E-posta: satış@mill-sbm.com
Tek geçiş vs çift geçiş çene kırıcılar: Hızlı bir karşılaştırma
Toplam üretim ve mineral madenciliği gibi temel endüstriyel alanlarda, Tek geçiş ile çift geçiş çene kırıcıları arasındaki yapısal farklılıklar, ekipman seçim stratejisini doğrudan belirleyin. The comparative analysis of the two in terms of crushing efficiency, maintenance cost and applicable scenarios has become a core issue in the industry’s technical optimization. Örneğin, the single-joint model achieves a lightweight design by simplifying the transmission system. The double-joint model enhances the processing capacity of high-hardness materials through a symmetrical mechanical structure. This division of technical paths has a profound impact on the selection logic of mining equipment. Engineers must rigorously evaluate their unique structural architecture, motion characteristics, and operating efficiency parameters to meet material processing requirements. This analysis will provide an in-depth analysis of their mechanical principles, energy consumption curves, and application-specific performance indicators to optimize equipment selection.
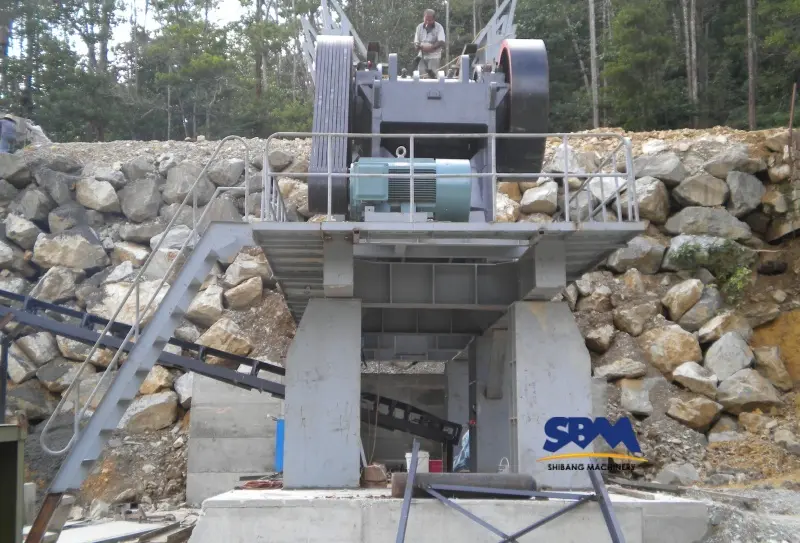
How Toggle Mechanisms Define Crusher Performance
At the heart of jaw crushers lies the toggle mechanism, which determines motion patterns and crushing efficiency. Here’s how each design operates:
1. Tek geçiş çene kırıcı: Simplicity with Limitations
The single toggle crusher uses a single set of toggles and an eccentric shaft to drive the movable jaw. Its simplified design allows for:
- Elliptical motion at the bottom of the jaw, enhancing material discharge.
- Higher speed but limited compressive force, ideal for medium-hard materials like limestone or coal.
- Lower cost and easier maintenance due to fewer components.
Vaka çalışması: In Australia’s limestone quarries, single toggle crushers like the PE çeneli kırıcı series are favored for their agility in processing raw materials with moderate abrasiveness.
2. Double Toggle Jaw Crusher: Robustness for Hard Materials
The double toggle design employs two sets of toggles and a more complex linkage system. Key advantages include:
- Purely vertical motion, generating greater compressive force to crush hard, abrasive rocks like granite.
- Reduced wear on jaw plates due to balanced force distribution.
- Higher energy consumption but superior durability in heavy-duty applications.
Vaka çalışması: A U.S. granite quarry achieved a 15% increase in crushed stone output by switching to a double toggle crusher for primary crushing.
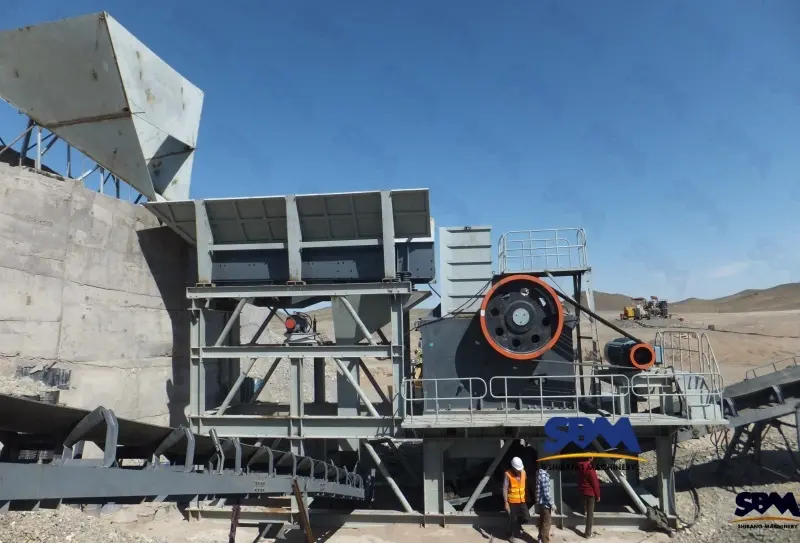
Critical Differences in Design and Functionality
Feature | Single Toggle | Double Toggle |
---|---|---|
Toggle Mechanism | One toggle plate + eccentric shaft | Two toggle plates + pivot point |
Jaw Motion | Elliptical at the bottom | Vertical and linear |
Crushing Force | Moderate | Yüksek |
Best For | Soft to medium-hard materials | Extremely hard, abrasive rocks |
Maintenance | Lower cost, frequent adjustments | Higher cost, longer intervals |
For projects requiring versatility, explore how impact crusher vs jaw crusher technologies complement each other in multi-stage crushing systems.
