E-mail: [email protected]
What is the ideal jaw crusher for granite crushing?
Granite’s relentless toughness demands jaw crusher built to endure—think armored jaws and unyielding frames. Prioritize crushers that combine brute force with precision engineering, like heat-treated alloys and adaptive crushing chambers. Dưới, we dissect industry-leading models and their battlefield-proven innovations, from Chilean mines to Norwegian quarries, to pinpoint what truly drives granite-crushing efficiency.
Why Jaw Crusher Is Essential for Granite Crushing?
Granite’s density and compressive strength make jaw crushers the go-to choice—their mechanical compression crushes rock more efficiently than impact crushers’ rapid spinning. While impact models pulverize with momentum, jaw units rely on a powerful squeezing action to fracture granite into precise, workable fragments.
Challenges of Crushing Granite: Why Standard Crushers Fall Short?
Granite’s quartz-packed structure sits stubbornly at 6-7 Mohs—outmuscling concrete and limestone like a heavyweight. Witness Indonesia’s Bangka Island mines: standard crushers crumble like stale bread here, their jaw plates surrendering within months to granite’s grit, bleeding operations dry with weekly shutdowns and $25k+ monthly part replacements. Here’s where specialized granite-focused jaw crushers shine:
- High manganese steel jaws resist abrasion.
- Optimized crushing chambers handle irregular slab shapes.
- Advanced hydraulic systems adjust output sizes efficiently.
Interested in versatile applications? See how the C6X excels atcrushing concrete and hard stone.
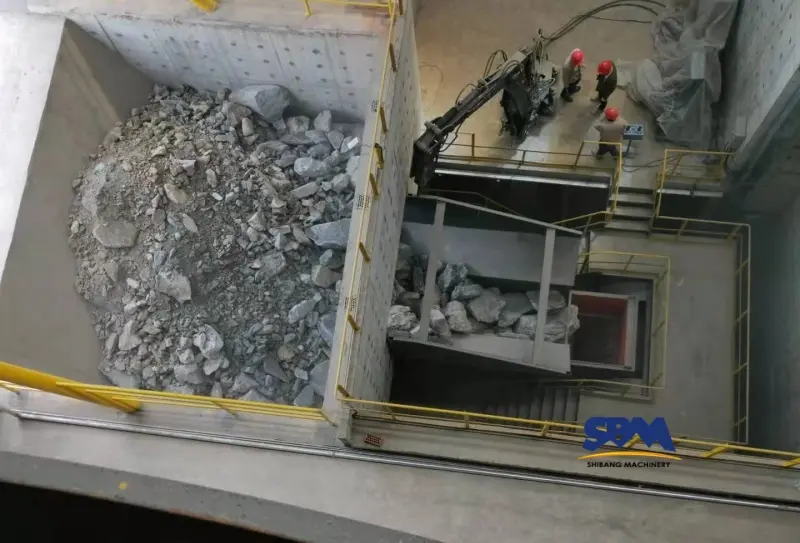
Top 5 Jaw Crushers for Granite Crushing
1. C6X Series Jaw Crusher
Các Máy nghiền hàm C6X dominates granite quarries with its hard-rock whisperer design—monster-sized 2,000mm feed openings devour slabs while maintaining 1,510 t/h throughput. Proven in South Africa’s Mpumalanga mines, its wave-patterned jaw plates and split-frame engineering turn brutal granite into profit-generating aggregate without breaking a sweat.
Features:
- Heavy-duty eccentric shaft: Reduces vibration and extends service life.
- Hydraulic adjustment system: Simplifies discharge port settings.
- Case Study: A South African quarry reduced energy consumption by 20% using the C6X jaw crusher for granite pre-crushing.
Ideal For: High-volume projects requiring consistent output.
2. PEW European Version Jaw Crusher
Designed for medium-to-hard materials, the Máy nghiền hàm PEW combines efficiency with user-friendly operation. Its deep crushing cavity increases material retention time, ensuring uniform particle size.
Key Specs:
- Feed size: Up to 630 mm.
