuvars, bazalt).
- Konik kırıcılar are better for medium-hard to hard rocks (Örn., kireçtaşı, dolomit) and produce finer outputs.
3. Cost Comparison
While cone crushers offer higher reduction ratios, their upfront costs and maintenance expenses are steeper. Örneğin, a cone crusher in Australia’s iron ore mines costs 40% more to operate annually than a jaw crusher, despite its superior output.
Impact Crushers vs. Çene kırıcılar: Speed vs. Strength
1. Verim
- Impact Crushers: Use rotating hammers to shatter materials through impact. Ideal for softer, fibrous materials like limestone or coal.
- Jaw Crushers: Better for tough, dense materials requiring heavy compression.
2. Applications
In Western Australia’s mining sector, impact crushers are preferred for processing coal, where particle shape matters. Bu sırada, jaw crushers handle the initial crushing of hard rock before feeding secondary crushers.
3. Drawbacks
Impact crushers generate more dust and noise, raising environmental concerns. Çeneli kırıcılar, while quieter, require periodic replacement of jaw plates.
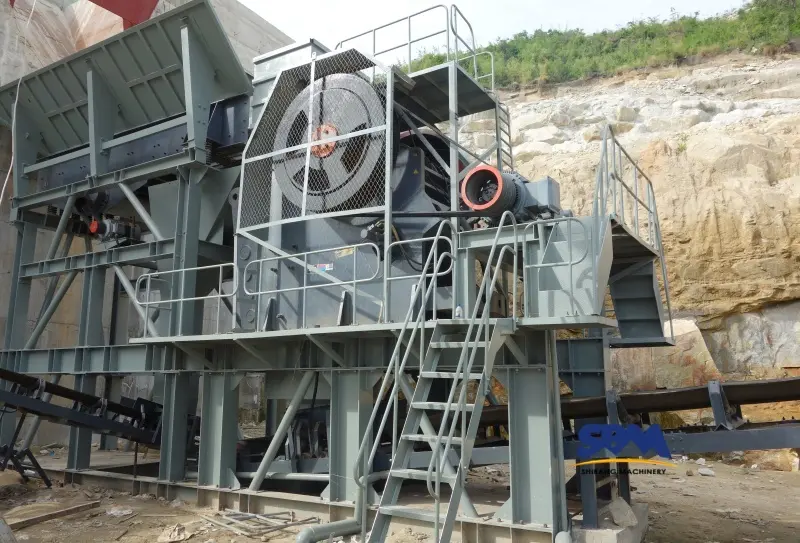
Çene kırıcı vs. Alternatives: 2 Unexpected Battlegrounds
Battle 1: Wet Material Processing
Conventional wisdom: Impact crushers dominate here
Reality: South Africa’s De Beers Group modified jaw crushers with heated plates to process diamond-bearing kimberlite at 18% moisture content.
Technical hack:
- Added tungsten carbide inserts on jaw plates (one of Key Jaw Crusher Components)
- Reduced downtime from 6 hours/day to 45 dakika
Battle 2: Ultra-Hard Rock Crushing
Chile’s Codelco Andina mine tested three crushers on copper porphyry (320 MPa hardness):
Metric | Çene kırıcı | Gyratory | Darbeli kırıcı |
---|---|---|---|
Wear part cost | $0.18/ton | $0.31/ton | $0.42/ton |
Energy use | 2.1 kWh/t | 1.8 kWh/t | 3.4 kWh/t |
Çözüm: Jaw crushers offered best total cost despite higher energy use.
When to Choose Alternatives: Data-Driven Exceptions
Dava 1: High-Volume Oil Sands (Alberta, Canada)
Syncrude’s Aurora Mine uses gyratory crushers for:
- Continuous 14,000 tph processing
- Automated tramp iron protection
Why not jaw crushers?