Choosing the Right Crusher: Factors to Consider
1. Material Hardness
- Single toggle crushers excel with limestone, kömür, or recycled concrete due to their shearing and attrition actions.
- Double toggle models dominate in iron ore or basalt processing, where high compression is critical.
2. Production Capacity
Crusher Type | Tek geçiş çene kırıcı | Double Toggle Jaw Crusher |
---|---|---|
Kapasite | 200–300 T/H | kadar 600 T/H |
Application | small to mid-scale aggregate production | large mining operations |
3. Operational Costs
- Single toggle units have lower upfront costs but may incur higher wear-part replacement expenses.
- Double toggle crushers offer longer component lifespans, reducing downtime in high-abrasion environments.

Industrial Applications: When to Choose Which?
Single Toggle Crushers
- Best for: Hard, abrasive materials (Örn., bazalt, quartzite).
- Use cases: Mobile crushing plants, PE jaw crusher setups for urban construction projects.
- Örnek: A South African quarry used a single toggle crusher to boost crushed stones output by 25% for roadbase production10.
Double Toggle Crushers
- Best for: Soft to medium-hard rocks (Örn., kumtaşı, shale).
- Use cases: Stationary plants, high-volume aggregate production requiring minimal wear.
- Örnek: A U.S. cement plant reduced maintenance costs by 40% after switching to a double toggle system for limestone crushing.
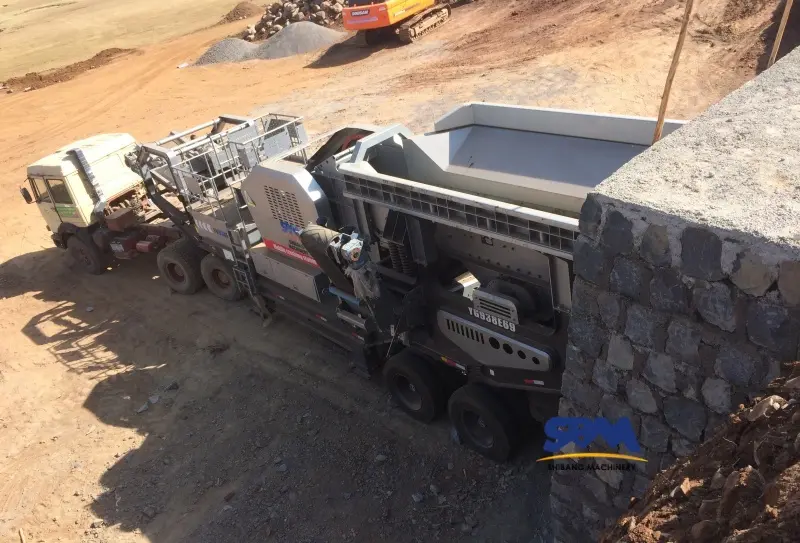
Understanding the distinction between single toggle vs double toggle jaw crushers ensures optimal equipment selection for your raw material type and production goals. While single toggle designs prioritize cost-efficiency for softer materials, double toggle crushers deliver unmatched power in hard-rock environments. For tailored solutions, consult manufacturers offering both PE jaw crusher and heavy-duty toggle models to balance performance and budget.
Genel Müdürlük
Naber:+8615225176731
E-posta: satış@mill-sbm.com
Adres: HAYIR. 1688, Gaoke Doğu Yolu, Pudong yeni bölge, Şanghay, Çin.
İnternet sitesi: https://www.mill-sbm.com/
Makale İçeriği
yakın zamanda Gönderilenler
- Tek geçiş vs çift geçiş çene kırıcılar: Hızlı bir karşılaştırmaToplam üretim ve mineral madenciliği gibi temel endüstriyel alanlarda, Tek geçiş ile çift geçiş çene kırıcıları arasındaki yapısal farklılıklar, ekipman seçim stratejisini doğrudan belirleyin. Karşılaştırmalı…
- Bir çene kırıcının hayatı nedir? Anahtar faktörler & Bakım İpuçlarıBir çene kırıcının servis ömrü genellikle 5-15 yıl, ve ömrü, ekipman kullanımının yoğunluğunun birleşik etkilerine tabidir., Bakım sistemi ve çalışma…
- Aşkın Ötesinde: Çene kırıcıları için çevresel etkiler ve çözümlerAvustralya demir cevheri madenlerinden Norveç granit ocaklarına kadar, çene kırıcıların çevresel etkileri – gürültü, toz, Enerji gereksinimleri ve atık – küresel tartışmaya yol açtı. Madencilik olarak…