- Crushing ratio: 3:1 ĐẾN 6:1.
- Applications: Granite aggregate production in European construction sites.
Why Choose It?:
- Low noise and vibration for urban environments.
- Modular design for easy maintenance.
3. Hammer Mill Crusher for Supplementary Crushing
While jaw crusher handles primary crushing, hammer mills excel in secondary processing. They reduce granite fragments to fine aggregates using high-speed rotating hammers.
Benefits:
- Versatile feed sizes: Accommodates 50–1,500 mm inputs.
- Adjustable output: Fine-tune granularity via grate gaps.
- Case Study: A German recycling plant achieved 95% material recovery using a hammer mill for granite waste.
Best For: Mixed-material recycling or fine-grinding needs.
4. Mobile Jaw Crusher Units
For on-site flexibility, mobile jaw crushers integrate crushing and screening systems. These units are ideal for remote quarries or urban projects with space constraints.
Features:
- All-in-one design: Thầm yêu, sàng lọc, and conveying in one unit.
- Fuel efficiency: Diesel-powered engines with low emissions.
- Applications: Road construction in Australia’s outback2.
5. Jaw Crusher Components & Spare Parts
A well-maintained crusher requires quality components. Key parts include:
- Jaw Plates: High-manganese steel (Mn13) for wear resistance.
- Bearings: Lubricated for reduced friction.
- Toggles & Bolts: Reinforced for heavy loads.
Replacement Tips:
- Monitor wear patterns monthly.
- Use OEM parts for compatibility (ví dụ., Jaw crushers spare parts from trusted suppliers)
Case Study: Australian Quarry Doubles Output
A granite quarry in New South Wales replaced their older crushers with a C6X unit paired with ahammer mill crusher for secondary processing. Results:
- 95% reduction in unplanned downtime.
- 40% longer lifespan ofjaw crushers spare parts due to reduced metal fatigue.
- Output size consistency improved by 22%.
Maintenance Tips for Long-Lasting Granite Crushers
Even thebest jaw crusher for granite crushing needs care. Pro tips from Brazilian operators:
- Lubricate bearings every 50 operational hours.
- Rotate or replacejaw plates once wear exceeds 20%.
- Use laser alignment tools to check frame integrity biannually.
Stock up on genuinejaw crusher components to avoid counterfeit parts.
Jaw Crushers vs. Hammer Mills: When to Choose Which
Trong khihammer mill crushers work well for softer materials like coal, jaw crushers dominate granite processing. Key differences:
Feature | máy nghiền hàm | Hammer Mill |
---|---|---|
Best For | Hard, abrasive rock | Brittle materials |
Maintenance Cost | Lower long-term | Higher (hammers) |
Output Size Control | Precise adjustment | Limited by grates |
Investing in the Right Crusher
Choosing thebest jaw crusher for granite crushing means balancing upfront costs with long-term efficiency. Models like the C6X offer modularity and smart engineering, while proper maintenance ofjaw crushers spare parts ensures decades of reliable service.
Explore our guide tohammer mill crusher applications for secondary crushing needs.
trụ sở văn phòng
Whatsapp:+8615225176731
E-mail: [email protected]
Địa chỉ: KHÔNG. 1688, Đường Đông Gaoke, quận mới Phố Đông, Thượng Hải, Trung Quốc.
Trang mạng: https://www.mill-sbm.com/
Nội dung bài viết
Bài viết gần đây
- What are the causes of damage to the jaw crusher plate?Because it is under tremendous pressure during material processing, there are many causes for the damage of the jaw crusher plate. Understanding why they degrade prematurely can save costs and…
- What is the ideal jaw crusher for granite crushing?Granite’s relentless toughness demands jaw crusher built to endure—think armored jaws and unyielding frames. Prioritize crushers that combine brute force with precision engineering, like heat-treated alloys and adaptive crushing chambers.…
- Jaw Crusher for Limestone Processing: A Guide to EfficiencyAs limestone is widely used in construction and industry, its processing requires strong and durable jaw crusher to meet the needs of the industry. Among the many crushers, the jaw…