- Gereklilikler 6+ units for equivalent capacity
- Higher per-ton maintenance costs at scale
Dava 2: Urban Concrete Recycling (Tokyo, Japan)
Taisei Corporation’s mobile impact crushers:
- Process 500 tph of mixed demolition waste
- Magnetic separators remove rebar automatically
Jaw crusher limitation:
- No built-in separation for contaminants
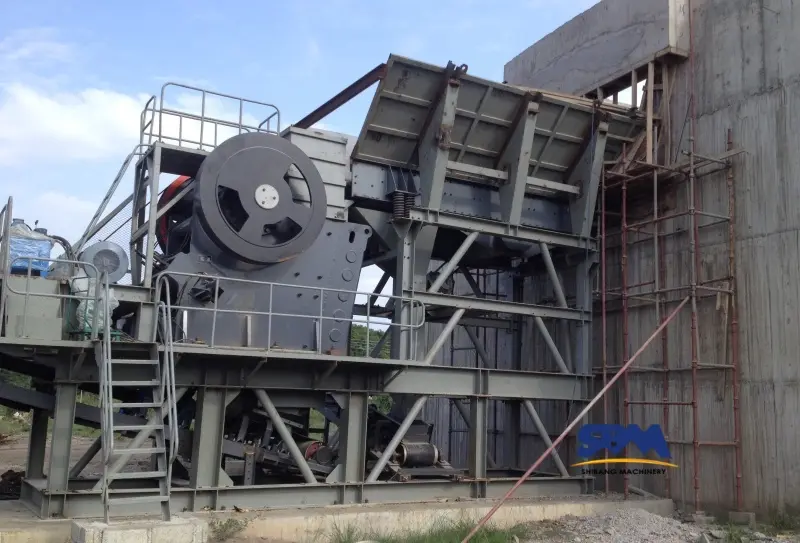
Global Vaka Çalışmaları: Jaw Crushers in Action
Dava 1: Iron Ore Processing in Australia
A Pilbara mining operation replaced its aging gyratory crushers with sbm jaw crushers. The result? A 20% reduction in energy costs and streamlined maintenance due to modular components.
Dava 2: Marampa Iron Ore Project (Sierra Leone)
A 900-tonne gyratory crusher was integrated with jaw crushers to process high-grade iron ore. The jaw crushers handled primary crushing, reducing feed size from 1.2m to 150mm, ensuring smooth downstream processing.
Dava 3: Cayman Islands Quarry
The Ironshore Quarry uses a customized jaw crusher to process tough limestone. Its robust design minimizes downtime, critical for remote island operations.
Beyond the Spec Sheet
While jaw crushers dominate hard rock scenarios, smart operators blend equipment:
- Use jaw units for primary reduction
- Add components of impact crushers for final shaping
- Integrate mobile units for flexible operations
The true advantage lies in jaw crushers’ adaptability – from heated plates in diamond mines to AI-driven maintenance in copper operations. As mining faces tougher ores and tighter margins, this versatility cements their role as the unshakable foundation of mining.
Genel Müdürlük
Naber:+8615225176731
E-posta: satış@mill-sbm.com
Adres: HAYIR. 1688, Gaoke Doğu Yolu, Pudong yeni bölge, Şanghay, Çin.
İnternet sitesi: https://www.mill-sbm.com/
Makale İçeriği
yakın zamanda Gönderilenler
- Gold Ore Processing: Jaw Crusher EfficiencyEffective gold ore processing hinges on precise crushing operations, where jaw crushers convert rugged deposits into optimized feedstock. Discover how to fine-tune these machines for peak productivity without compromising worksite…
- Çene kırıcılarla ezici nehir çakılModern inşaatın temel taşı, River Gravel, yollar için eşsiz tokluk ve uyarlanabilirlik sağlar, beton, ve erozyon kontrolü. Yine de sağlam, Düzensiz doğa, katlanmak için inşa edilen makinelerin gerektirdiği - çene kırıcılara girin.…
- Endüstriniz için doğru çene kırıcı boyutunu nasıl seçersiniz??Doğru çene kırıcı boyutunu seçmek bir tahmin oyunu değildir - malzeme dinamikleri ve operasyonel hesaplardan kaynaklanan bir bilimdir. Sabit kaya madenciliğinden kentsel beton geri dönüşümüne kadar sektörler için, Hatta bir…